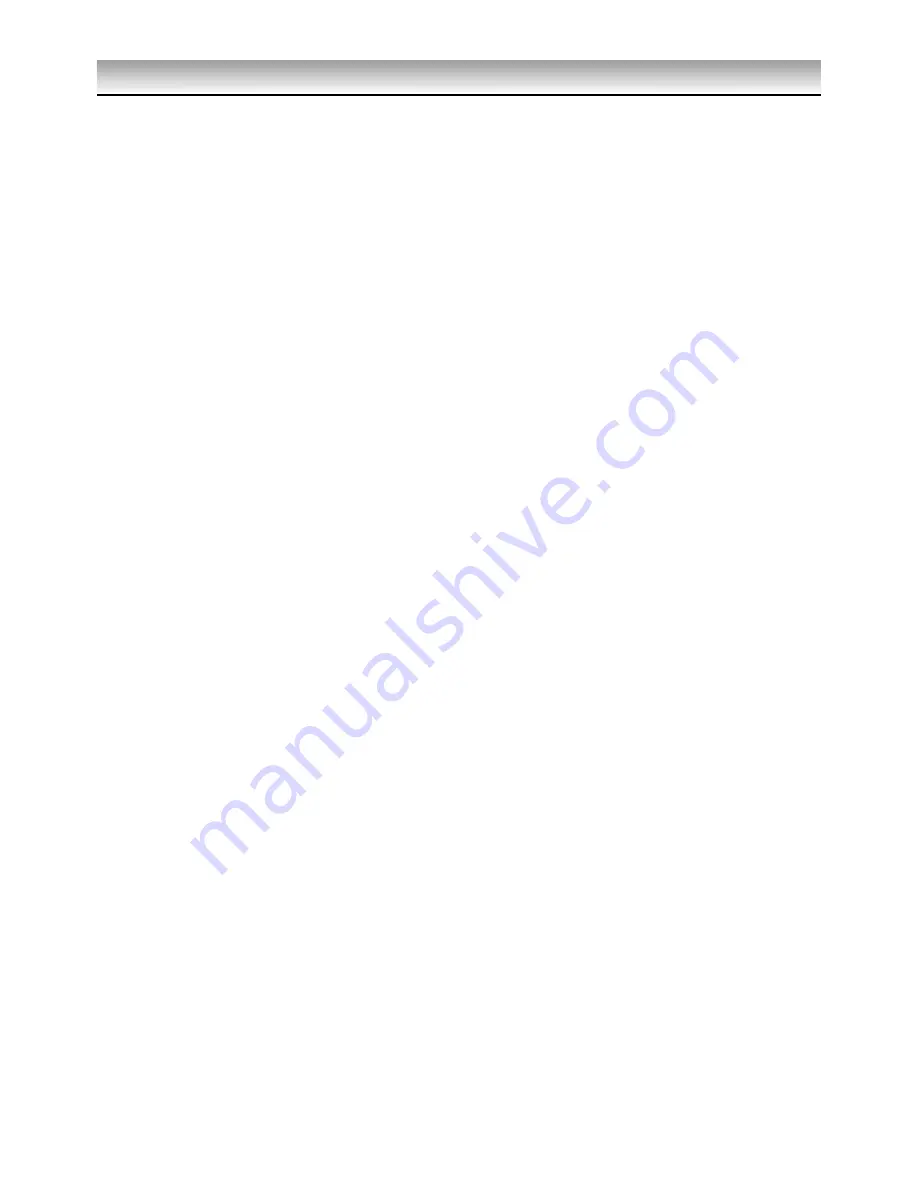
Gear change
A reeded knob screwed into the front of the headstock, it locates in a slot
cover knob
in the change gear cover, and is used to secure the cover shut. It is
unscrewed to release the cover to allow it to be swung open.
Tailstock
A machined casting that accurately fits to the lathe bed. It carries the tailstock
barrel. The tailstock barrel is machined with a No. 1 MT, which allows the
accessories to be mounted (centers, drill chucks, reamers etc). The tailstock
is positioned on the bed by a clamp mechanism at the front of the tailstock
body. The clamp is tightened by the two caphead bolts in the front flange of
the casting. The Tailstock is capable of being offset to allow for taper turning.
The offset locking screw is on the right of the tailstock.
Tailstock barrel
Wheel and rod handle that controls the backward and forward movement of
control
the barrel in the tailstock. The barrel has a travel of 22mm, to allow the
tailstock tooling to be brought into controlled contact with the workpiece,
this is indicated on a coarse scale engraved on the barrel itself. The scale
indicates –0 and then 20 plus two (x1mm) divisions. The supplied tailstock
centre will self eject at –0. The tailstock control has a graduated ring (thimble)
mounted on the neck of the handle so that the amount of movement can be
measured.
Tailstock barrel
Small ‘petal’ knob that locks the barrel in place once it has been moved into
lock
the required position.
Leadscrew
The leadscrew is a threaded shaft that is anchored into a housing machined
into the end of the lathe bed. The shaft runs virtually through the centre axis
of the underside of the bed, and is engaged in a dog fixed to the underside of
the saddle, enabling the saddle to be driven back and forth along the main
axis of the bed. The fixed dog is well supported from the front apron of the
saddle, and combined with effect of the centralized axis of the leadscrew,
results in a very smooth ‘judder’ free movement. The leadscrew can be driven
from either end,from the headstock end, via the change gear train, for auto
feed and thread cutting, or manually by the leadscrew drive handle.
NOTE
The leadscrew is permanently engaged into the saddle dog. Any
movement of the leadscrew is transmitted to the saddle.
Leadscrew
Wheel and rod handle locked onto the end of the leadscrew shaft. Turning the
drive handle
handle will turn the leadscrew and drive the saddle back and forth along the
main axis of the lathe. There is a graduated ring (thimble) on the neck of the
handle to allow the movement of the saddle to be measured.
Motor securing
Two caphead bolts that screw through the change gear compartment
bolts
bulkhead and into the motor flange. The holes through the bulkhead are
elongated to allow the motor to be moved slightly to maintain the drive belt
tension.
Leadscrew
This is a small hole situated between two caphead bolts on the lower right
oiling point
face of the saddle apron. The oil gallery gives direct access to the leadscrew
dog, and enables oil to be spread onto the leadscrew (which is mainly
obscured beneath the lathe bed.)
Motor brush
Two brush caps located top and bottom of the motor, they are accessed by
caps
removing the splash guard.
Parts Identification and Description (Continued)
12
Содержание SIEG C1 MK2
Страница 18: ...18 Illustrated Parts Breakdown for the Micro Lathe Part 1...
Страница 19: ...19 Illustrated Parts Breakdown for the Micro Lathe Part 2...
Страница 20: ...20 Illustrated Parts catalogue for the Micro Lathe Part 1...
Страница 21: ...21 Illustrated Parts catalogue for the Micro Lathe Part 2 PC Board Replacement Part No Part No 600883...
Страница 23: ...23 Change Gear Table Fig 8 Fig 9...