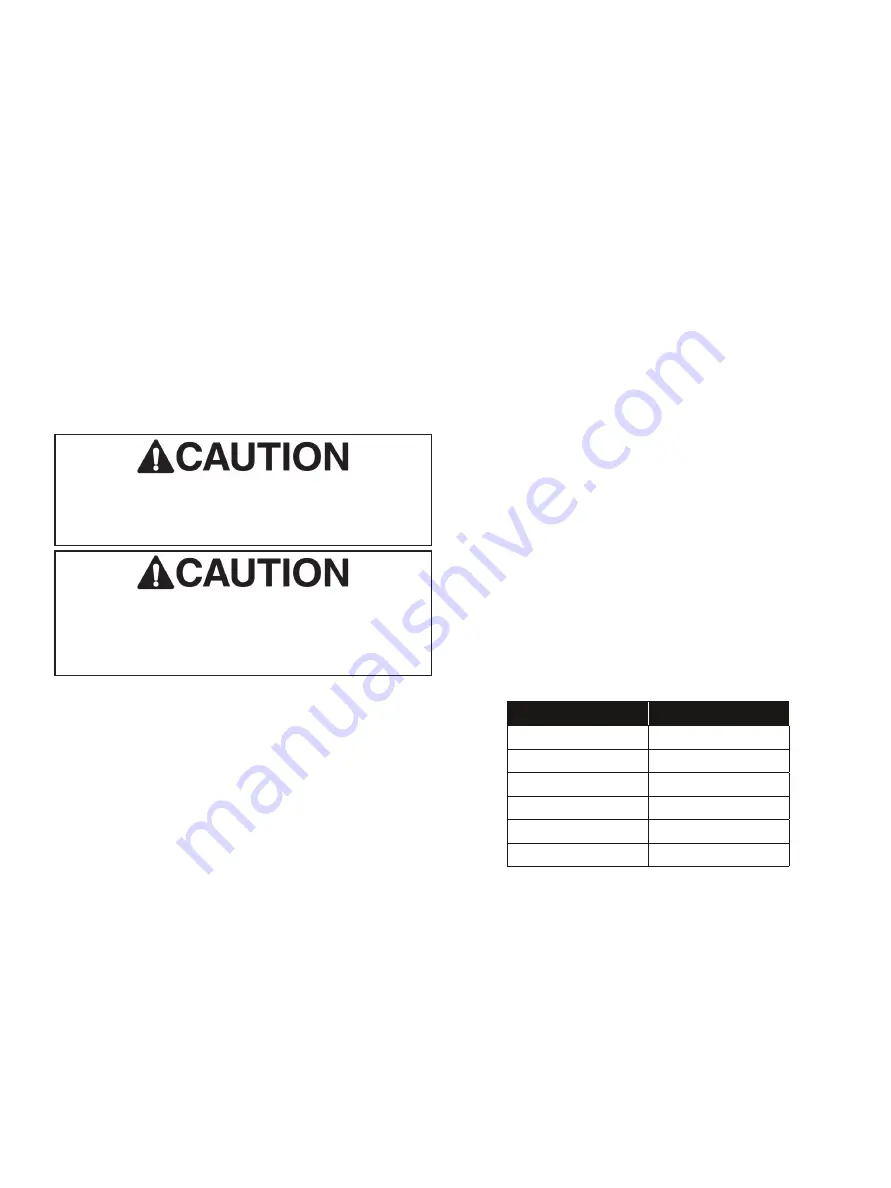
Masoneilan DSH Series Desuperheater Instruction Manual | 4
Copyright 2020 Baker Hughes Company. All rights reserved.
Isolation Bypass Valve
To allow for in-line inspection, maintenance and removal of the
desuperheater without service interruption, provide a manually
operated shutoff valve on each side of the desuperheater and a
manually operated throttling valve in the bypass line. The location
of the downstream isolation valves requires special consideration
in the case of the DSH Series Desuperheater as a result of the
spray water injection system on the outlet of the Desuperheater
valve. If the downstream isolation valve is close coupled to the
Desuperheater, it will be difficult to properly control downstream
temperature as the water injection becomes interrupted by the
location of the isolation valve. Please contact the factory for
specific recommendations on a suitable downstream location of
the isolation valve.
Flow Direction
The desuperheater must be installed so that the process fluid will
flow through the desuperheater in the direction indicated by the
flow arrow located on the body.
Welded Connections
Carefully follow the installation steps defined in the
sections noted below prior to performing weld proce-
dures.
Carefully review the information in this section prior
to welding any desuperheaters inline. Refer any
additional questions to the local Baker Hughes Sales
Office or Service Center.
Welding Process
Perform welding process in accordance with the standard
requirements for the materials and weld construction of the
specific desuperheater. Apply post weld heat treatment if
required.
Post Weld Cleaning and Assembly
Inspect the body and components for cleanliness and surface
condition. Remove any foreign materials, such as weld chips,
slag or scale. Make sure there are no nicks, scratches, burrs or
sharp corners on any sealing surfaces. Clean all gasket interface
surfaces and reassemble using new gaskets to ensure sealing
integrity.
Nozzles
Opening Nozzle Housing
Note: If the Desuperheater is shipped with the spray water
nozzles installed, it is advisable to remove these critical
devices during operations such as pipeline flushing and
hydrostatic testing. Blank (blind) nozzles may be employed
to separate hydrostatic test regions and protect important
surfaces.
The valve nozzle housings must always be reassembled with a
new set of gaskets.
Before disassembling, make sure the appropriate gaskets are
available for replacement.
Remove the nozzle flange nuts from the nozzle housing (Figure
1).
Lift the nozzle housing flange from the nozzle housing.
Remove the nozzle flange gasket.
The nozzle holder may have a snug fit within the nozzle housing.
For ease of removal of the nozzle holder, screw a bolt (per Table
1) into the exposed threaded connection to provide a lifting point.
Pull nozzle holder to remove from nozzle housing.
Remove nozzle gasket from the bottom of the nozzle housing.
If installing an alternative nozzle, complete the following
additional steps:
Install a new inner nozzle gasket in the gasket groove at the
bottom of the nozzle housing.
Install the nozzle into the housing.
Install a new outer nozzle gasket in the gasket groove.
Mount the nozzle flanges and nuts to the housings.
Torque the nuts to the values indicated on the assembly drawing
and to the required torquing sequence shown in Figure 1 in at
least 6 equal torque steps (10%, 20%, 40%, 60%, 80%, and
100% of the prescribed value) unless otherwise specified.
Nozzle C
v
Lifting Bolt Size
0.4
1/4”
0.8
3/8”
1.5
1/2”
3.0
3/4”
5.0
1”
10.0
1-1/2”
Table 1 - Nozzle removal bolts