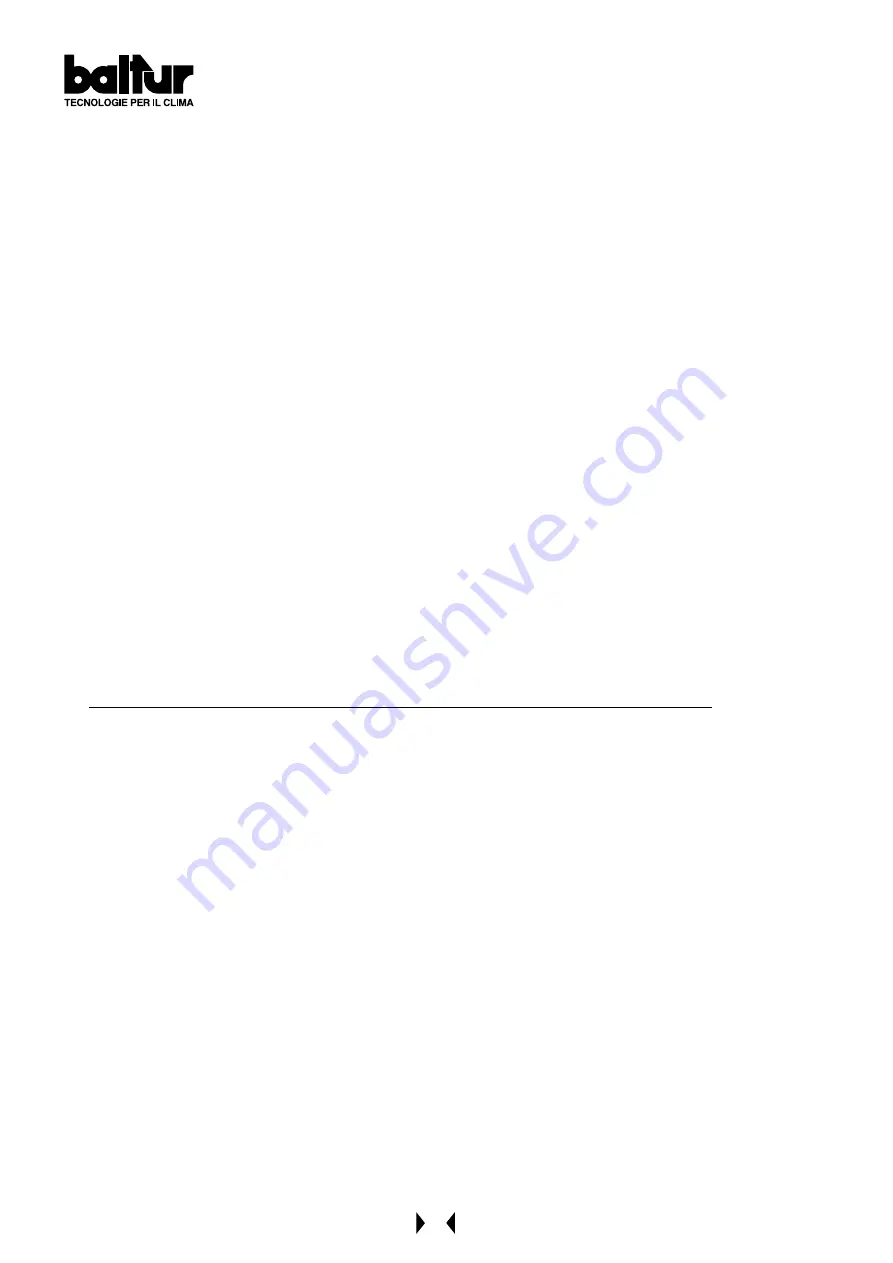
28
18) The servomotor which regulates the fuel/air delivery starts moving; wait until the disk on which the regulating
screws have been fitted, has reached an angle of about 12° (this corresponds to a space taken up by three
screws), stop the modulation and return the switch to the “O” position. Carry out a visual control of the flame
and proceed, if necessary, with regulating the combustion air by operating as described in point 16.
Subsequently, control combustion with the appropriate instruments and modify, if necessary, the previous
regulation carried out by visual control only. The operation described above should be repeated progressively
(by moving forwards the disk by about 12° at a time) and modifying every time, if necessary, the fuel/air ratio
during the entire modulation run. Make sure that the increase in fuel delivery occurs gradually and that maximum
delivery is reached at the end of the modulation run. This is necessary in order to ensure that modulation
functions with good graduality. The positions of the screws that commend the fuel may need to be modified in
order to obtain the graduality required. Maximum delivery is obtained when the return pressure is about 2 ÷ 3
bar less than the delivery pressure (normally 20 ÷ 22 bar). For a correct air/fuel ratio, the percentage of Carbon
Dioxide (CO
2
) should increase with the increase in delivery (at least 10% at minimum delivery to a maximum
of 13% at maximum delivery). We advise against exceeding 13% of CO
2
to avoid operating with a rather
limited excess of air which could cause a considerable increase in smoke opacity due to unavoidable
circumstances (a variation in the atmospheric pressure, presence of dust particles in the fan’s air ducts, etc.).
Smoke opacity depends on the type of fuel utilized (the most recent provisions indicate that it should not
exceed N° 2 of the Bacharach Scale). We advise, if possible, maintaining smoke opacity below N° 2 of the
Bacharach Scale, even if, as a consequence, the CO
2
value is slightly lower. The lower smoke opacity dirties
the boiler less and therefore its average yield is normally high even when the CO
2
value is slightly inferior.
It should be remembered that, in order to regulate properly, the water in the system should be at the right
temperature and the burner should have been operating for at least 15 minutes.
If the appropriate instruments are not available, judgement can be based on the colour of the flame.
We advise regulating in such a way as to obtain a flame bright orange in colour. Avoid a red flame with smoke
in it, or a white flame with an exaggerated excess of air. After having checked the air/fuel regulation, tighten the
locking screws of the adjustable screws.
19) Control that the modulation motor functions automatically by putting the AUT - O - MAN switch in the “AUT”
position and the MIN - O - MAX switch in the “O” position. In this way, modulation is activated exclusively by the
automatic command of the boiler’s probe, if the burner is a COMIST...MM (modulating) version, or on the
command of the thermostat or pressure switch of the 2nd stage, if the burner is a COMIST...DSPGN (two
stage progressive) version. (See Chapter “Electronic Potentiality Regulator RWF... for the modulating version).
Normally, it is not necessary to alter the internal settings of the Potentiality Regulator RWF... .
20) Check the efficiency of the flame detection device (photocell UV). The photoresistant cell is a flame control
device and, if the flame should be extinguished during operations, it must be capable of intervening (this
control should be made at least one minute after start up). The burner should be capable of blocking itself
(shut down), and remaining so, if the flame does not appear regularly during the start up phase within the time
limit preset on the control box. The shut down causes an immediate interception of the fuel, the burner comes
to a standstill and the red warning light comes on. To check the efficiency of the photocell UV and of the shut
down system, proceed as follows:
a) Start up the burner
b) after one minute, extract the photoresistant cell by pulling it out of its seat and simulate flame failure with
a dark cloth. The flame should be extinguished and the control box will repeat the ignition phase from the
beginning and, immediately after the flame appears, it will go to shut down.
c) The control box can only be unblocked by pressing manually on the appropriate pushbutton (unblocking).
To check the efficiency of the shut down device, carry out this control at least twice.
21) Check the efficiency of the boiler’s thermostats or pressure switches (this operation should stop the burner).
Содержание COMIST 122 DSPGM
Страница 9: ...9 COMIST 36 72 122 N 8187 1 Rev COMIST 180 250 300 N 8111 2 Rev...
Страница 22: ...22 N 0002900580 BALTUR PUMP...
Страница 46: ......
Страница 47: ......
Страница 48: ......
Страница 49: ......
Страница 50: ......
Страница 51: ......
Страница 52: ......
Страница 53: ......
Страница 54: ......
Страница 55: ......
Страница 56: ......
Страница 57: ......
Страница 58: ......
Страница 59: ......
Страница 60: ......
Страница 61: ......
Страница 62: ......
Страница 63: ......
Страница 64: ......
Страница 65: ......
Страница 66: ......
Страница 67: ......
Страница 68: ......
Страница 69: ......