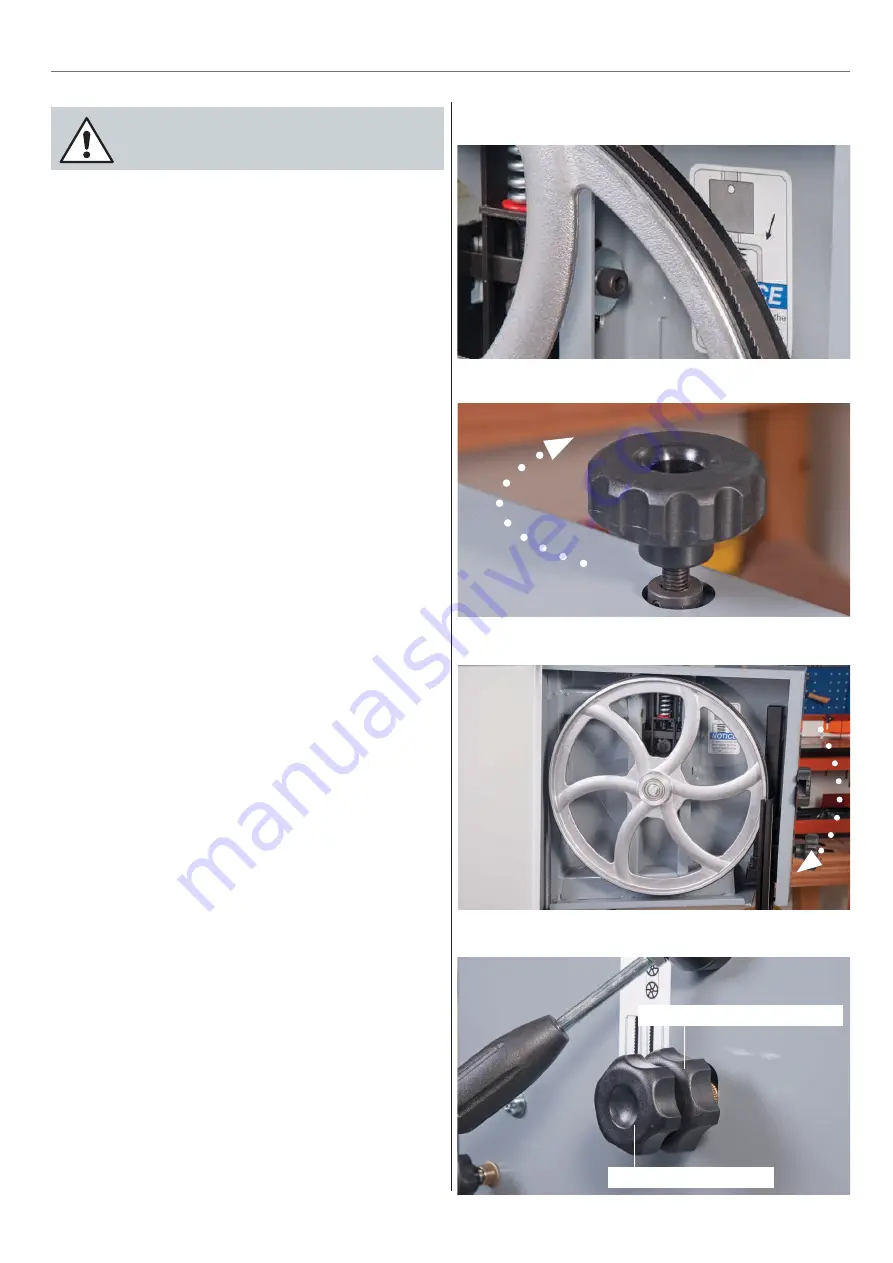
SETTING UP THE SAW
21
Open the front covers fully, giving good access to the
top compartment of the saw and good visibility into
the bottom compartment (see page 17). For tracking
the blade first adjust all bearing guides so that they’re
well clear of the blade. Check that the blade is sitting
approximately in the middle of the wheels, see fig 53.
Apply some tension to the blade by turning the
tensioning wheel clockwise, see fig 54 spin the top wheel
by hand and check that the blade remains centrally on
the tyre, see fig 55. If it does not, adjust the tracking by
turning the tracking control at the rear of the head box,
see fig 56. Viewed directly onto the tracking control
wheel, turning clockwise should cause the blade to track
to the rear of the tyre; anti-clockwise to the front, DO
NOT make large adjustments).
Spin the top wheel again, check again. Continue until
the blade tracks in the centre of the tyres with no
appreciable to and fro movement. Tighten the tracking
control knob to lock the setting. Tension the blade fully. A
sideways push of about 7-8 lbs( 3+kgs) in the middle of
the blade should allow a 1/4” (6.5mm)distension. Check
the tracking again, adjust if necessary. Check that the
drive belt is tensioned correctly. If it is slack, apply ‘take
up’ pressure to the belt by loosening the motor locking
Hex bolt (A) and pushing down the motor assembly until
the belt is under tension then re-tighten the Hex bolt to
lock the motor in position, see fig 57-58.
Connect the power to the machine. Stand clear and start
the saw. Check that the saw is running smoothly, (no
thumps, bumps, knocking or excessive vibration) and the
blade appears to be tracking correctly (in one place). You
can check this by holding a marker, e.g. a pencil, close
to the back of the blade (approach from the back of the
blade only) and check that the gap remains constant.
If it doesn’t, adjust the tracking until it does. Make very
small adjustments and wait for the saw to react before
you adjust again, sometimes the reaction is not
instantaneous. Once you are satisfied that the tracking
is correct, switch the machine off and allow it to run to
a complete stop.
Tensioning and tracking the blade
Make sure both top and bottom blade guides
are well clear of the blade
DISCONNECT THE SAW FROM
THE MAINS SUPPLY!
Fig 53
Fig 54
Fig 55
Fig56
Tracking control knob
Tracking control knob lock
Continues over....
Содержание 107659
Страница 1: ...AP2552B Bandsaw Code 107659 AT 12 05 2022 BOOK VERSION 07 ...
Страница 4: ...4 5 6 7 WHAT S INCLUDED 4 2 2 3 ...
Страница 5: ...WHAT S INCLUDED 5 10 9 8 15 14 13 12 11 16 17 18 19 20 21 22 23 24 25 26 ...
Страница 29: ...EXPLODED DIAGRAMS LISTS 29 Continues over Main Saw Assembly ...
Страница 35: ...WIRING DIAGRAM 35 ...