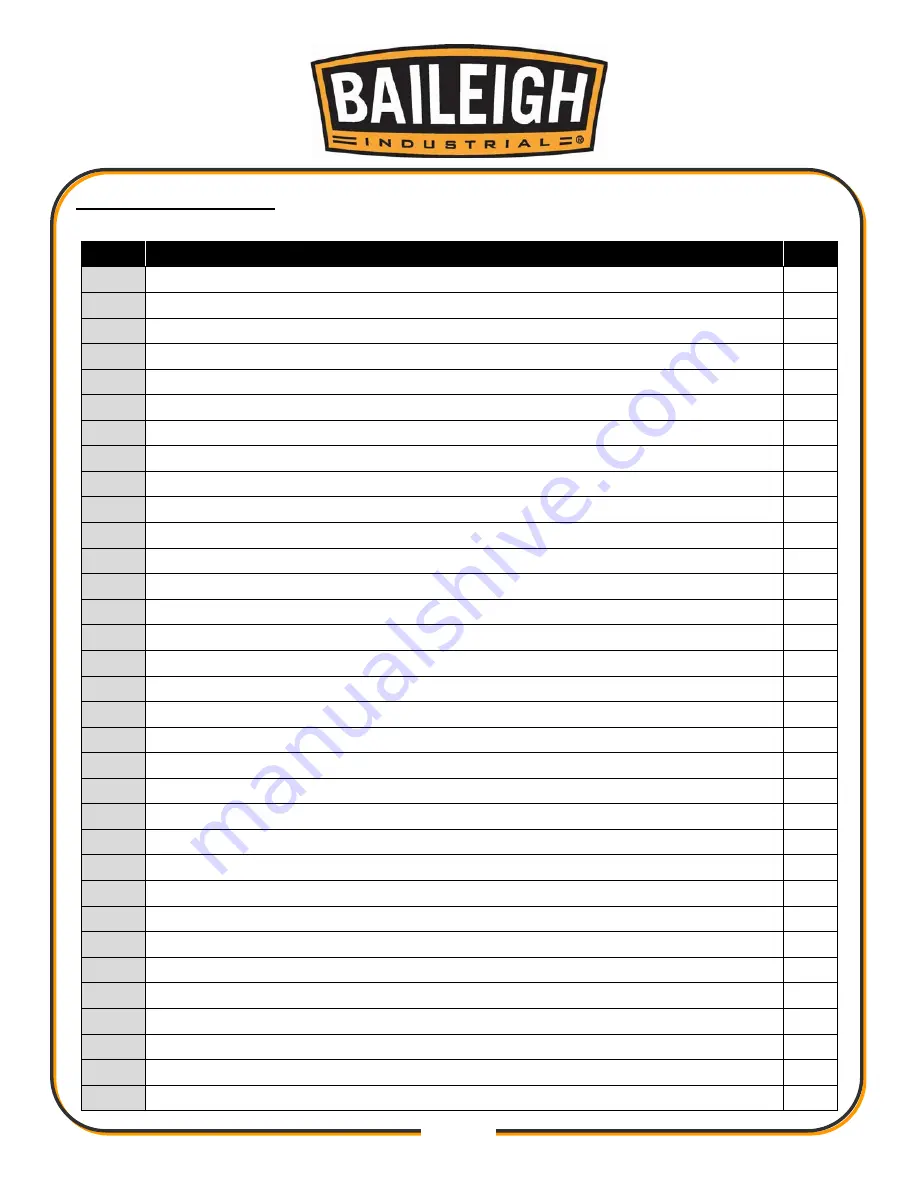
39
39
Parts Identification List
Item
Description
Qty.
1
Angle Bar
1
2
Bending Leaf
1
3
Clamping Bar
1
4
Insert Bar
1
5
Machine Base Assembly
1
6
Bottom Die
1
7
Fingers 1@6” (152.4mm), 5@5” (127mm), 2@4” 101.6mm, 3@3” (76.2mm)
1
8
Clamping Beam
1
9
Back Gauge Assembly
1
10
Hydraulic Oil Tank
1
11
Hydraulic Cylinder Pin
4
12LH
Hydraulic Cylinder
1
12RH Hydraulic Cylinder
1
13
Clamping Cam Assembly
2
14
Cam
2
15
Workpiece Thickness Adjusting Nut
2
16
Clamping Beam Center Fixing Rod
2
17
Adjusting Screw
2
18
Adjusting Screw
2
19
Nut
4
20
Clamping Beam Center Fixing Plate
4
21
Clamping Beam Center Fixing Rod
2
22
Clamping Beam Center Fixing Plates Connector
2
23
Clamping Beam Adjustment Screw
2
24
Clamping Beam Adjusting Handwheel
2
25
Clamping Beam Center Shaft
2
26
Hinge Pin - Left Side
1
27
Hinge – Left Side
1
28
Hinge Pin – Right Side
1
29
Hinge - Right
1
30
Collar
1
31
Hex Bolt
4
32
Link Shaft
1
Содержание BB-12010H
Страница 17: ...14 14 OVERALL DIMENSIONS 139 00 145 50 60 00 135 50 122 50 37 50 50 50 34 50...
Страница 18: ...15 15 GETTING TO KNOW YOUR MACHINE G H A D B L I J E C K F...
Страница 19: ...16 16 S N R M T Q P U O...
Страница 51: ...48 48 NOTES...