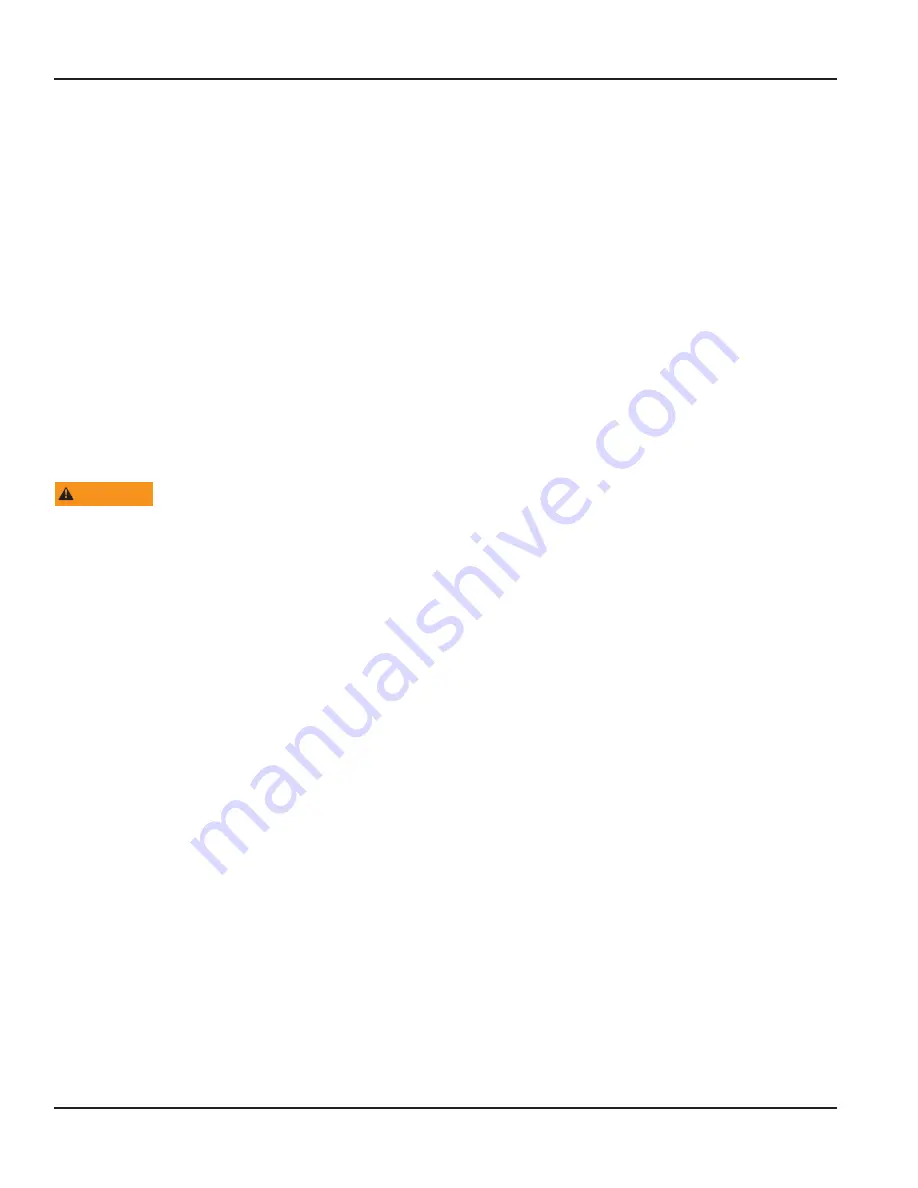
Test Procedures
Motor Test Loaded
1 Open the Hydraulic System Analyzer loading valve fully to read maximum pump flow at zero pressure
2 Select
Run
and/or
Record
on the PC (see
"Recording Measurements to a File" on page 10
)
3 Put one control valve in the forward operating position If there are multiple valves, only one control valve should be in an
operating position at any one time
4 Using a tachometer, run the motor while providing a load on the motor The flow and RPM can now be checked against
the motor manufacturer’s specifications A decrease in RPM in the manufacturer's specifications or the unloaded motor
test indicates a loss of the motor's efficiency
Motor Test Simulated Load
1 Reverse the pump flow
2 Open the Hydraulic System Analyzer loading valve fully to read maximum pump flow at zero pressure
3 Install one or both of the following instruments on the hydraulic motor
a Place a Hedland variable area meter on the case drain and manually record the flow as you increase the load on the
tester Then compare it to the manufacturer's specifications
b Place a tachometer on the motor's shaft
4 Select
Run
and/or
Record
on the PC (see
"Recording Measurements to a File" on page 10
)
5 Increase the load on the Hydraulic System Analyzer to produce back pressure on the hydraulic motor
WARNING
SEE MANUFACTURER'S SPECIFICATIONS FOR MAXIMUM ALLOWABLE BACK PRESSURE. IF THE MOTOR DOES NOT
HAVE AN EXTERNAL DRAIN, IT CANNOT HAVE A BACK PRESSURE LOAD. FAILURE TO FOLLOW THE MANUFACTURER'S
SPECIFICATIONS CAN RESULT IN INJURY TO PERSONNEL AND/OR DAMAGE TO THE EQUIPMENT.
6 The flow at rated RPM can now be checked against the motor manufacturer’s specifications A decrease in RPM and an
increase of case flow with increased load indicates a loss of the motor's efficiency
OTE:
N
If the motor does not have a case drain, it cannot be loaded on the discharge side
Other Test Procedures
Case Drain
You can check the case drain flow concurrently with any of these setups using a second Hedland Variable Area Flow Meter¹
However the motor’s case drain, the pump’s case drain, and the charge pump are all connected in series This means that the
charge pump flow must be factored into the case flow Any increase in case flow would indicate a pump or motor problem
Test Stand Calibration System
You can add the Hydraulic System Analyzer to any existing test stand for diagnostics calibration, certification and data logging
of hydraulic components You can use the Hydraulic System Analyzer for recording bi-directional flow, which makes it ideal for
hydraulic motors and cylinders Install the meter either on the supply or the return line of the test bench However, place the
meter on the supply side in case any contamination is passed through the units under test Once the data is recorded it can be
stored for future reference or printed and sent with the repaired unit
Servo Controlled Pumps, Motors and Valves
Special procedures for testing these components may be specified Observe the nstructions of the component and
machine manufacturer
These components may have the capability of nearly instantaneous increases of flow and/or pressure and should have a
positive means of control An example of such a control is the push-pull servo control for varying pump delivery Attempting
to manually adjust this control can result in excessive increases in flow and/or pressure Such uncontrolled changes may cause
a failure in the system and result in component damage or personal injury
¹ For complete information, visit www badgermeter com and select Petroleum Fluids under Products / Variable Area High
Pressure Flow Meters
Page 24
June 2022
TST-UM-02433-EN-02