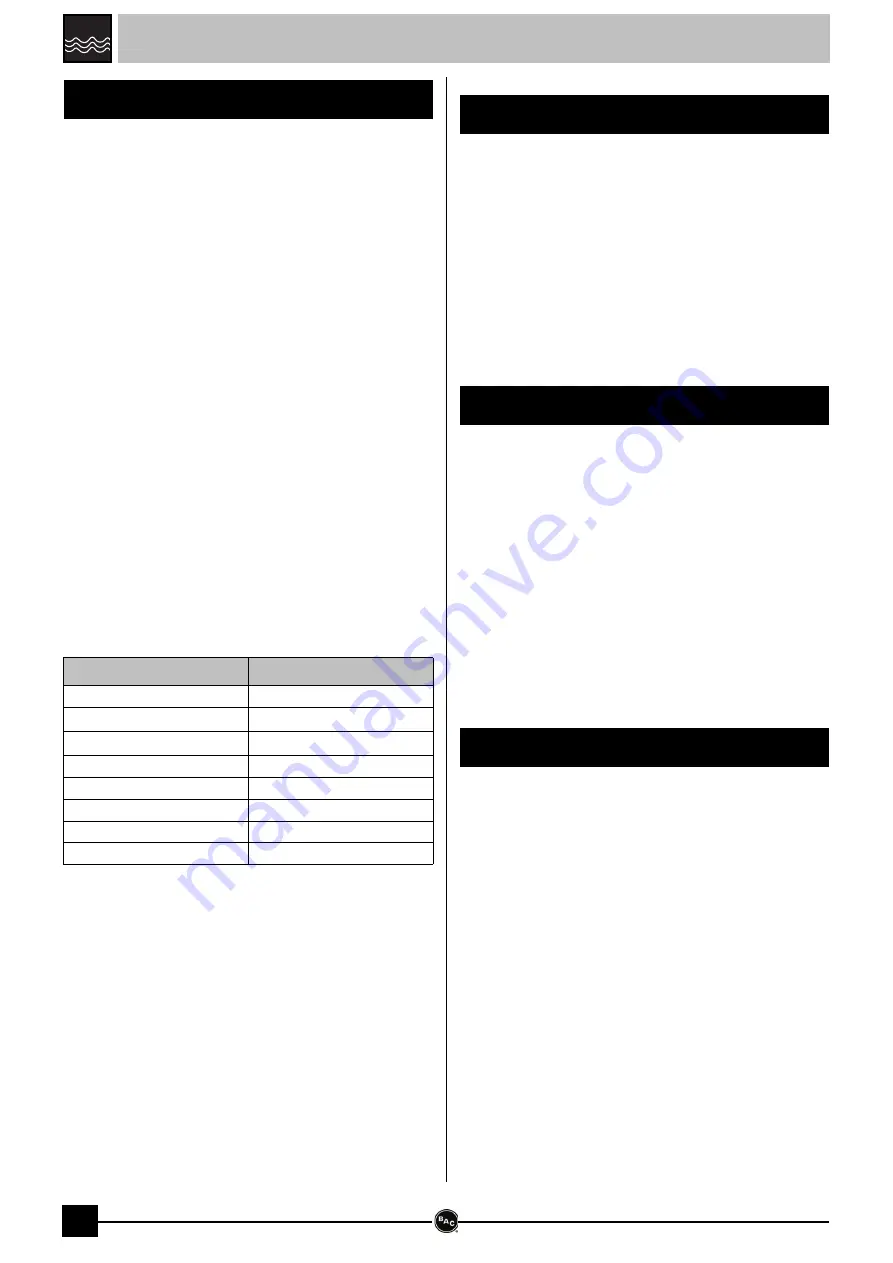
4
WATER CARE
In all cooling equipment, operating in evaporative mode, the cooling
is accomplished by evaporating a small portion of the re-circulating
water as it flows through the equipment. When this water
evaporates, the impurities originally present in the water remain.
Unless a small amount of water is drained from the system, known
as blow down, the concentration of dissolved solids will increase
rapidly and lead to scale formation or corrosion or both. Also, since
water is being lost from the system through evaporation and blow
down, this water needs to be replenished.
The total amount of replenishment, known as make-up, is defined
as:
Make-up = evaporation loss + blow down
In addition to the impurities present in the make-up water, any
airborne impurities or biological matter are carried into the
equipment and drawn into the re-circulating water. Over and above
the necessity to blow down a small quantity of water, a water
treatment programme specifically designed to address scale,
corrosion and biological control should be initiated when the system
is first installed and maintained on a continuous base thereafter.
Moreover there must be an ongoing programme of monitoring in
place to ensure the water treatment system is maintaining the
water quality within the control guidelines.
Check and adjustments of blow down depends on the blow down
device actual in use.
To prevent excessive build-up of impurities in the circulating water, a
small amount of water must be « bled » from the system at a rate to
be determined by the water treatment regime. The amount of blow
down is determined by the design cycles of concentration for the
system. These cycles of concentration depend on the quality of the
make-up water and the design guidelines for the quality of the
recirculating water given below.
Cycles of concentration are the ratio of the dissolved solids
concentration in the circulating water compared to the dissolved
solids concentration in the make-up water. The blow down rate can
be calculated as follows :
Blow down = Evaporation loss / Cycles of concentration - 1
The evaporation loss is not only function of the heat load but also
depends on climatic conditions, the type of equipment used and the
method of capacity control, which is applied. The evaporation loss at
summer conditions is approximately 0.431 l/ 1000 kJ heat
rejection. This number should be used for blow down valve sizing
only and not for the calculation of annual water consumption.
Galvanised steel units require passivation in order to prevent white
rust.
Passivation is the formation of a protective, passive, carbonate layer
on galvanised steel surfaces. On newly installed units, to provide
maximum protection from corrosion, one must take special
measures to passivate galvanised steel surfaces.
To ensure proper passivation of the galvanised steel, keep the pH of
the circulating water between 7.0 to 8.2 for four to eight weeks after
start-up, or until new zinc surfaces turn dull grey in colour. If white
deposits forn on galvanised steel surfaces after the pH is returned to
normal service levels, itmay be necessary to repeat the passivation
process.
NOTE: Stainless steel units and units protected by additional coating
do not require passivation.
The growth of algae, slimes and other micro-organisms, if
uncontrolled, will reduce system efficiency and may contribute to
the growth of potentially harmful micro-organisms, such as
Legionella, in the recirculating water system.
Accordingly a treatment programme specifically designed to
address biological control should be initiated when the system is
first filled with water and administered on a regular base thereafter
in accordance with any regulations that may exist or in accordance
with accepted codes of good practice.
It is strongly recommended to monitor the bacteriological
contamination of the recirculating water on a regular base (for
example, TAB test with dip slides on a weekly base) and record all
results.
If a chemical water treatment is used, it must meet the following
requirements:
1. The chemicals must be compatible with the materials of
construction used in the cooling system.
2. Chemicals should be fed into the re-circulated water to avoid
localised high concentrations, which may cause corrosion.
Chemicals are normally fed into the pump discharge line. Batch
feeding of chemicals does not afford adequate control of water
quality and is not recommended.
3. Acid water treatment maybe used on evaporative cooling
equipment as long as the requirements 1 and 2 listed above are
maintained. When chlorine is added to the system, free residual
chlorine should not exceed 1 ppm. Exceeding ths limit may
accelerate corrosion.
It is strongly recommended to check the key parameters of the
circulating water quality on a monthly base. See table: Circulated
Water Quality Guidelines. All test results need to be recorded.
About Water Care
Property of Water
Recommended Level
pH
6.5 to 9.0
Hardness (as CaCO
3
)
30 to 750 ppm
Alkaline (as CaCO
3
)
500 ppm max.
Total Dissolved Solids
1500 ppm max.
Chlorides
250 ppm max.
Sulfates
250 ppm max.
Conductivity
1800 µS/cm
Silica
150 ppm max.
Table 1: Circulated Water Quality Guidelines
Passivation
Biological Control
Chemical Treatment