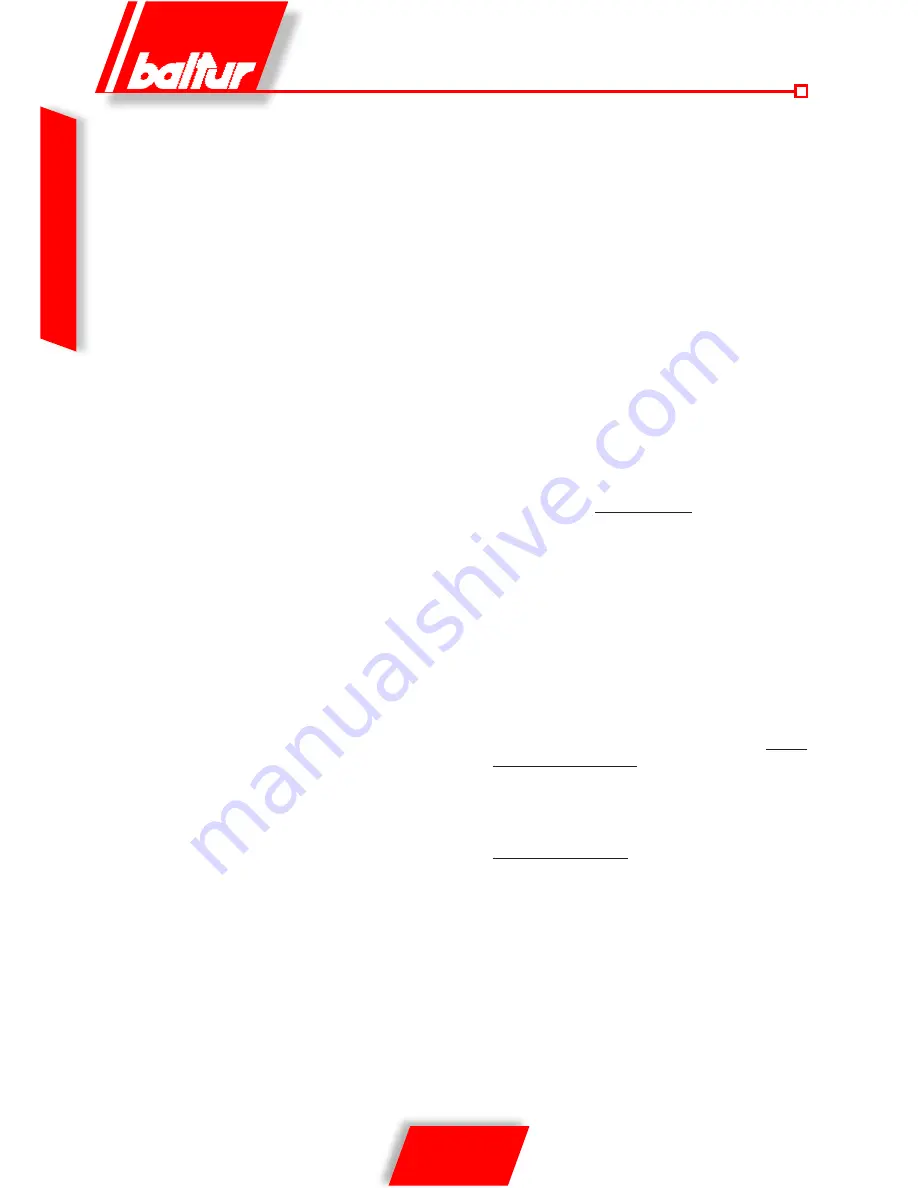
E
N
G
L
I
S
H
16 / 34
0006080766
- ignite the burner, adjust the quantity of gas and air
for the pilot flame and check for proper ignition
several times.
- when adjustment is over restore the original connections.
UV CELL
Detection of the pilot flame is effected by a UV cell: the
following information should be born in mind. Even slight
greasiness will compromise passage of the UV rays through
the UV photocell bulb, thus preventing the sensitive device
inside it receiving the quantity of radiation needed for correct
operation. If the bulb is smeared with light oil, heavy oil,
etc. it must be cleaned thoroughly. Note that even gentle
contact with fingers can leave a slight film of grease which
is sufficient to compromise proper UV photocell operation.
The UV cell does not “see” daylight or the light emitted by a
common bulb. A sensitivity check can be carried out using
a flame (lighter, candle) or the spark generated between the
electrodes of a common ignition transformer. To ensure proper
operation the UV cell current must be sufficiently stable and
must not drop below the minimum required by the specific con
-
trol box. It may be necessary to try different positions in order
to find the best one: do this by shifting (axial or rotary shift) the
body that contains the photocell with respect to the attachment
strap. The check is effected by connecting a micro-ammeter
(with suitable scale), in series, to one of the two UV photocell
connection wires; it is, of course, necessary to observe polarity
( + and - ). The cell current needed to ensure proper control
box operation is given on the wiring diagram.
17) When the burner is working at “minimum” adjust the air to
the quantity needed to ensure good combustion. Turn the
adjuster screws in or out at the point of contact with the lever
that transmits combustion air regulation damper movement.
The quantity of air at “minimum” should be a little scarce so
as to ensure perfect ignition even under the most demanding
circumstances.
18) After adjusting the air for the “minimum” turn the modulation
switches to position “MAN” and to position “MAX”.
19) The modulation motor starts moving: wait for the disk (on
which the adjuster screws are fitted) to sweep through an
angle of about 12° (this corresponds to the space taken up by
three screws) and then stop modulation by turning the switch
back to position “0”. Run a visual check on the flame and, if
necessary, regulate combustion air as described in point 17.
Then check combustion using the appropriate instruments
and, if necessary, correct the adjustment previously made
by way of visual check. The above-described operation must
be repeated by proceeding progressively (by advancing the
disk about 12° at a time) and, each time, modifying, where
necessary, the fuel-air ratio throughout the entire modulation
range. It is necessary to make sure that fuel feed progression
occurs gradually and that maximum fuel flow occurs at the
end of the modulation range. This condition is necessary for
attainment of smooth, gradual modulation. If necessary modify
the position of the fuel control screws to obtain that specified
above. Note that maximum flow is attained when return
pressure is about 2 - 3 bar less than delivery pressure (gene-
rally 20 - 22 bar). A correct air-fuel ratio should give a carbon
dioxide (CO
2
) value that increases as fuel flow increases: as
a rough guide, it should be at least 10% at minimum flow and
reach an optimum of about 13 % at maximum flow.
It is inadvisable to exceed a CO
2
figure of 13% so as to prevent
operation with a rather limited excess of air, possibly leading to
a significant increase in smoke number owing to unavoidable
causes (changes in atmospheric pressure, small dust depo-
sits in the fan air ducts etc.). The resulting smoke (i.e. fume)
number is closely linked to the type of fuel used (latest regu-
lations indicate n° 6 on the Bacharach scale as a maximum).
it is advisable, if possible, to keep the smoke number below
n° 6 on the Bacharach scale even if the CO
2
value could, as a
consequence, be slightly lower. Reduced opacity (i.e. a lower
smoke number) soils the boiler less and the average efficiency
of the latter is normally higher even if CO
2
levels are slightly
lower. Remember that to achieve proper adjustment system
water must be up to normal working temperature and that the
burner must have been working for at least fifteen minutes. In
the absence of proper instrumentation use fume colour as a
guide. We recommend that adjustment be effected so as to
obtain a light orange flame; avoid red flames with smoke and
white flames with an exaggerated excess of air.
20) The purpose of the air pressure switch is to place the control
box in lock-out (safety mode) if air pressure is incorrect. The
pressure switch must be adjusted so that it trips by closing the
N.O. (Normally Open) contact when air pressure in the burner
reaches a sufficient value. The pressure switch connection
circuit features self-control so it is necessary that the N.C.
(Normally Closed) contact (with fan at standstill and therefore
no air pressure in burner) actually brings about this condition. If
it does not the control box is not switched on (the burner stays
off). More precisely, note that if the contact designed to be clo-
sed when working fails to close (air pressure too low) then the
control box goes through its cycle but the ignition transformer
does not come on, the pilot flame gas valves stay closed and
the burner thus shuts down in “lock-out”. To check that the air
pressure switch is working properly it is necessary, with the
burner at minimum flow rate
to increase the adjustment value
until it trips: immediate burner “lock-out” must follow. Reset
the burner by pressing the appropriate button and adjust the
pressure switch to a value sufficient to detect the air pressure
during pre-ventilation.
21) The gas pressure switches (minimum and maximum) are desig-
ned to stop the burner working when gas pressure is outside the
set range. Given the specific function of the pressure switches it
is evident that the minimum pressure control switch must utilise
the closed contact when the pressure switch detects a pressure
higher than that to which it is set. It is also evident that the ma-
ximum pressure switch must utilise the closed contact when it
detects a pressure lower than that to which it is set. Adjustment
of minimum and maximum gas pressure switches must there-
fore be effected during burner testing as a function of actual
pressure at each individual installation. The pressure switches
are electrically connected in series; consequently, if any one of
the pressure switches trips (i.e. opening of the circuit) when the
burner is working (flame lit) the burner shuts down immediately.
When testing the burner it is extremely important to check
that pressure switches are working properly. Proper pressure
Содержание GI MIST 1000 DSPNM-D
Страница 36: ...75 84 0006080766 ...
Страница 37: ...76 84 0006080766 ...
Страница 38: ...77 84 0006080766 ...
Страница 39: ...78 84 0006080766 ...
Страница 40: ...79 84 0006080766 ...
Страница 41: ...80 84 0006080766 ...
Страница 42: ...81 84 0006080766 ...