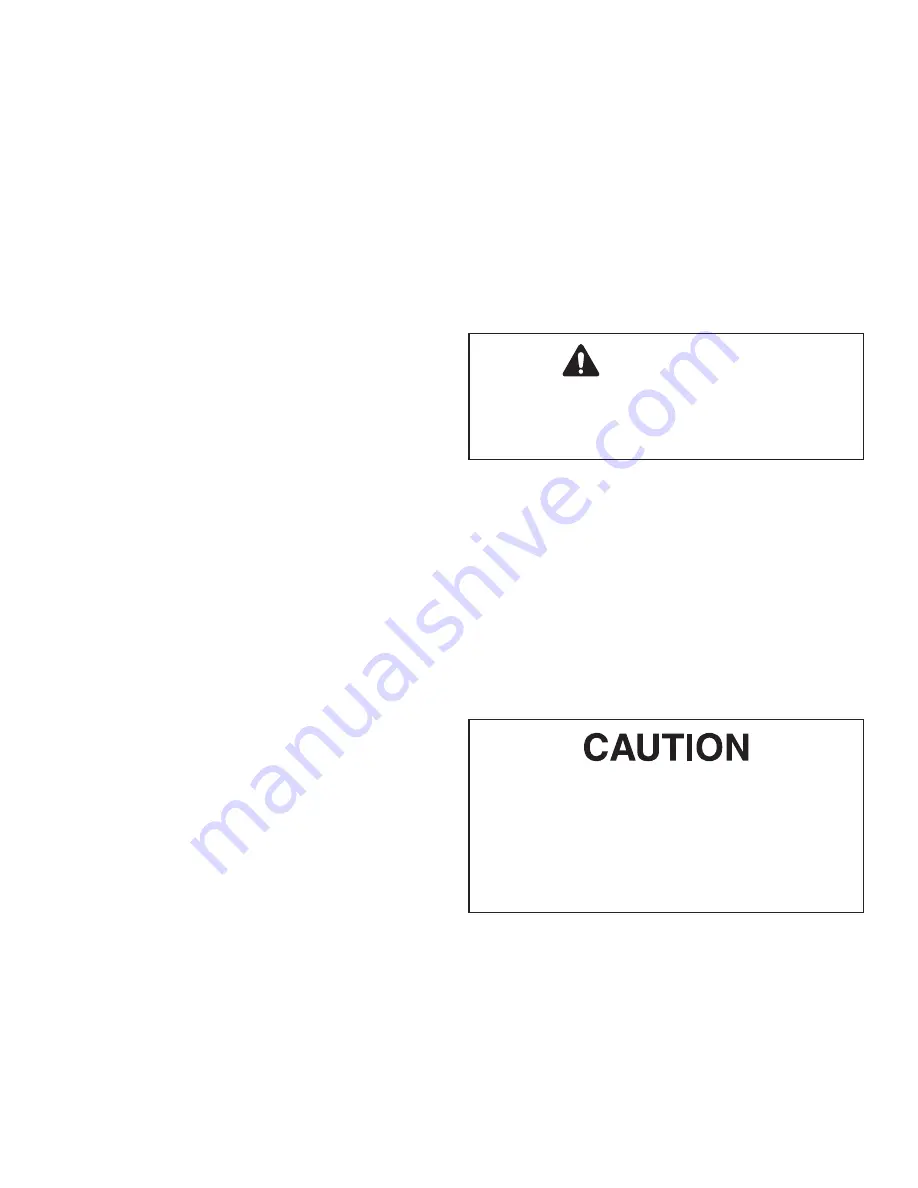
© 2021 Baker Hughes Company. All rights reserved.
4 | Baker Hughes
Description-Operation
535V Regulators
The 535V Direct Operated Regulators are designed to
maintain a uniform reduced pressure. Microflow bodies of
regulators are offered in single seat type.
Operation
The adjustable spring is set for the desired controlled
pressure. This spring holds the plug open. An increase in
controlled pressure above the set point causes regulators to
close.
Variations in the controlled pressure thus cause the necessary
regulators movement to restore the controlled pressure to set
point.
535V-50 Regulators
Masoneilan 535V-50 Series Differential Pressure Regulators
are designed for maintaining one pressure in excess of
another (reference) pressure by an adjustable amount.
Microflow bodies of regulators are offered in single seat type.
Operation
The adjustable spring of actuator is set for the desired
differential pressure. This spring holds the regulator open. An
increase in differential above the set point causes the 535V-50
regulators to close.
Variations in the differential pressure thus cause the necessary
regulator movement to restore the controlled pressure to set
point.
Plug and seat ring combination (trim)
Eight plugs and five seat rings can be used in combination to
obtain ten different plug and seat ring assemblies (See Figure 2).
Each plug design and the seat ring orifice diameter permit to
identify parts in relation to Figure 2.
The four plugs corresponding to trim Nos 6 to 9 differ by the
angle of the flat, machined on the point. The same seat ring
(3e) and the same spacer (3f) are used in the four cases.
See Figure 2 to select the plug and seat ring combination to
obtain the required C
v
.
Installation
Before installing, blow out line thoroughly to remove all foreign
matter which might foul the regulator.
Place the regulator vertically in a horizontal run of pipe so that
the controlled fluid will flow through the body in the direction
indicated by the arrow on the body or the words “IN & OUT”
marked on the connections. On steam service, the regulator
should be installed with the diaphragm chamber down so that
the diaphragm will be protected by a water seal. If installed
otherwise, an adequate water seal or seals must be provided.
A three valve by-pass around the regulators permits removing
the regulator from the line without shutting off the flow.
See Figure 1 for typical installation diagrams.
On 535V Regulators
Pipe the controlled pressure from a convenient point in the line
6-10 feet (1,8 to 3 m) from the regulator (or in the discharge
line, 6-10 feet from the pump on pump pressure applications),
to the 1/2” NPT connection in the diaphragm case.
Install a gauge and a needle valve in the controlled pressure
line, to protect diaphragm case against any over- pressure.
Needle valve permits shutting off the control line and also
serves as an adjustable choke to prevent cycling of the
regulator, which may result from the pulsation of a pump in the
system.
On 535V-50 Regulators
Pipe the
higher
pressure fluid from a convenient point to the
1/2” NPT connection in the upper diaphragm case (i.e., to
diaphragm chamber where pressure will oppose the spring).
Pipe the lower pressure fluid to the diaphragm chamber.
Install a needle valve and gauge in each of these control lines,
sufficiently near each other so that both valves can be reached
simultaneously.
Needle valves permit shutting off both control lines and may
be used as adjustable chokes to prevent cycling of the
regulator as a result of pump pulsations. By adjusting both
valves simultaneously, accidental over-pressuring either side
of the diaphragm can be avoided.
Pressure must be increased on both sides of
the diaphragm at the same time in order to avoid
diaphragm failure.
CAUTION
CAUTION
WARNING
DANGER
Tests have been performed at the factory to check
correct operation of the regulator on its full nominal
spring range. After that, the spring compression has
been fully removed to avoid unnecessary stress of
parts (diaphragm, spring) during storage.
THEREFORE IT IS NECESSARY TO PROCEED WITH
ADJUSTMENT BEFORE SERVICING.