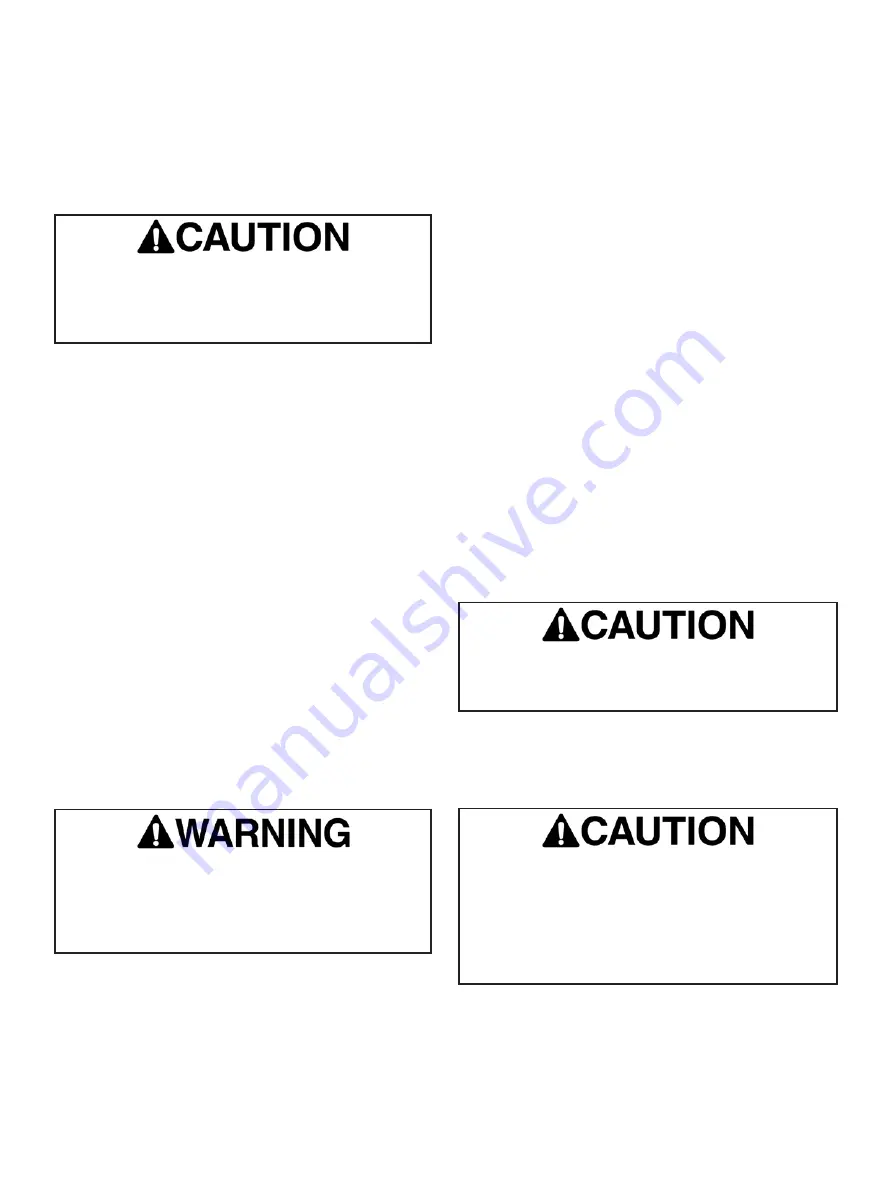
Masoneilan 77000 Series Control Valves Instruction Manual | 3
Copyright 2021 Baker Hughes Company. All rights reserved.
Unpacking
Care must be exercised when unpacking the valve to prevent
damage to the accessories and component parts. Contact the
local Baker Hughes Sales Office or Service Center with any
issues or problems. Be sure to note the valve model number and
serial number in all correspondence.
Installation
The 77000 Series valve must always be installed with
the flow tending to open the valve plug. For applica
-
tions where insulation of the valve body is required,
do not insulate the valve bonnet when possible.
Recommended Installation
It is recommended to install the 77000 Series valves in the
vertical position with the actuator extended up whenever
possible. This orientation eliminates the need for additional
pipe support, reduces the side load friction on the actuator, and
provides ease of removal of the trim during maintenance for
weld-end construction designs.
For best acoustical performance provide a minimum of 10 pipe
diameters of straight pipe length at the exit of the valve before
installation of any pipe bends or additional equipment.
For applications involving flashing or erosive service it is highly
recommended to include a minimum of 20 pipe diameters for
best system performance.
Handling
When lifting the valve for installation it is important to never lift
the valve by the actuator, lever or other assembled components.
It is recommended to use lifting straps around the body or flange
connection whenever picking the valve for installation or removal
from the piping system.
Piping Cleanliness
Before installing the valve in the line, clean piping and valve of all
foreign material such as welding chips, scale, oil, grease or dirt.
Gasket mating surfaces must be thoroughly cleaned
to ensure leak-free joints. Sacrificial start-up fixtures
can be purchased from Baker Hughes to protect the
operational trim during the installation and line flush
-
ing phases.
If major system or piping modifications (or repairs) are performed,
thorough flushing and blowdown of the system will be required
prior to reinstalling the 77000 Series trim. Sacrificial flushing
trim should be installed in this valve to protect the integrity of
the flow passages. Failure to follow this warning will violate the
valve warranty agreement and could result in control instability,
excessive noise levels, and valve leakage.
Isolation Bypass Valve
To allow for in-line inspection, maintenance and removal of the
valve without service interruption, provide a manually operated
shutoff valve on each side of the control valve and a manually
operated throttling valve in the bypass line.
Heat Insulation
In case of a heat-insulated installation, do not insulate the valve
bonnet and take protective measures relative to personal safety.
Hydrostatic Testing and Line
Cleaning
During this operation, the control valve must not be used as an
isolating valve. This means that the valve must always be opened
before carrying out pressure tests in the process line, cleaning of
pipes, etc. Otherwise equipment damage or failure of the seal
rings could result. Flushing and hydrostatic test equipment can
be purchased from the Masoneilan factory.
Flow Direction
The valve must be installed so that the process fluid will flow
through the valve in the direction indicated by the flow arrow
located on the body.
Welded Connections
Carefully review the information in this section prior to welding
any valves inline. Refer any additional questions to the local
Baker Hughes Sales Office or Service Center.
Pre-Weld Preparation
Carefully follow the installation steps defined in the
sections noted above prior to performing weld proce-
dures.
Welding Process
Perform welding process in accordance with the standard
requirements for the materials and weld construction of the
specific valve. Apply post weld heat treatment if required.
Internal valve components should be removed prior
to performing any post weld heat treatment in order to
prevent damaging any soft goods. If unable to remove
the elastomeric components, then other methods
must be employed to prevent the local temperature
around the seals from exceeding the maximum mate
-
rial limits.