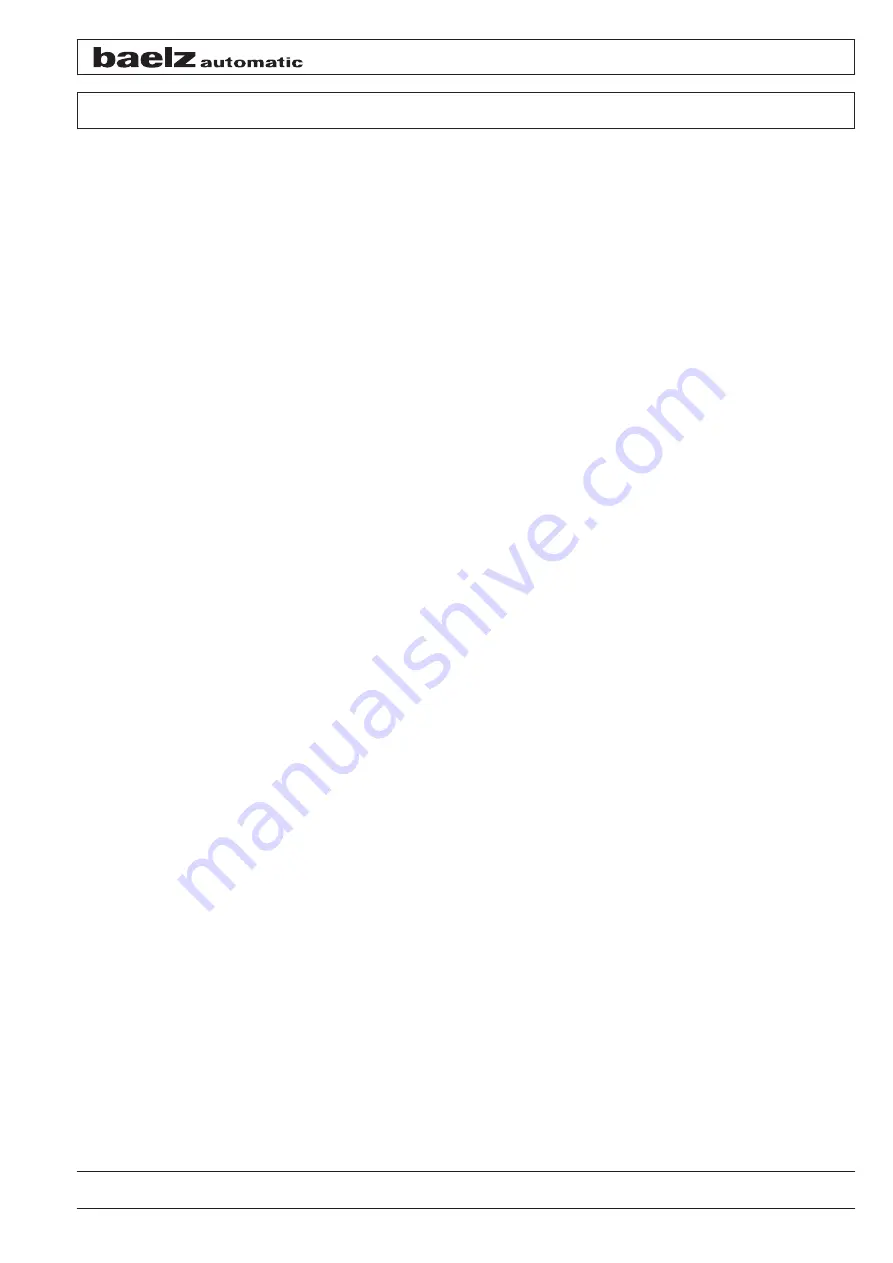
Page 23/37
Operating Instructions
BA 373-E66
Technical specifications subject to change
W. Bälz & Sohn GmbH & Co.
Koepffstrasse 5
74076 Heilbronn
Germany
Phone +49 (0)7131 15 00 0
Fax +49 (0)7131 15 00 21
www.baelz.de
Observe copyright protection DIN 34
7.5 Calibrating the positioning electronics to the travel
The positioning electronics are adjusted by the manufacturer for the specified travel. Therefore only minor calibra-
tion should be required. The following requirements must be fulfilled before proceeding:
● The actuator is properly mounted on the valve
● The switching and signalling unit is properly adjusted to the valve stroke
● The potentiometer's zero point corresponds to the stroke's lower end position
● The limit switches have been adjusted to the valve stroke
The positioning electronics can be adjusted so that the actuator is switched off either by the switches (DE, WE) or
the positioning electronics when it reaches the end positions.
If the actuator is switched off by the switches, adjust the potentiometers on the positioning electronics so that the
LEDs just remain illuminated when the end position is reached.
7.5.1 Setting the zero
At the input, set the lower set point (0 or 4 mA, 0V) for the lower end position.
Turn potentiometer P1 counter-clockwise until the actuator is switched off by the associated switch and LED V19
just remains illuminated. This can be checked by turning the potentiometer back.
7.5.2 Setting the end position
For the upper end position, use potentiometer P2 in combination with LED V18 to preset the set point for the upper
end position.
Turn potentiometer P2 clockwise to shift the tripping point upward. When the actuator is to be switched off by the
switches, change the potentiometer setting until the LED just remains illuminated.
If the potentiometer's angle of rotation cannot be fully used due to a very small travel, use the spreading function to
adapt the input range. This function is activated by setting switch S1.2 to OFF.
Turn potentiometer P4 counter-clockwise to shift the upper tripping point downward.
7.6 Setting the dead band
The set dead band of the actuator depends on the actuator. This parameter is factory-set and should not be
changed. If the dead band setting is too narrow, the actuator will oscillate around the set point, which will cause
premature wear of positioner and actuator. If oscillations are detected, these can be reduced by increasing the
dead band. Make sure the setting is retained when replacing the positioning electronics.
7.7 Reversing the actuator action
If the actuator action is to be reversed as compared to the set point, this can be done by changing the setting of
switch S3. It may be necessary to adapt the end positions or travel.