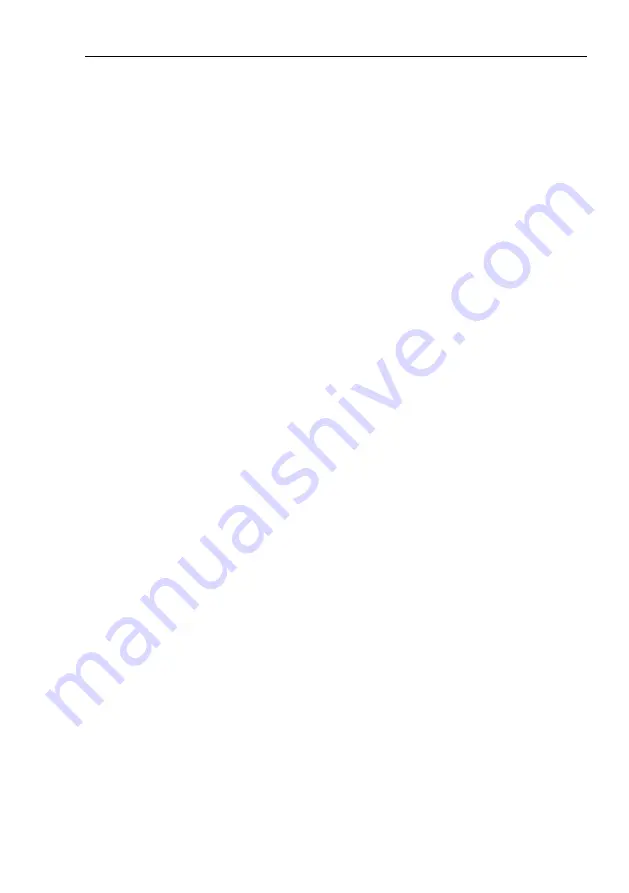
Autopilot Installation Manual
6.1
Elevator
gradually until you achieve proper response. Proper response of the aircraft
has a small overshoot and small steady-state error. Make sure that
I-term
of VS loop is at least twice the
I-term
of pitch loop.
D-term
After
I-term
set small
D-term
for the VS loop. Start with small
value. The starting
D-term
should be around
I-term
/20. Increase it only if
you do not observe any oscillations. The maximum
D-term
should not exceed
I-term
/5.
Testing
After tuning the operator should test the
PID
-terms with different
vertical speeds, both in climb and in descend. Please note the autopilot will
not automatically adjust the airspeed. If the airspeed is too high or too low
the autopilot will disengage. Make sure that during the tests the aircraft stays
within operational limits.
37
©
Kanardia
2016-2020
Содержание Kanardia
Страница 1: ...Autopilot Installation Manual Kanardia d o o November 2020 Revision 2 1 ...
Страница 2: ......