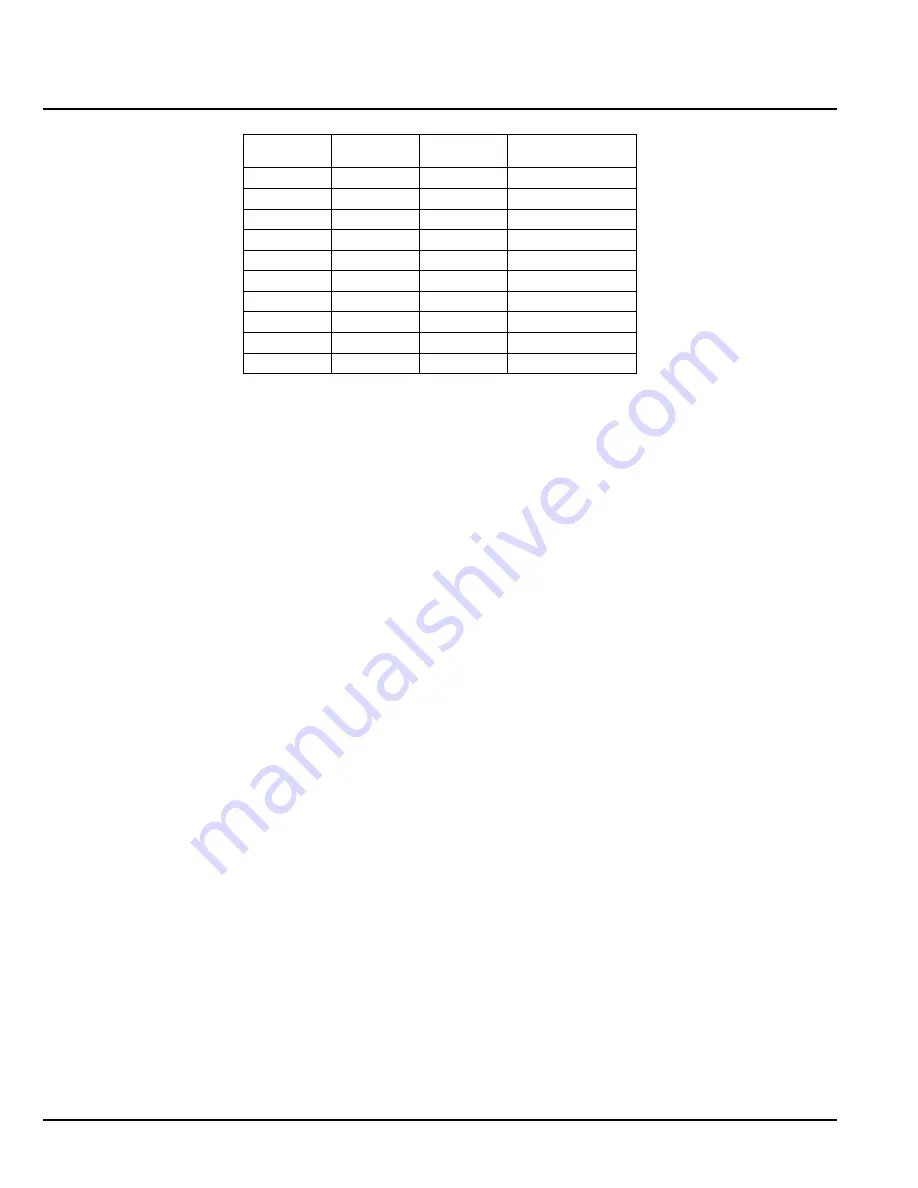
2-4
MN605
Table 2-5 Minimum Blower CFM for DPBV Motors (Drip Proof Blower Ventilated)
Blower Size
Motor Frame
Size
Blower CFM
Blower Static Pressure
(In H
2
O)
LM2
180
55
0.50
LM3
180
150
1.45
LM3
210
175
1.45
LM3
250
215
0.78
LM4
280
350
0.88
LM6
320
780
2.80
LM6
360
780
2.80
LM6
400
820
2.50
LM8
504-506
1120
1.58
LM9
508-5012
2000
5.00
Each motor nameplate is stamped with the above data for DPBV (less Blower), DPSV and TEPV enclosures.
Caution:
Motors designed for forced ventilation must have cooling air when fields are excited at rated voltage.
Installations having the air supply interrupted when the motor is not operating must have field
disconnected or field voltage reduced to 67% rated by means of field economizing resistor and relay or
motor insulation life will be significantly reduced.
Initial Start-Up
If driven equipment can be damaged by rotating in the wrong direction, uncouple the motor from the load before
checking for rotation.
Caution:
Series wound motors must never be allowed to run with no load (broken belt etc.) An unloaded motor may
reach destructive high speeds.
If the direction of rotation needs to be corrected, disconnect the input power supply and interchange the
appropriate leads. Refer to the motor connection diagrams in Section 4 of this manual.
1. The first start-up and running of the motor should be with the motor uncoupled from the load.
2. Check the direction of rotation by momentarily applying power to the motor.
3. With the motor running, make sure it’s running smoothly without too much noise or vibration. If either are
present, shut down the motor immediately and find the cause of the problem.
Coupled Start-Up
1. After the first successful no load start-up, stop the motor and assemble the coupling.
2. Align the coupling and be sure it is not binding in any way.
3. The first coupled start-up should be without load. Check to see that the driven equipment is not transmitting
any vibration back to the motor through the coupling or the base. Vibrations (if any) should be within
acceptable levels.
4. Run about 1 hour with driven equipment unloaded.
5. After completing these steps, the motor can now be loaded.
6. Do not exceed the value of armature nameplate amperes under steady continuous loads.
Содержание MN605
Страница 23: ......