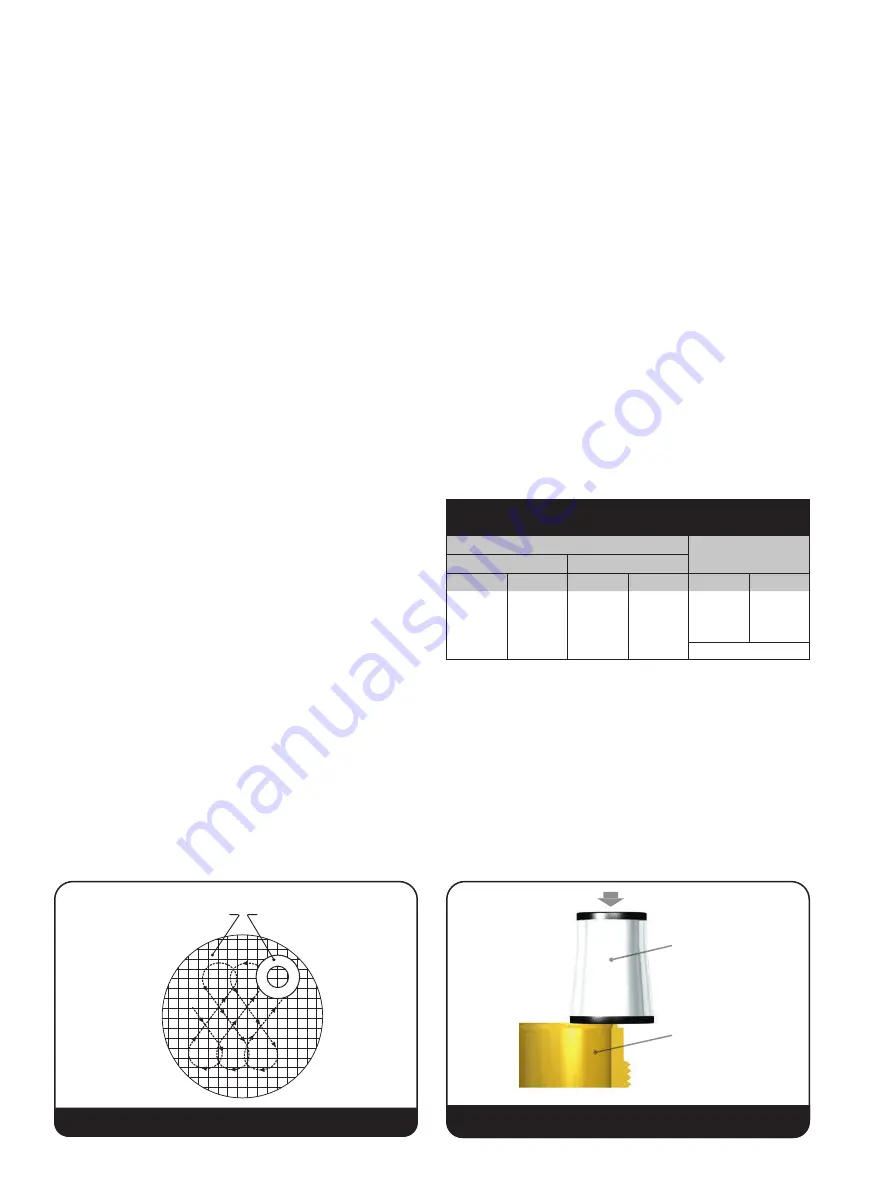
20 |
Baker Hughes
© 2020 Baker Hughes Company. All rights reserved.
A. Metal Seat Valves (MS)
A1. Precautions and Hints for Lapping Seats
Reconditioning of the seat surface may be accomplished
by lapping with a flat cast iron ring lap coated with a 1000
grit lapping compound or its equivalent (see Table 17). A
cast iron lap, coated with a lapping compound, is used for
reconditioning the seating surfaces of the base (1) and disc
(2). The following will enable maintenance personnel to do a
“professional” job of lapping seats:
1. Keep work materials clean.
2. Always use a fresh lap. If signs of wearing (out
of flatness) are evident, recondition the lap.
Reconditioning of laps is accomplished by lapping them
on a flat lapping plate. The lapping should be done with
a figure-eight motion as indicated in Figure 9. To assure
the best results when lapping seats, the laps should be
reconditioned after each usage.
3. Apply a very thin layer of compound to the lap. This will
prevent rounding off the edges of the seat.
4. Keep the lap squarely on the flat surface and avoid any
tendency to rock the lap which causes rounding of the
seat.
5. When lapping, keep a firm grip on the part to prevent
the possibility of dropping it and damaging the seat.
6. Lap, using an eccentric, or figure-eight motion, in all
directions, while at the same time, applying uniform
pressure and rotating the lap slowly (see Figure 9).
7. Replace the compound frequently after wiping off the
old compound, and apply more pressure to speed the
cutting action of the compound.
8. To check the seating surfaces, remove all compounds
from both the seat and the lap. Then, shine the seat
with the same lap using the lapping motion described
above. Low sections on the seating surface will show up
as a shadow in contrast to the shiny portion. If shadows
are present, further lapping is necessary and only
laps known to be flat should now be used. Only a few
minutes will be required to remove the shadows.
9. When the lapping is completed, any lines appearing
as cross scratches can be removed by rotating the lap
(which has been wiped clean of compounds) on the
seat about its own axis.
10. The seat should now be thoroughly cleaned using a lint-
free cloth and a cleansing fluid.
A2. Lapping the Base Seat
For -1 Material Seat Design
The base seat may be reconditioned using the lapping
procedure; however, the dimensions provided in Table 2,
should be used to determine the seat width.
The seat width can be measured by the use of a “Measuring
Magnifier” (see Figure 10a). Baker Hughes recommends the
use of Model S1-34-35-37 (Bausch and Lomb Optical Co.)
or an equivalent. This is a seven power glass with a .750"
(19.05 mm) scale showing graduations of .005" (0.13 mm).
The use of this scale in measuring the seat width is shown in
Figure 10b.
LAPPING PLATE
RING LAP
Figure 9: Lapping Pattern
Measuring
Magnifier
Base
Figure10a:MeasuringMagnifier
XIII. Maintenance
Table 2: Base Lapping Width
(-1 Metal Seat Design Only)
SET PRESSURE
SEAT WIDTH
psig
barg
min.
max.
min.
max.
in.
mm
5
100
0.34
6.89
.010
0.25
101
300
6.96
20.68
.015
0.38
301
800
20.75
55.16
.020
0.51
801
UP
55.23
UP
Note 1
1. Add .005” (0.127 mm) per 100 psig (6.896 barg), not to
exceed .070” (1.78 mm).
Содержание Consolidated 19000 DA
Страница 2: ......