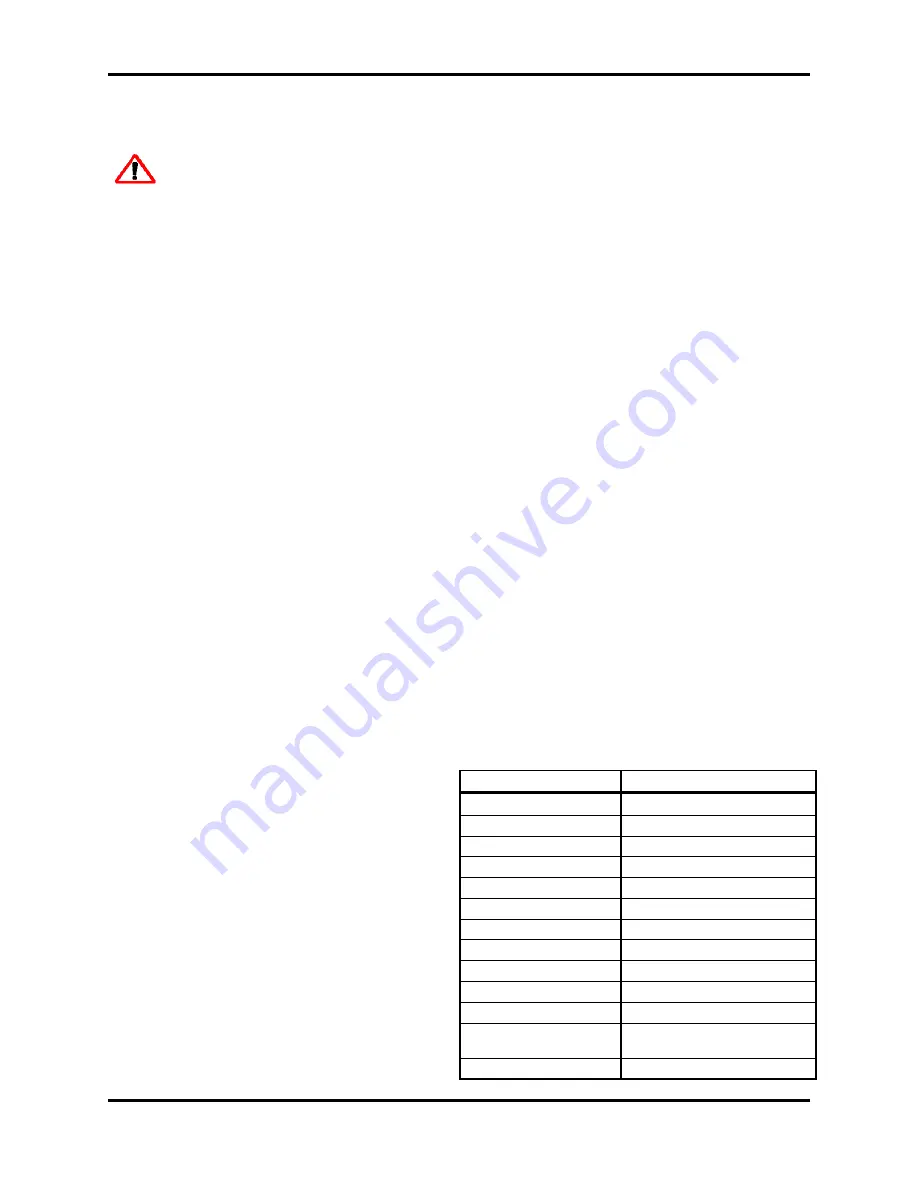
Page 2
Installation and General Maintenance Recommendations
WARNING: INSTALLATION
and MOUNTING
The user of these devices must conform to all
applicable electrical, mechanical, piping and
other codes in the installation, operation or repair
of these devices.
INSTALLATION! Do not attempt to install,
operate or repair these devices without proper
training in the technique of working on
pneumatic or hydraulic systems and devices,
unless under trained supervision.
Compressed air and hydraulic systems
contain high levels of stored energy. Do not
attempt to connect, disconnect or repair these
products when a system is under pressure.
Always exhaust or drain the pressure from a
system before performing any service work.
Failure to do so can result in serious personal
injury.
MOUNTING! Devices should be mounted and
positioned in such a man
n
er that they cannot
be accidentally operated.
Installation and General
Maintenance Recommendations
Before installing the Controlair
®
Valve, all air lines
in the system should be cleaned to remove all
dirt, moisture or contamination.
A strainer is furnished on the inlet port to protect
the valve from large particles or foreign matter in
the supply line. To insure long, trouble-free
service, a 10 micron or better filter should be
installed in the supply line to the valve.
The HG-2 Controlair Valve is designed for panel
mounting. The valve less the pipe bracket can be
installed from the top of the panel. Refer to the
installation view for panel opening dimension.
Allow suitable clearance for installing or removing
of the (3) pipe bracket screws which are 2 1/8”
long (54 mm).
GENERAL MAINTENANCE and
REPAIR RECOMMENDATIONS
Maintenance periods should be scheduled in
accordance with frequency of use and working
environment of the Controlair Valve.
All valves must be visually inspected for wear
and given an “in System” operating
performance and leakage test at least once a
year. If these visual observations indicate valve
repair is required, the valve must be removed
immediately and repaired.
A major overhaul is recommended at one
million cycles. However, where frequency of
use is such that it would require more than two
years to obtain the one million cycles, the valve
must be overhauled at the two year period.
When it is determined that the Controlair Valve
requires a major repair as a result of the one
million cycles, one year routine inspection or the
two year service period has elapsed, the device
must be disassembled, cleaned, inspected,
parts replaced as required. The valve then
must be tested for leakage and proper
operation prior to installation, refer to the Major
Repair and Maintenance Instructions and test
procedures.
Notice that the operating portion of the valve
can be removed without disturbing the pipe
connections by just removing the (3) screws
that hold the pipe bracket to the valve.
No special tools are required to maintain the
Controlair valves, with the exception of internal
snap-ring pliers.
One complete Controlair valve should be kept in
stock for every (4) valves in service. During the
maintenance period, replacing the complete
valve with the stand-by unit reduces production
down time and affords inspection and
replacement of parts at a more appropriate time
and favorable location.
Technical Data:
Max. Operating Pressure
200 psi (13.8 bar)
Admissible Mediums
Clean & Dry Compressed Air
Operating Temperature
-40° to 160°F (-40° to 71°C)
Hysteresis
1 1/2 psi (.10 bar)
Control Pressure Range
Ref. Identity Chart
Pressure Change
1 1/2 psi (.10 bar)
Mounting
Flanged Plate
Port Size
1/4”-18 NPTF
Materials
Controlair Valve
Housing & Body
Die Cast Aluminum
Internal Parts
Brass, Rubber, Aluminum,
Steel, Plastic and Hytrel™
Weight
9 LB. (4.1 kgs.)