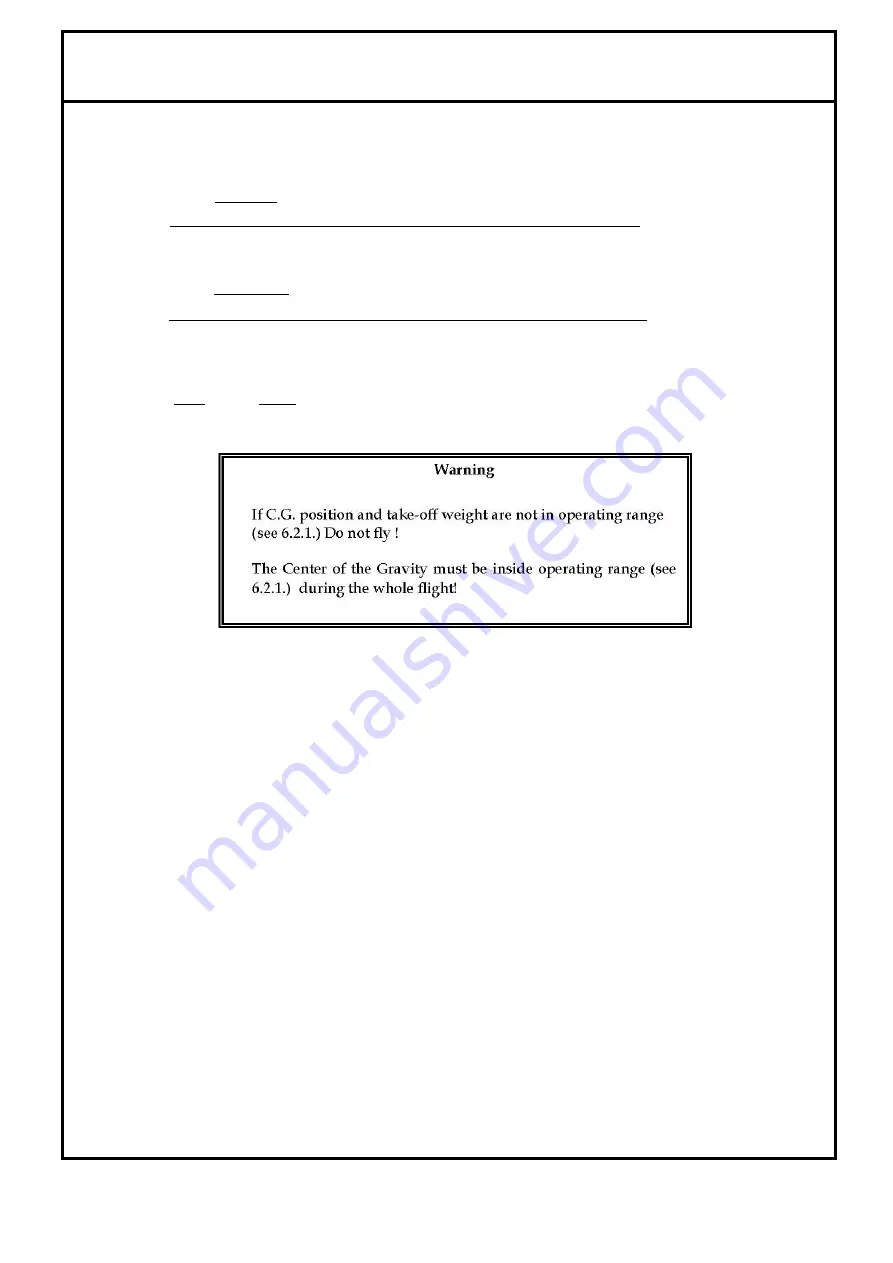
VL-3E-1 Pilot Operating Handbook
date of issue:
32/40
C.G. position
m
m
+
vp
+
m
+
m
+
b
x
m
=
x
z
p2
p1
sat
bsat
pr
1467
215
0.725
682
682
100
mm
=
+
+
+
+
=
x
346
443.6
1467
10
215
0.725
45
682
0
682
100
100
1236
17.1
301
xt =
x
b
SAT
×
100
=
346
1236
×
100
=
28
%b
SAT