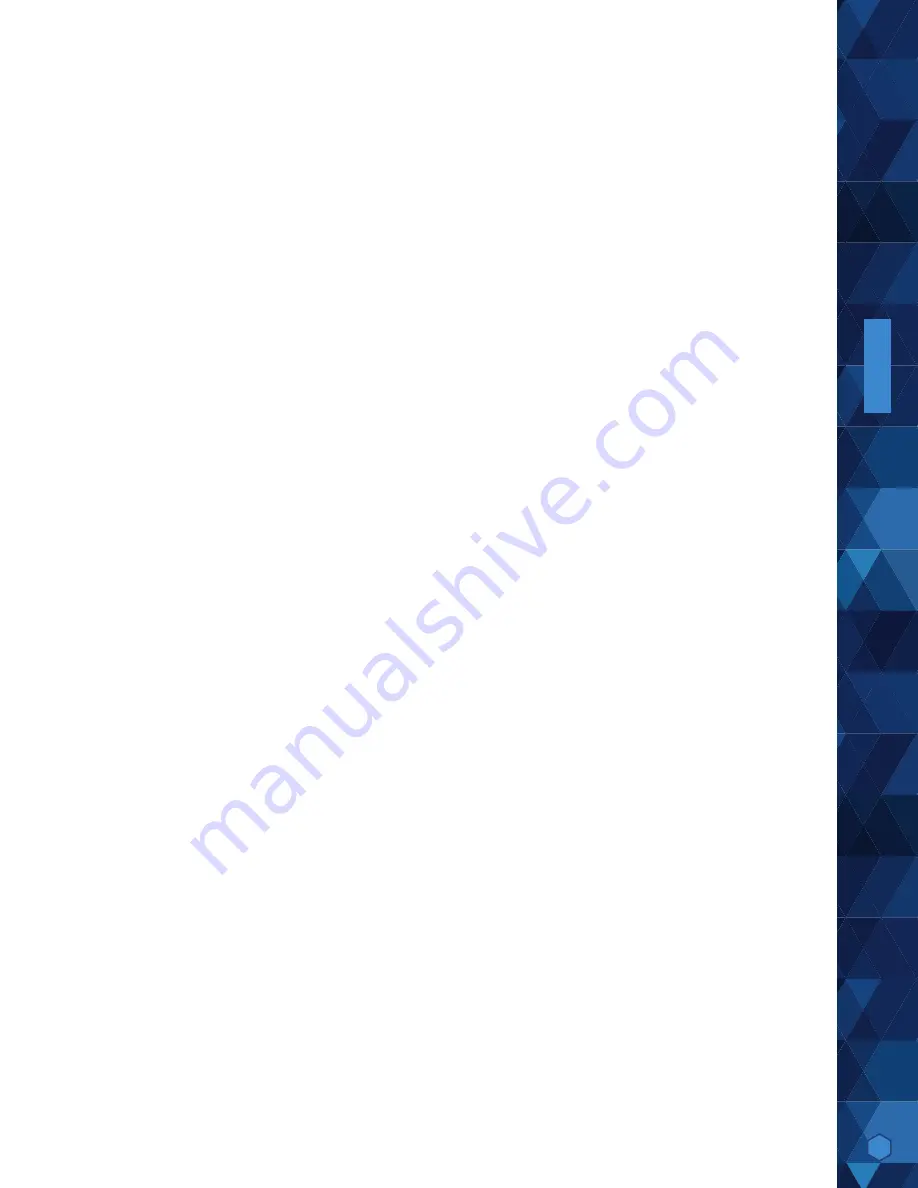
9
S
Y
S
TEM C
OMPONENT
S
PRIMAR
Y INSPECTION
OPERA
TION
PRIMING
C
ONTR
OLLER
C
OMMISSIONING
MAINTENANCE
REV0303HC300010318
OPERA
TION
O
VER
VIEW
2. Connect the Suction hose to the System Inlet Port.
3. Connect the Discharge Hose to the System Discharge Port
4. Check all connections for integrity.
5. Install a large micron (200µ or larger) bag filter in the Bag Filter Vessel and close vessel securely.
6. Ensure no fine filters are in either of the last two filter vessels.
7. Open the Inlet Ball Valve.
8. Open the Discharge Ball Valve.
9. Insert suction “stinger” into the tank and secure.
10. Insert discharge hose into separate container for disposal (removal of unwanted contaminants).
11. Verify that the “MANUAL/OFF” switch is in the “OFF” position.
12. Connect the system to an appropriate power source.
13. Verify that the Variable Frequency Controller dial is set at 20-30, so that the pump motor will start at lower intial speed.
14. Switch the Smart Filtration Controller circuit breakers to on - the “System Power” light illuminates.
15. Switch the Smart Filtration Controller to “MANUAL” to begin pumping.
16. If the pump does not start, toggle the Variable Frequency Controller Lever switch to “Start”. This will be necessary for
the first cycle after the Smart Filtration Controller circuit breakers are switched on.
17. Observe System Priming.
18. Check for leaks or other abnormalities.
19. If anything deviates contact AXI International immediately
Phase 2:
After removing the bulk of the sludge and water from the tank into a separate container for disposal, the return hose is now
inserted into the tank, ending Phase One. The goal of Phase Two is to remove any additional free water within the tank and
also remove any large contaminants and sludge. This phase will clean the fuel and should be a precursor to using the more
expensive fine filters (which are higher efficiency and cost). It should be noted that meeting required cleanliness codes is
typically not possible with pre-filtering alone. Phase Two is used to extend the life of the fine filters, and remove the worst of
the contaminants, before polishing with fine filters to meet the required cleanliness.
1. Insert blue/black discharge hose into tank as far away from the suction hose as possible. In some cases, it is
recommended to remove the sending unit cover to gain sufficient access to the tank. In some cases, both hoses will
have to be inserted through the same tank fill opening.
2. After verifying that both hoses are properly placed in the fuel tank and that the valves on the MTC system are in the
correct position, switch on the pump and ensure proper fuel flow.
Depending on the amount of contaminant in the tank, we recommend you stop the pump shortly after priming and check for
free water and sludge by draining the water from the bottom of the pre-filter.
Check the sump of the pre-filter periodically for build-up of free water.
3. The MTC should be kept running in the Phase Two recirculating mode until clean fuel samples can be drained from the
pre-filter. Then, switch off the pump for final polishing.
Содержание MTC HC-300
Страница 23: ...NOTES...