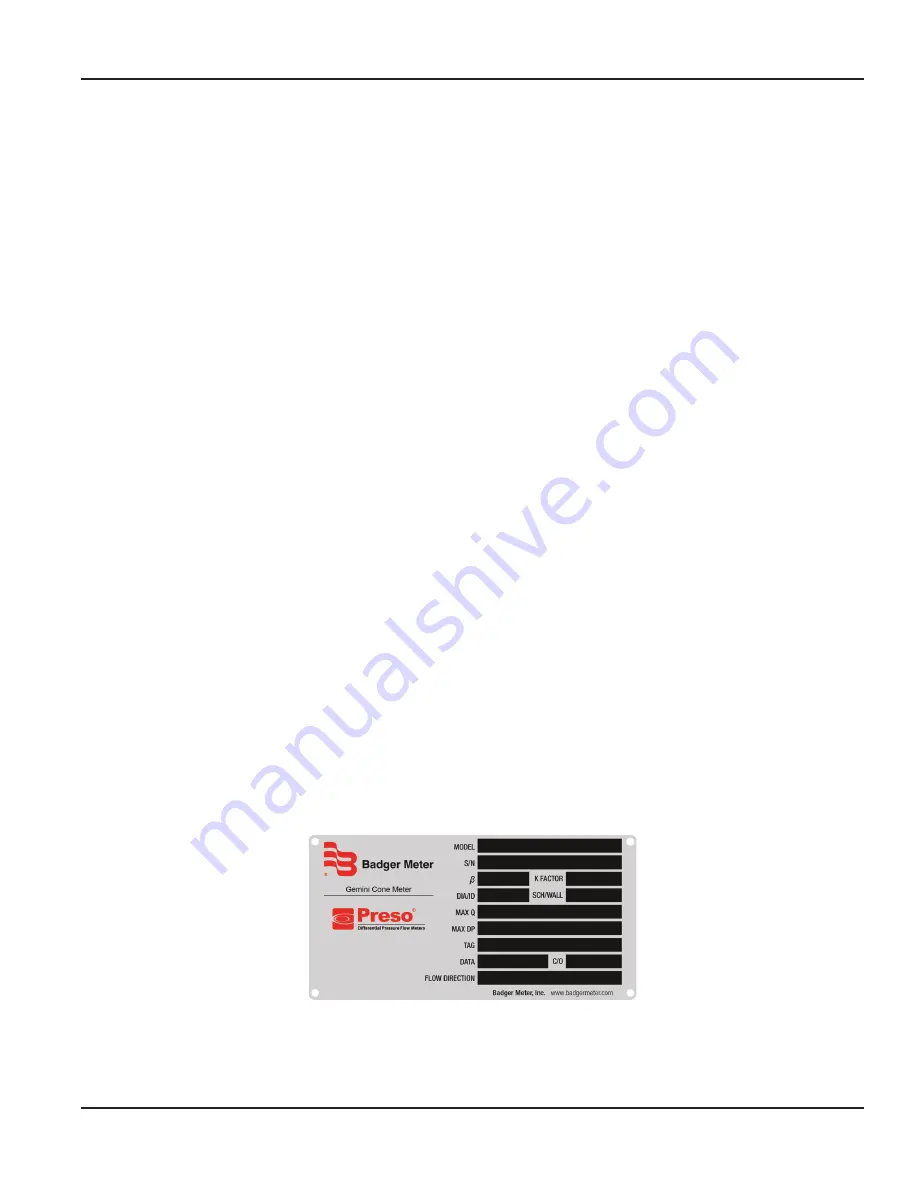
Meter Components
The meter comprises three primary elements, as shown in
• A meter body or tube with various available end connections
• A cone assembly, either fabricated or machined from a solid piece of metal, positioned in the center of the meter tube
• A pair of pressure taps—a wall tap upstream and an integral sensing tap downstream—for reading the differential
pressure across the center of the meter tube (Alternately a downstream tap may be used under certain process
measurement conditions )
The meter can be manufactured from various materials (carbon and stainless steels are standard, but more exotic materials
such as duplex stainless steel or nickel-based alloys are also available upon request) to meet the specific requirements for
metering steam, air, natural gas, digester gas, nitrogen, ethanol, and a host of media from crude oil to industrial gases
Preso Gemini Cone meters are differential pressure flow devices providing highly accurate and repeatable measurements of
liquids, gases and steam The meter design provides longer lasting accuracy and lower permanent pressure loss than orifice
type meters, reducing maintenance and operating costs The Gemini Cone can be built to meet the highest pressure and
temperature specifications often limited in other flow meter technologies All models can also be supplied with RTD's and
transmitters to provide an economical mass flow measurement solution
System Components
Valve Manifolds
A 3-way or 5-way valve manifold isolates the transmitter from the process lines A manifold allows the operator to calibrate
the transmitter without removing it from the impulse tubing, draining the transmitter and impulse tubing or venting it to
atmosphere Valve manifolds must be oriented according to the manufacturer’s instructions to prevent trapping air or liquid
Shutoff Valves
Choose a blocking valve that is rated for the operating pressure of the pipe in which it will be installed Where dangerous or
corrosive fluids or gases like oxygen are likely, the blocking valve and packing must provide ample protection The valves
must not affect the transmission of the differential pressure signal
Install blocking valves next to the Gemini Cone meter pressure taps
Differential Pressure Transmitter
A differential pressure transmitter interprets the differential pressures generated by the cone within the meter body and
provides an analog or serial output to a flow computer or data control system Select a transmitter that is rated for accuracy
and safety for your particular operating conditions
Differential pressure devices must be zeroed following installation The procedure varies somewhat for liquid, gas, and steam
applications and by manufacturer See the manufacturer’s literature for complete procedures on zeroing the transmitter
Meter Nameplate
This name plate identifies the proper specifications associated with the meter designed for the defined application The
direction of the flow is also indicated on each tag
Figure 2: Nameplate
Introduction
Page 7
June 2018
DPM-UM-00206-EN-03