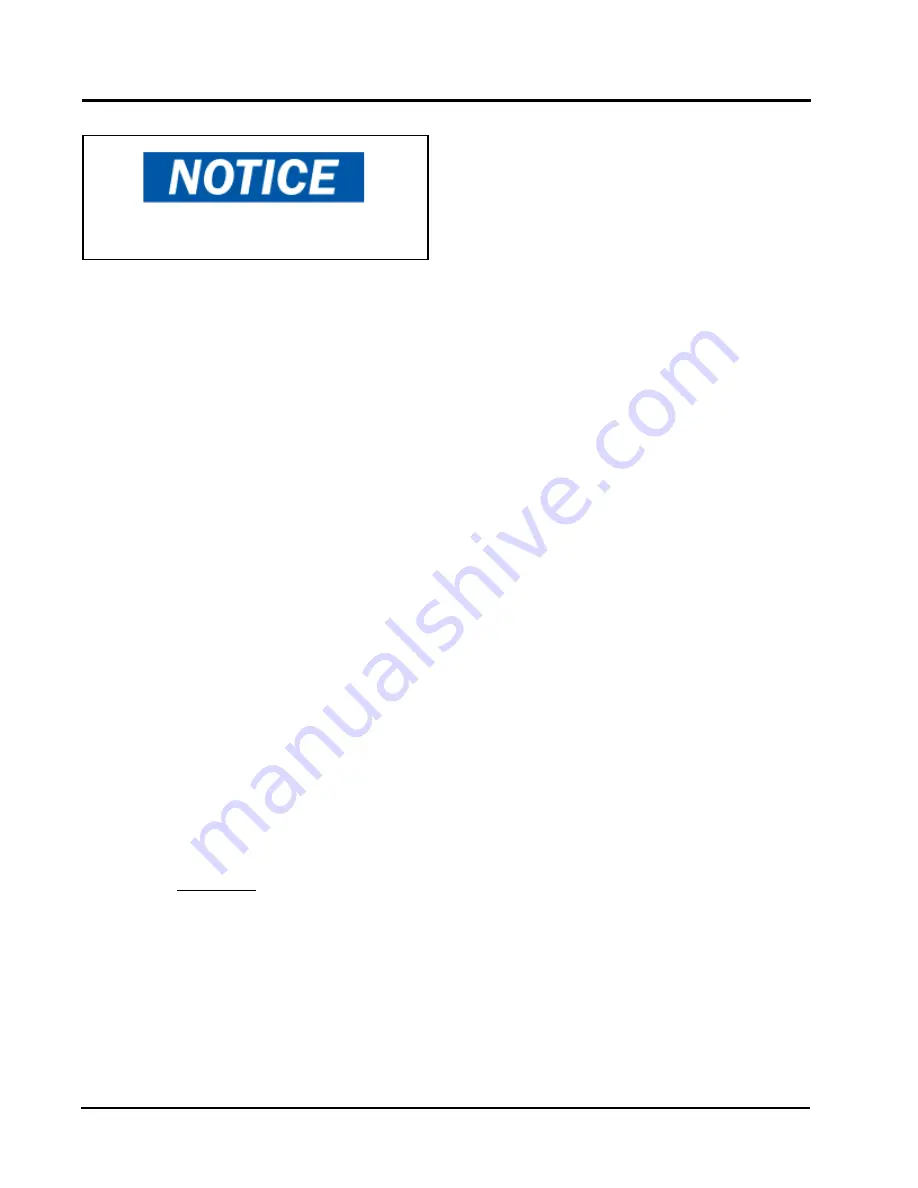
Manual 2100-695
Page
40 of 54
REFRIGERANT INFORMATION
General
1. Use separate service equipment to avoid cross
contamination of oil and refrigerants.
2. Use recovery equipment rated for R-410A
refrigerant.
3. Use manifold gauges rated for R-410A (800
PSI/250 PSI low).
4. R-410A is a binary blend of HFC-32 and HFC-
125.
5. R-410A is nearly azeotropic—similar to R-22 and
R-12. Although nearly azeotropic, charge with
liquid refrigerant.
6. R-410A operates at 40-70% higher pressure than
R-22, and systems designed for R-22 cannot
withstand this higher pressure.
7. R-410A has an ozone depletion potential of zero,
but must be reclaimed due to its global warming
potential.
8. R-410A compressors use polyol ester oil.
9. Polyol ester oil is hygroscopic; it will rapidly absorb
moisture and strongly hold this moisture in the oil.
10. A liquid line dryer must be used—even a deep
vacuum will not separate moisture from the oil.
11. Limit atmospheric exposure to 15 minutes.
12. If compressor removal is necessary, always plug
compressor immediately after removal. Purge with
small amount of nitrogen when inserting plugs.
Topping Off System Charge
If a leak has occurred in the system, Bard
Manufacturing recommends reclaiming, evacuating
(see criteria above) and charging to the nameplate
charge. If done correctly, topping off the system charge
can be done without problems.
With R-410A, there are no significant changes in the
refrigerant composition during multiple leaks and
recharges. R-410A refrigerant is close to being an
azeotropic blend (it behaves like a pure compound or
single component refrigerant). The remaining refrigerant
charge in the system may be used after leaks have
occurred. “Top-off” the charge by utilizing the pressure
charts on the inner control panel cover as a guideline.
REMEMBER:
When adding R-410A refrigerant, it must
come out of the charging cylinder/tank as a liquid to
avoid any fractionation and to insure optimal system
performance. Refer to instructions for the cylinder that
is being utilized for proper method of liquid extraction.
Safety Practices
1. Never mix R-410A with other refrigerants.
2. Use gloves and safety glasses. Polyol ester oils can
be irritating to the skin, and liquid refrigerant will
freeze the skin.
3. Never use air and R-410A to leak check; the
mixture may become flammable.
4. Do not inhale R-410A—the vapor attacks
the nervous system, creating dizziness, loss
of coordination and slurred speech. Cardiac
irregularities, unconsciousness and ultimately
death can result from breathing this concentration.
5. Do not burn R-410A. This decomposition produces
hazardous vapors. Evacuate the area if exposed.
6. Use only cylinders rated DOT4BA/4BW 400.
7. Never fill cylinders over 80% of total capacity.
8. Store cylinders in a cool area, out of direct
sunlight.
9. Never heat cylinders above 125°F.
10. Never trap liquid R-410A in manifold sets, gauge
lines or cylinders. R-410A expands significantly at
warmer temperatures. Once a cylinder or line is full
of liquid, any further rise in temperature will cause
it to burst.
Important Installer Note
For improved start-up performance, wash the indoor
coil with a dishwashing detergent.
R410-A Refrigerant Charge
This wall-mount unit was charged at the factory with
the quantity of refrigerant listed on the serial plate.
AHRI capacity and efficiency ratings were determined
by testing with this refrigerant charge quantity.
Table 10 shows nominal pressures for the units. Since
many installation specific situations can affect the
pressure readings, this information should only be used
by certified technicians as a guide for evaluating proper
system performance. They shall not be used to adjust
charge. If charge is in doubt, reclaim, evacuate and
recharge the wall-mount unit to the serial plate charge.
These units require R-410A refrigerant and
polyol ester oil.