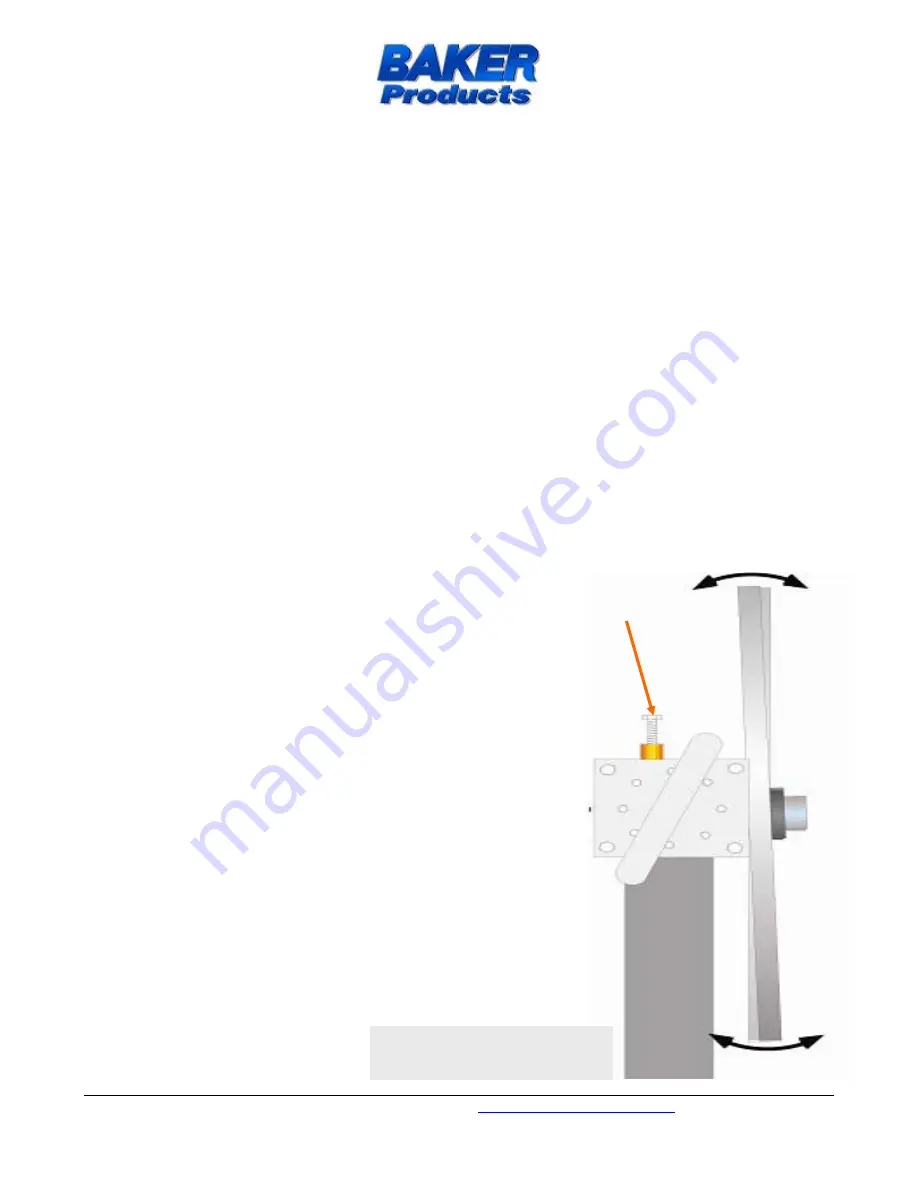
Baker Band Resaw - Rev 1, 09/08;
WWW.BAKER-ONLINE.COM
15
Drive Wheel Adjustments
The drive wheel’s position is set in the factory. In most cases it never needs to be moved. It
can only be moved in and out, and should only be moved when the wheel is cocked so that
the face cannot be lined up with the face of the idler wheel. If you find that you must move
this wheel, you will find a set screw located under the rubber dust cap, on top of the square
tube, on the back side of the head rig, directly behind the wheel. With this setscrew
loosened, the wheel can be moved in or out, or removed completely. If spindle and wheel
assembly is moved, the spindle will need to be re-dimpled. Retighten setscrew when
finished.
Note
:
It is important to re-dimple the spindle after moving or replacing it.
Idler Wheel Adjustments
When looking at the front of the head rig, the idler wheel is on the left. This wheel is used to
adjust tracking problems. Your tracking adjusters are located on the square tube on the
backside of the head rig. These two bolts make all of your tracking adjustments. The bolt on
the topside of the square tube is used for vertical adjustments. The bolt on the backside of
the square tube underneath the motor is used for horizontal adjustments. Use these bolts to
tilt the idler wheel so that it is lined up with the face of the drive wheel. When the faces
appear to be lined up, fine-tune it using the following procedure.
Vertical Adjustments
Rotate the wheel several rotations counterclockwise.
Examine the positions of the back of the blade on the
wheel at the top of the wheel and compare it to its
position at the bottom of the wheel. The blade position
should be the same in both locations on both wheels. If
not, proceed to the next step.
If the blade needs to come forward at the top of the
wheel, turn the vertical adjuster bolt clockwise. If the
blade needs to go back at the top of the wheel, loosen
lock nut then turn the vertical adjuster bolt
counterclockwise.
Manually turn the wheel several rotations and check the
tracking as noted in the first step above. If vertical
tracking is still not correct, repeat the procedure until the
blade position at the top and bottom of the wheel is the
same (both idler and pull wheels).
Rotate the wheel several rotations clockwise and repeat
the procedure, then tighten lock nut.
Note:
When blade is tracking properly, the blade gullet
should be flush with the front side of the wheels.
Vertical
Adjuster
Bolt
Figure C
: Vertical View
with Covering Removed