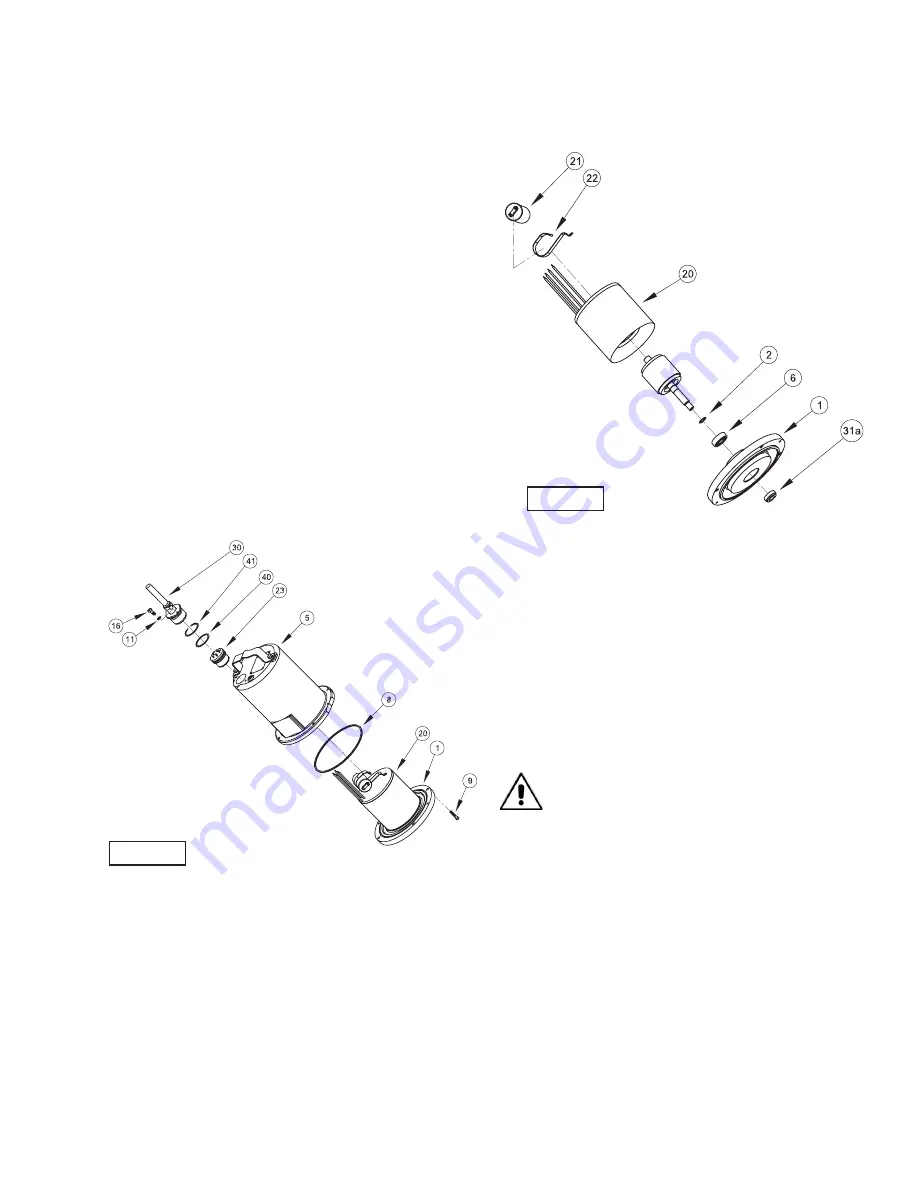
9
F-2) Impeller and Volute Service:
F-2.1) Disassembly and Inspection:
To clean out volute (24) or replace impeller (29), disconnect
power, remove screws (12), and lockwashers (11), vertically
lift motor and seal plate assembly from volute (24). Clean
out volute if necessary. Clean and examine impeller (29), for
pitting or wear and replace if required, inspect gasket (10)
and replace if cut or damaged. If the impeller (29) needs
replacing, remove nut (3), place a fl at screwdriver in the
slot of the end of the shaft to hold the shaft stationary while
unscrewing the impeller (29). (See Figure 11 or 12)
F-2.2) Reassembly:
To install impeller (29), screw impeller onto the shaft hand tight.
Clean the threads with Loctite cleaner. Apply thread locking
compound to shaft threads and install nut (3). Torque to 40
ft. lbs. Rotate impeller to check for binding. Position gasket
(10) on volute fl ange and position impeller and motor housing
on volute (24). Position lockwashers (11) on cap screws (12)
and screw into volute (24). Torque to 8 ft. lbs. Check for free
rotation of motor and impeller. (See Figure 11 or 12)
F-3) Motor and Bearing Service:
F-3.1) Disassembly and Inspection:
To examine or replace the motor (20), capacitor (21, single
phase units), and bearing (6), drain oil from motor as outlined
in paragraph F-1.2. Disassemble volute and impeller as
outlined in paragraph F-2.1 and disassemble shaft seal as
outlined in paragraph F-4.1. (See Figure 3, 4, and 11)
Position unit upright, using blocks to avoid resting unit on
shaft. Unscrew cable hex bolts (16) and remove compression
fl ange (30a) and power cord (30). Remove snap ring (41) with
a fl at head screwdriver. Pull the terminal block (23) out of the
housing (5) using a T-bolt or pair of pliers and a 1/4”-20 screw
in the threads of the terminal block (23). Be sure to leave
slack on the motor leads connected underneath. Use needle
nose pliers to pull each female connector off of the pins on
the underside of the terminal block (23) (see Figure 5). The
unit voltage should be noted. Repeat cable and terminal block
removal procedure for any control cables (32) if equipped.
Remove socket head cap screws (9). Vertically lift the motor
housing (5) from seal plate (1) by lifting handle (17). Inspect
square ring (8) for damage or cuts. Remove the motor bolts
and lift motor stator from seal plate (1). Disconnect capacitor
leads from capacitor (21, single phase units). Examine
bearing (6) and replace if required. If replacement is required,
remove bearing (6) from motor shaft using a wheel puller or
arbor press, see Figure 4.
Check motor capacitor (21, single phase units) with an
Ohm meter by fi rst grounding the capacitor by placing
a screwdriver across both terminals and then removing
screwdriver. Connect Ohm meter (set on high scale) to
terminals. If needle moves to infi nity (∞) then drifts back,
the capacitor is good. If needle does not move or moves to
infi nity (∞) and does not drift back, replace capacitor (21).
To test the temperature sensor (P1 / P2, optional), check for
continuity between the wire leads (see Figure 10). If found
to be defective, contact a motor service station or Barnes
Pumps Service department. Inspect motor winding for shorts
and check resistance values. Check rotor for wear. If rotor or
the stator windings are defective, the complete motor must be
replaced.
IMPORTANT! - All parts must be clean before
reassembly.
F-3.2) Reassembly:
Bearing - When replacing bearing, be careful not to damage
the rotor or shaft threads. Clean the shaft thoroughly. Apply
adhesive compound to the shaft and press bearing (6) on the
motor shaft, position squarely onto the shaft applying force to
the inner race of the bearing only, until bearing seats against
the retaining ring (2).
FIGURE 4
FIGURE 3