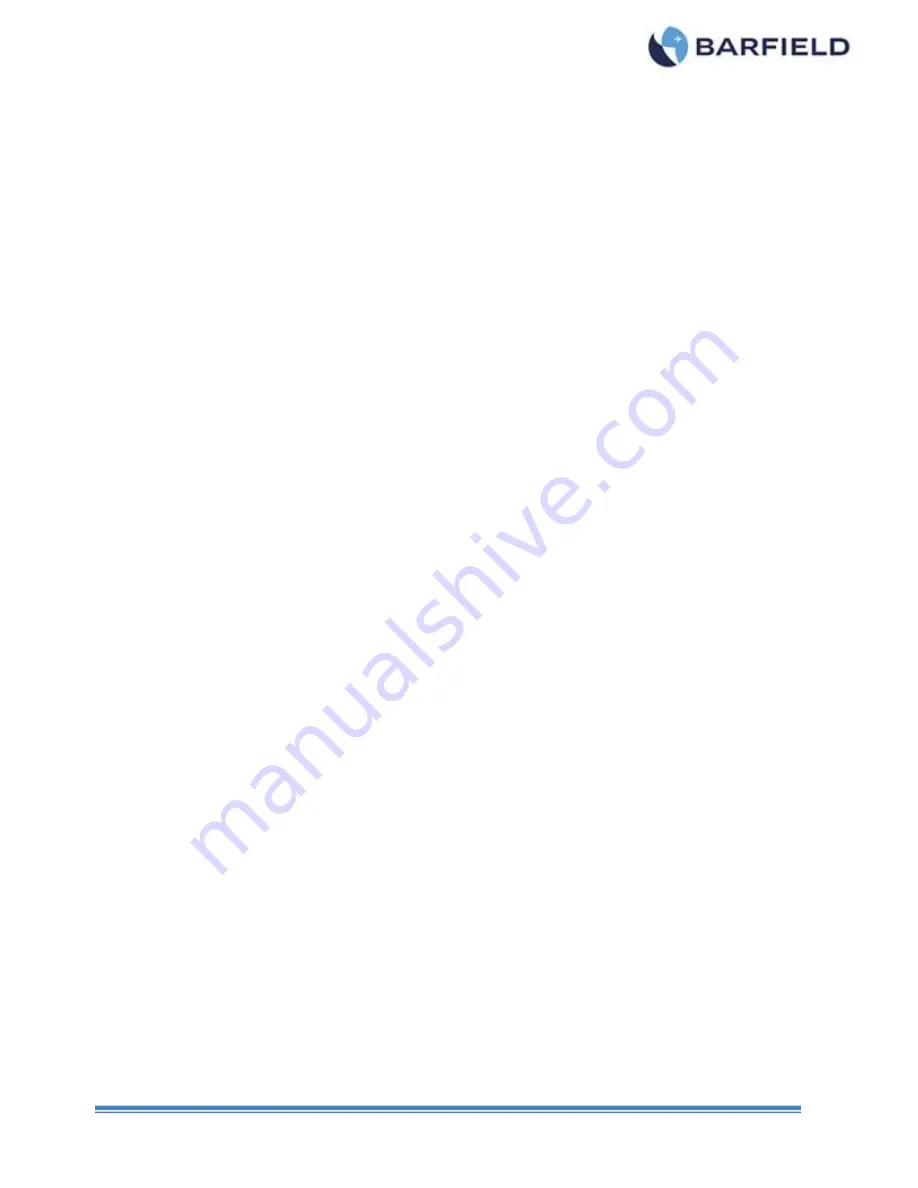
56-101-01178 Revision K
Page | 40
While in Leak Measure mode, the ALR “Auto Leak Recover” (if enabled) monitors the leak
rate of ROC and RtCAS. If the rates exceed the values defined under the Limits menu
(Example: with Limits=default, ALR for ROC = 1,000 ft/min and RtCAS= 25
kts/min) the Test Set will automatically switch into Control mode with the Target values set
to the current ALT and CAS values and the Test Set pneumatic controller will try to
overcome the leak and stabilize the pressures on the STATIC (Ps) and PITOT (Pt) ports.
When this occurs, there will be a message displayed “Excessive Leak Detected”.
The Leak Test ATP profiles are only available when the Display Setup is configured for
Aeronautical display mode. When the user selects Pressure or EPR “Engine Pressure
Ratio” display mode, the Leak Test ATP will not be available only the Leak Rate Timer
feature is available under these two display modes.
D. Control Mode
The Control mode on the 1811NG provides a two-channel pneumatic controller. The
1811NG controller is referred to as the PCM (Pneumatic Control Module). This module
provides an absolute pressure controller for the STATIC (Ps) channel and a differential
pressure controller for the PITOT (Pt) channel.
This two-channel precision controller is used to control and simulate the Target pressure
and vacuum set point conditions and rates as requested by the user setting Target set
points.
The pneumatic controller can control the STATIC (Ps) channel pressure with a resolution
of ~ 0.0002 inHg while maintaining/controlling the PITOT (Pt) channel differential pressure
with a pressure resolution of ~0.0004 inHg. The precession custom controller provides the
ability of maintain a constant CAS “Airspeed” (maintaining a constant differential pressure
with regards to the STATIC (Ps)) even during high rates of ROC enabling 0 kts CAS (the
most demanding control situation) to be well maintained under considerably high slew
rates of 6,000 ft/min and higher.
When the 1811NG transitions into
Control
mode, the display indicates “
Wait Resuming
Control
” during this transition period (~ 4 seconds) the PCM is responsible for establishing
the same controlled pressures as last measured on the STATIC (Ps) and PITOT (Pt) ports
while in Leak Measure mode. During the Leak Measure to Control transition, the Target set
points are always preloaded with the same value as the existing pressure measured on the
ports at the time the Control mode was selected.
The following internal control sequences occur:
1. The pressure presently on the STATIC (Ps) and PITOT (Pt) ports are measured and
recorded.
2. The output valves located internally on the 1811NG pneumatic control manifold
(SvPs_Out and SvPt_Out) are closed to isolate the pneumatic controller from the
aircraft or instrument under test. This is done to insure that no transient pressure
spikes are seen or impressed onto the UUT or aircraft while the internal control
manifold is establishing the same control pressures that was last measured on the
STATIC (Ps) and PITOT (Pt) ports, during this process the Test Set displays
“Wait
Resuming Control”. Once the PCM has established stable internal control vessel
pressures the output valves (SvPs_Out and SvPt_Out) are opened.