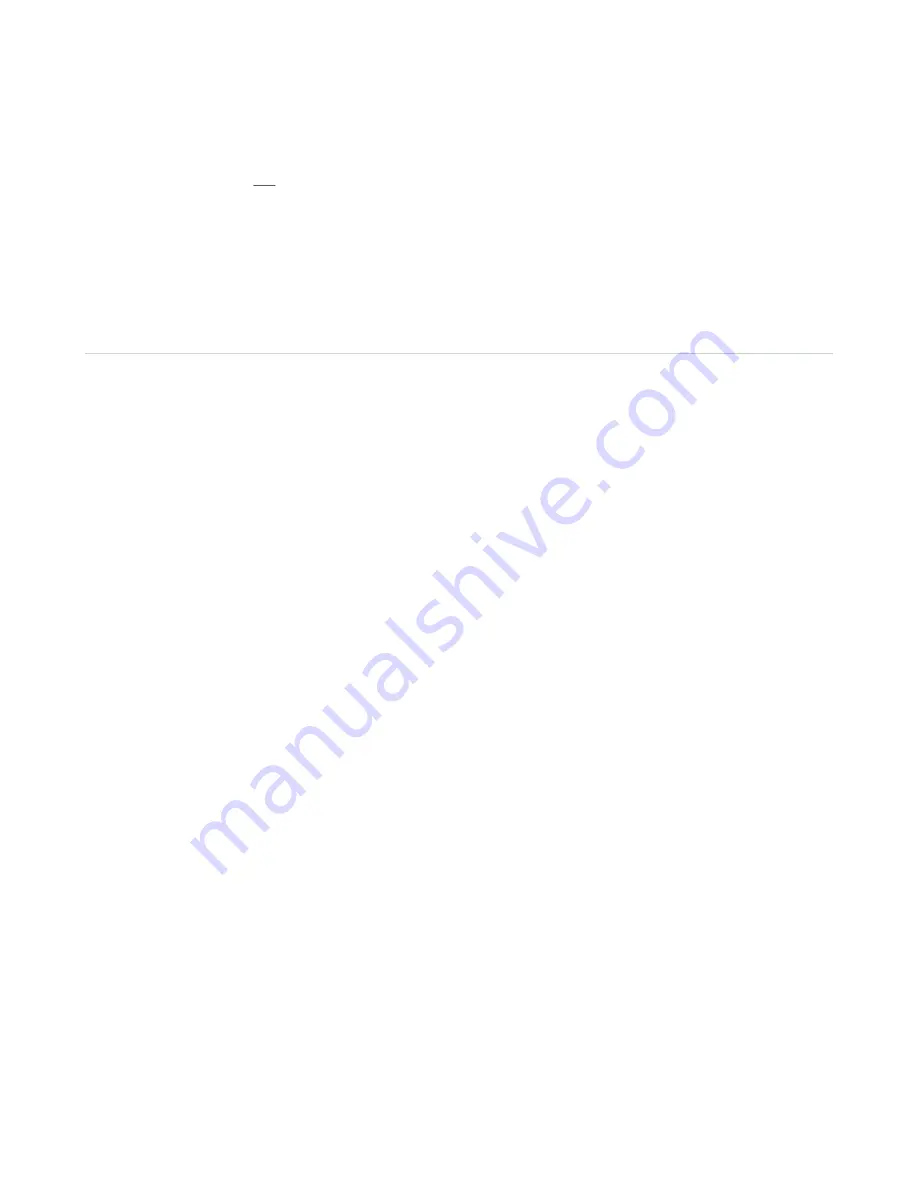
Track Output
Indicates the physical state of a particular Safety Output (On or Off).
Track Output Fault
Indicates when a particular Safety Output has a fault.
Track Output Fault All
Indicates a fault from any Safety Output.
Track Output Logical State
Indicates the logical state of a particular Safety Output. For example, the logical state is Off but the Safety Output
is in an Off-Delay and not physically off yet.
Waiting for Manual Reset
Indicates a particular configured reset is needed.
System Lockout
Indicates a Non-Operating Lockout Condition, for example unmapped input connected to 24 V.
6.8 Virtual Status Outputs
The Ethernet models of the Safety Controller can be configured for up to 64 virtual status outputs, using the PC Interface.
These outputs can communicate the same information as the Status Outputs over the network. See
on page 95 for more information. The Auto Configure function, located on the Industrial Ethernet tab of
the PC Interface, automatically configures the Virtual Status Outputs to a set of commonly used functions, based on the
current configuration. This function is best used after the configuration has been determined. Virtual Status Output
configuration can be manually revised after the Auto Configure function has been used. The information available over
the network is consistent with the logical state of the inputs and outputs within 100 ms for the Virtual Status Output tables
(viewable via the PC Interface) and within 1 second for the other tables. The logical state of inputs and outputs is
determined after all internal debounce and testing is complete. See
on page 45 for details on
configuring Virtual Status Outputs.
XS/SC26-2 Safety Controller
96
Содержание SC26-2 Series
Страница 1: ...XS SC26 2 Safety Controller Instruction Manual Original Instructions 174868 Rev E 20 June 2014 174868 ...
Страница 58: ...Figure 49 Run Time Equipment view Figure 50 Run Time Functional View XS SC26 2 Safety Controller 58 ...
Страница 62: ...Figure 54 Sample Configuration Functional View XS SC26 2 Safety Controller 62 ...