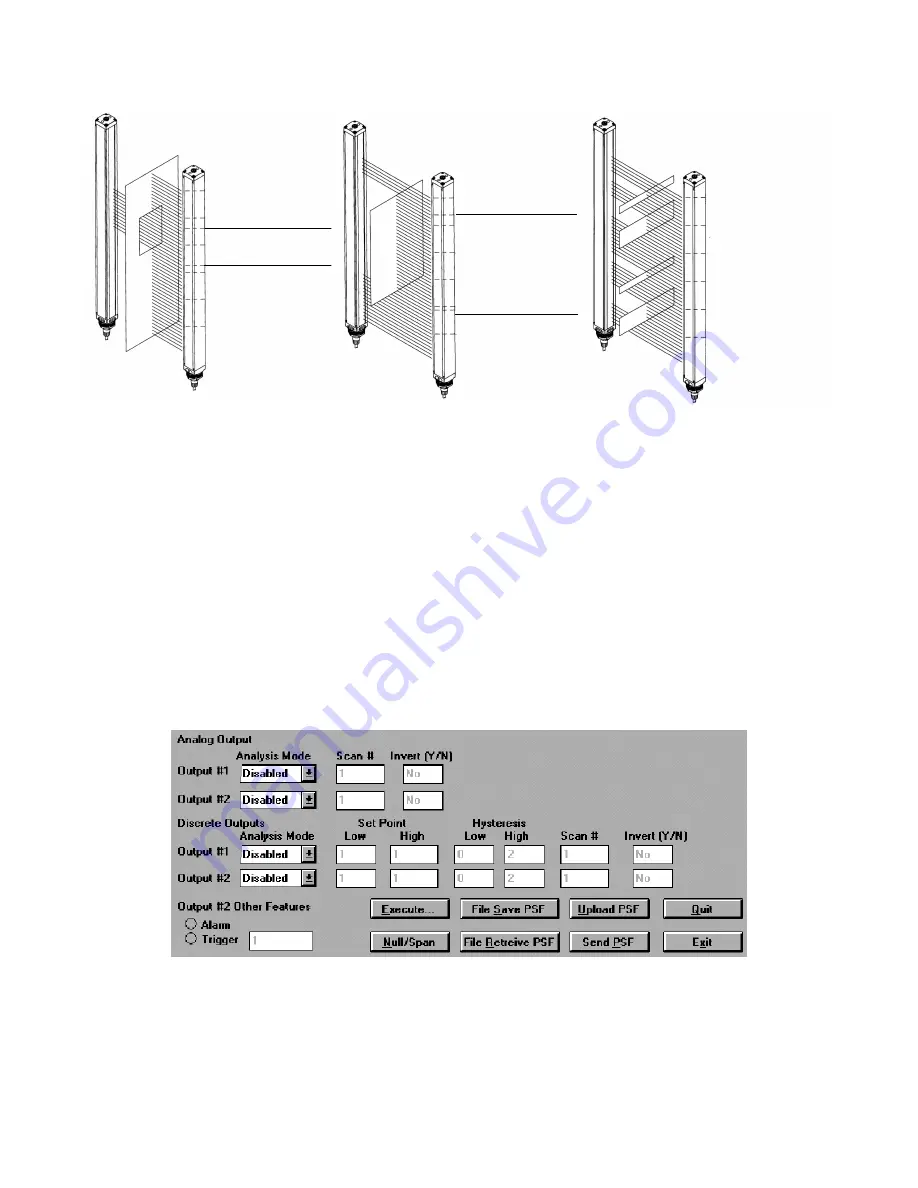
48 –
40 –
32 –
24 –
16 –
8 –
In Last Beam Made Mode,
last beam is #37 of 48.
In First Beam Made Mode,
first beam is #26 of 48.
Last Beam Made, First Beam Made
BMRL 3616A
Receiver
BMEL 3616A
Emitter
BMRL 3616A
Receiver
48 –
40 –
32 –
24 –
16 –
8 –
In Last Beam Blocked Mode,
last beam is #43 of 48.
In First Beam Blocked Mode,
first beam is #15 of 48.
Last Beam Blocked, First Beam Blocked
BMEL 3616A
Emitter
BMRL 3616A
Receiver
48 –
40 –
32 –
24 –
16 –
8 –
In Total Beams Made Mode,
34 of 48 possible beams are
made.
In Total Beams Blocked Mode,
14 of 48 possible beams are
blocked.
Total Beams Made, Total Beams Blocked
BMEL 3616A
Emitter
5.4.2
Configuring
the Outputs
The controller
offers
2, 3, or 16 outputs, depending on the model. One scan analysis mode may be assigned to Output 1 and a second,
different,
analysis mode may be assigned to Output 2. All models except the 16-output models have an output labeled Alarm. This
output can be
configured
to:
•
Function
as the alarm output for the controller’s
self-diagnostic
circuitry when a scan analysis mode is not assigned to it; or
• Serve as a trigger input to begin the scan sequence of another MINI-ARRAY System.
Configuring
the Discrete Outputs (MAC-1, MACP-1, MACN-1, MACV-1, and MACI-1)
Use the Output Assignments
section
of the PSF
Configuration
screen to customize the Analysis Mode(s) response. With the
exceptions
noted, either Meas1 or Meas2 can be assigned to Output 1 or Output 2.
Output 2 may be assigned as an Alarm output for the module’s
self-diagnostic
circuitry when a scan analysis mode is not assigned to it.
Output 2 can also be programmed to serve as a Trigger input to begin the scan sequence of another MINI-ARRAY System. The Trigger
value is the beam
location
along the array at which the Trigger output (during a scan) occurs.
Set Point (Low and High) determines where within the array the output(s) responds. In the case of total or
contiguous
beams made or
broken, these
settings
determine the minimum and maximum number of beams required for an output.
Hysteresis (Low and High) determines how much change must occur at each set point to cause the associated output to change state.
Hysteresis avoids unstable output
conditions
(chattering)
when the scanning
condition
exactly matches one of the set points. The
default
setting
for hysteresis is one beam less than the Low Set Point and one beam more than the High Set Point.
Scan # is the number of
consecutive
array scans required before the associated output is updated. The controller can be programmed
for from one to nine
consecutive
scans. The scan data MUST BE THE SAME for all
consecutive
scans before the associated output
updates.
Invert (Y/N) allows the output to be normally open (No) or normally closed (Yes).
A-GAGE
®
MINI-ARRAY
®
Measuring Light Screen System
www.bannerengineering.com - Tel: 763.544.3164
19