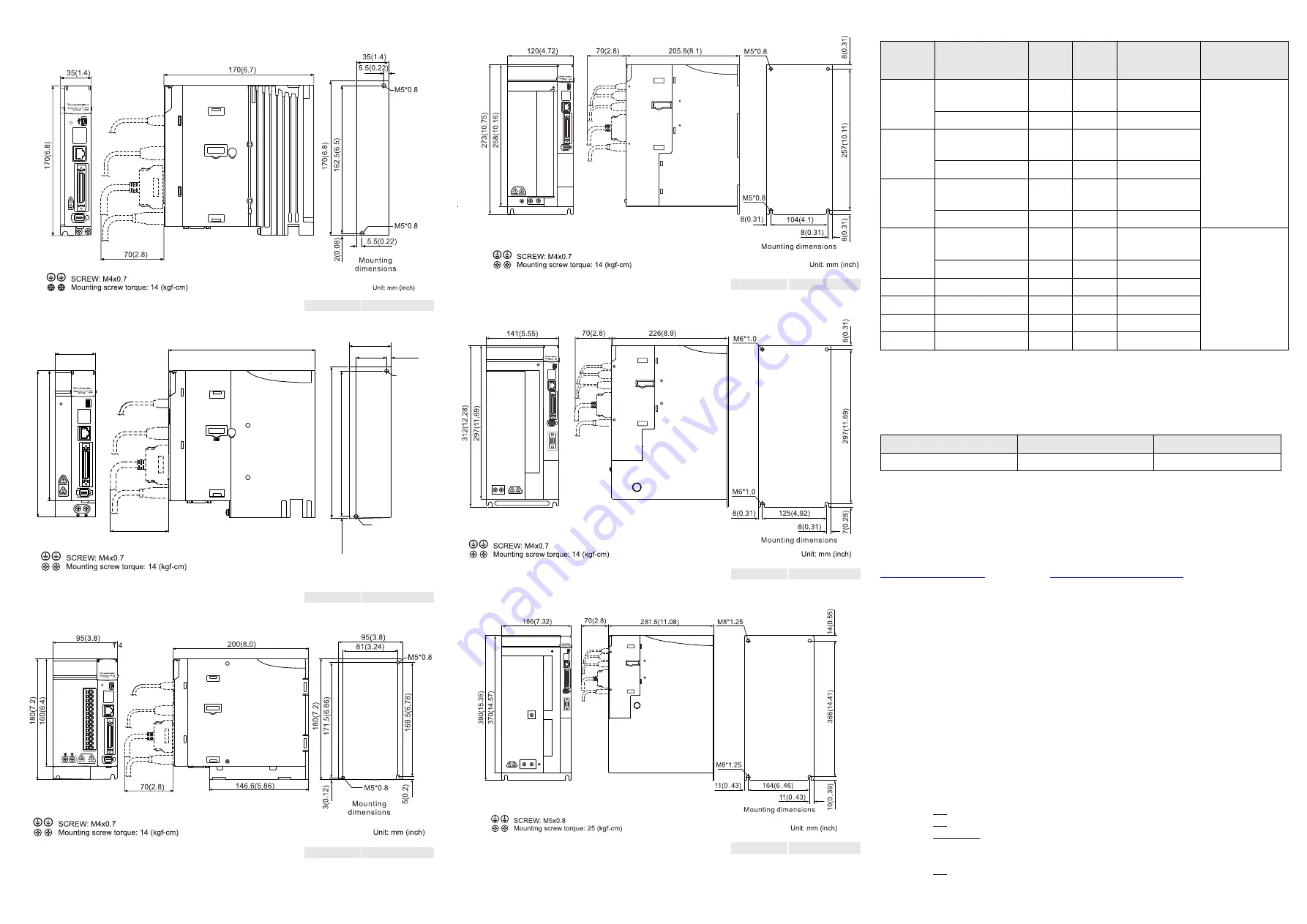
(9) Dimensions and weight of servo drive
SV2A-2040 model
SV2A-2075, SV2A-2150 models
180(7.1)
70(2.8)
5.5(0.22)
50(2)
36.3(1.43)
2
.1
(0
.0
8
)
1
8
0
(7
.2
)
1
7
2
.5
(6
.9
)
M5*0.8
M5*0.8
1
6
0
(6
.3
)
50(2)
1
8
0
(7
.2
)
Unit: mm (inch)
M ou nti ng
di men si on s
Weight
1.3 kg (2.87 lb)
SV2A-2200, SV2A-2300 models
Weight
2.7 kg (5.94 lb)
SV2A-2550 model
Weight
5.5 kg (12.13 lb)
SV2A-2750 model
Weight
7.5 kg (16.53 lb)
SV2A-2F00 model
Weight
15 kg (33.07 lb)
Note: the values displayed in the above figures are measured in metric units. The values displayed in imperial units are
for reference only.
(10) Circuit Protection (maximum allowable values)
Servo drive
model
Main Voltage Level
Drive
Rated
Input
Circuit
breaker
Fuse
Fuse Class
SV2A-2040
100-120VAC 1-phase
200-230VAC 1-phase
3.98 A
4.69 A
10A
15A
Class CC
200-230VAC 3-phase
2.76 A
10A
10A
SV2A-2075
100-120VAC 1-phase
200-230VAC 1-phase
7.73 A
8.71 A
20A
20A
200-230VAC 3-phase
5.09 A
13A
15A
SV2A-2150
100-120VAC 1-phase
200-230VAC 1-phase
12.56 A
14.82 A
30A
30A
200-230VAC 3-phase
8.09 A
20A
25A
SV2A-2200
100-120VAC 1-phase
200-230VAC 1-phase
18.03 A
20.83 A
40A
40A
Class J
Or
High Speed J*
200-230VAC 3-phase
11.36 A
30A
35A
SV2A-2300 200-230VAC 3-phase 14.52 A
35A
50A
SV2A-2550 200-230VAC 3-phase 27.06 A
60A
70A
SV2A-2750 200-230VAC 3-phase 37.33 A
70A
80A
SV2A-2F00 200-230VAC 3-phase 69.95 A
120A
125A
* Edison JHL fuses
These circuit protection values are the
maximum
values allowed by UL. See section
3) Wire Selection
for recommended wire and circuit protection values. Always follow all local and national electrical codes
when selecting circuit protection.
Separate fuses/breakers can be used for the control circuit. Install two fuses or a double pole breaker if
the control power will be using two phases of a 3-phase system. Due to inrush, each drive control circuit
should have separate circuit protection (don’t supply two drives with one breaker).
Control Power
Circuit breaker
Class CC Fuse
All models
5A
6A
(11) Quick Start Guide
This section will show how to safely and quickly start up a SureServo2 (SS2) drive. Wiring and starting
up the drive should only be performed by a qualified professional. High voltage levels are in use.
Commissioning is quicker and easier using the drive configuration software SV2-PRO, but the entire
start-up procedure can be accomplished with the keypad (detailed here). For further information and
more complete startup instructions, please download the SureServo2 User Manual (SS2 UM) from
www.automationdirect.com/videos
SureServo2 commissioning, programming, and operation.
Preliminary Wiring
To safely and quickly start up a SureServo2 (SS2) drive, several different types of wiring need to be
verified first. Until this wiring and functionality is verified, it is highly recommended to NOT connect main
incoming power (R,S,T) or connect the load to the motor shaft.
1.
Connect the ground wires to the screws at the bottom of the drive. Connect the incoming
ground to one screw and connect the motor ground to the other screw. (The motor ground
wire is in the motor cable SV2C-Pxxx-xxxx.)
2.
Connect the wiring for L1C and L2C (single phase 100-120VAC or 200-230VAC). This is
control power and should be continuously available (not disconnected with E-stop, etc.).
3.
Connect an appropriate safety circuit to CN10. See the wiring diagram elsewhere in this
document or the SureServo2 User Manual. Although the CN10 connector comes pre-wired
with an STO bypass, it is strongly recommended to wire a safety relay to connect
STO_A
to
/
STO_A
and to connect
STO_B
to
/
STO_B
.
4.
Connect the motor encoder cable (SV2C-
E
xxx-xxxx) to the motor and to CN2 of the drive.
5.
Connect the appropriate 24VDC input devices to DI1-DI10. Pay close attention to these
Digital Input (DI) definitions. Their default (out-of-the-box) configurations are listed below.
DI1 = Servo On input (wired normally open)
DI5 = Alarm Reset (wired normally open)
DI6 and DI7 = Overtravel inputs. Inputs are wired normally closed (in a fail-safe manner).
If the application is rotary and has no overtravel inputs, these inputs can be temporarily
wired to DC common (0 volts) or disabled thru programming (procedure shown below).
DI8 =Override (temporary Motor Stop input wired normally closed). NOTE: The STO input
(CN10) is separate from the Override (temporary Motor Stop input wired normally closed)
input DI8.
Weight
0.92 kg (2.02 lb)