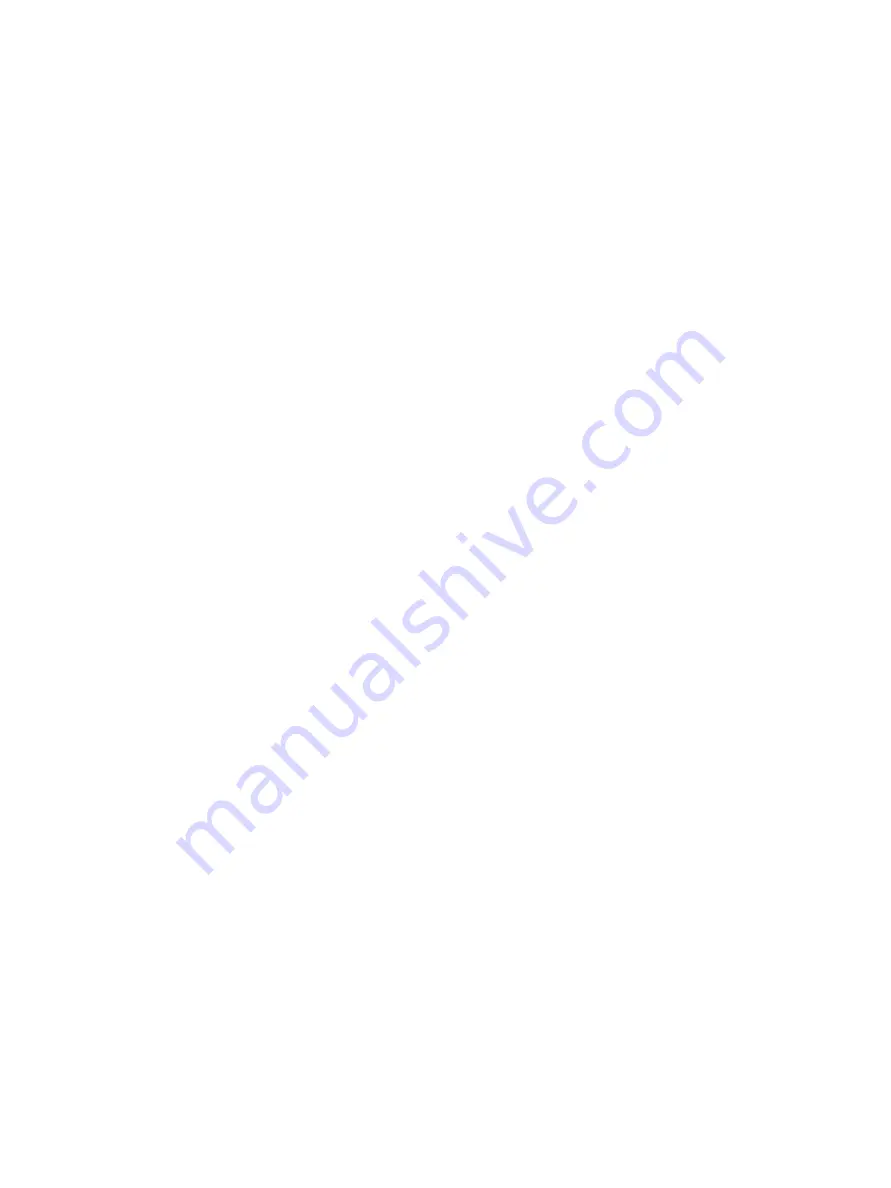
30 |
Baker Hughes
© 2020 Baker Hughes Company. All rights reserved.
L. Bonnet Bottom (8)
The bottom bonnet should be replaced if:
1. Threads are stripped, torn or galled
2. The guide seating surface is scratched, nicked,
corroded or leaks
3. The backup plate seating surface is scratched,
nicked or corroded.
4. Condition is porous, corroded or distorted
M. Backup Plate (39)
The backup plate should be replaced if:
1. Inside circumference “X” is scratched, nicked,
pitted or galled
2. O-ring groove “W” is scratched, nicked, pitted or galled
3. Backup plate is distorted
N. Spindle O-Ring
(310XX011) (38)
The spindle O-ring should always be replaced. The material
and durometer of the spindle O-ring should be the same
material and durometer as that specified for the Seat O-ring
(37).
O. Backup Plate O-Ring
(310XX030) (40)
The backup plate O-ring should always be replaced. The
material and durometer of the backup plate O-ring should
be the same material and durometer as that specified for the
seat O-ring (37).
P. Seat O-Ring (310XX013) (37)
The seat O-ring should always be replaced. The material and
durometer of the seat O-ring should be the same material
and durometer as that specified on the O-ring nameplate.
XIV. Inspection and Part Replacement (Contd.)
A. Metal Seat Valves (MS)
(Figures 1 and 2)
1. Bearing surfaces should be ground together using
a 320 grit lapping compound (see Table 17). These
surfaces are:
a. The disc holder-spindle pocket and spindle spherical
nose radius,
b. The lower spring washer and spindle spring washer
radius and
c. The upper spring washer and adjusting screw
spherical radius. Clean all parts before assembly.
2. Apply small amount of non-copper based thread
lubricant to the guide-bonnet seating surface and the
bonnet and base threads.
3. Use a clean base (1) lapped for the valve set pressure
(see seat width requirement Table 5). Place a lapped
disc (2) on the base with lapped surfaces facing each
other. Place the disc holder (4) onto the disc and base.
Place guide (5) over disc holder onto base. Lubricate
the disc holder-spindle bearing surface with non-copper
based thread lubricant
4. Lubricate the spindle nose with a small amount of non-
copper based thread lubricant and insert the spindle (9)
into the disc holder spindle pocket.
5. Apply a small amount of non-copper based thread
lubricant on the bearing surface of the lower spring
washer (10) and slip it over the spindle (9). Install the
spring (11) and upper spring washer.
6. Apply a small amount of non-copper based thread
lubricant to the bonnet-base threads and guide seating
surface. When a stainless steel bonnet (6) and base
(1) are used, and/or a standard bonnet for service
above 500° temperature, apply non-copper based
thread lubricant to the bonnet-base threads and guide
(5) seating surface. Before tightening the bonnet
completely, adjust the position of the guide so that one
of the holes is lined up with the discharge of the valve.
Tighten the bonnet using sufficient torque from Base
Torque Specification (see Table 10).
7. Thread the adjusting screw locknut (13) on the adjusting
screw (12). Apply a light coat of non-copper based
thread lubricant to the adjusting screw threads and
spherical radius. Thread the adjusting screw locknut
(13) onto the adjusting screw (12). Apply a small
amount of non-copper based thread lubricant to the
tip of the adjusting screw. Install the adjusting screw
in the bonnet, rotating the number of times required
to compress the spring slightly. Use pliers to hold the
spindle (9) in position and prevent galling. Adjust the
XV. Reassembly of Consolidated 19000 Series SRV
Содержание Consolidated 19000 DA
Страница 2: ......