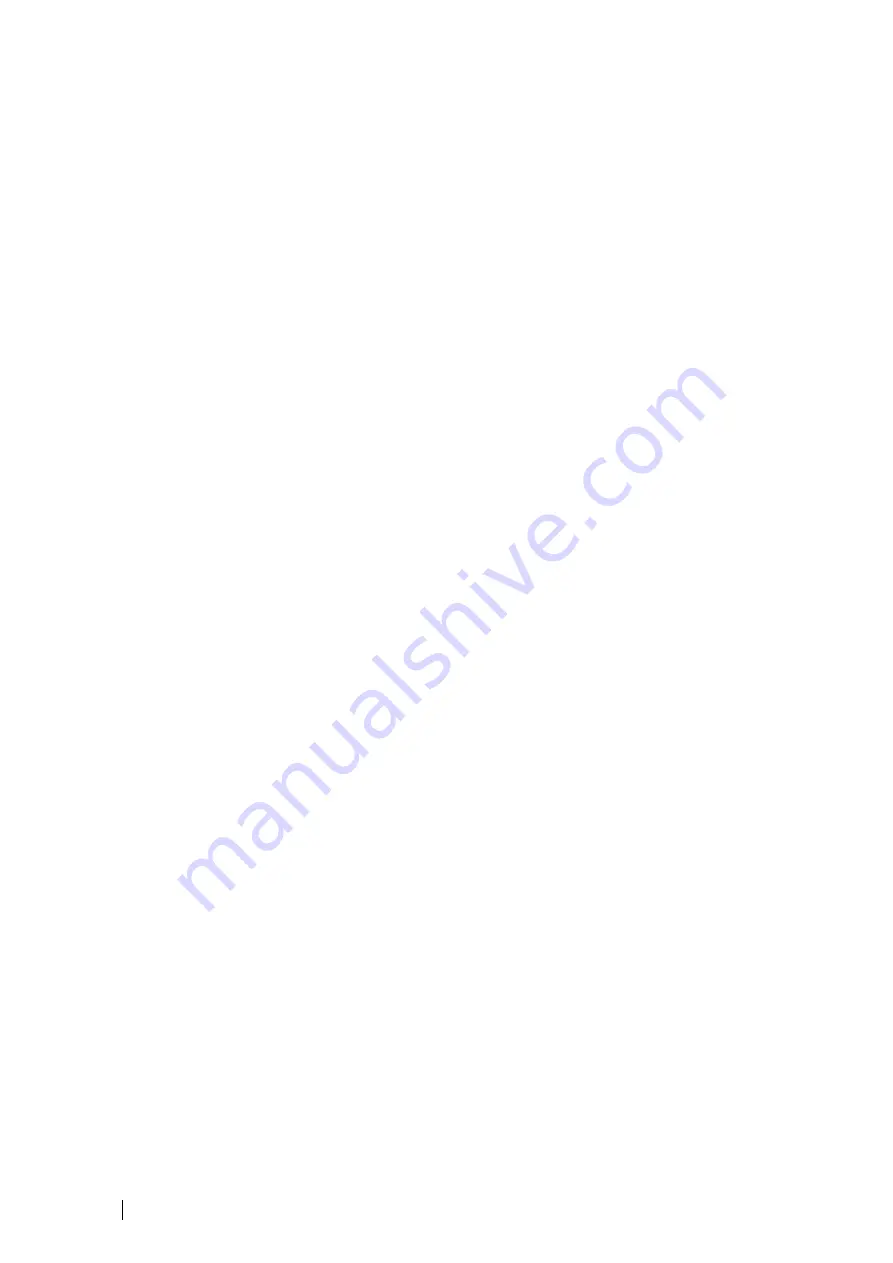
Copyright of RotorSport UK Ltd
Document number RSUK0060
Page 47 of 101 Page issue
6
, dated
12
.0
4
.1
6
LANDING
Before making the approach check all key equipment and functions.
Ensure brakes are not locked on, and backup electric fuel pump turned on.
The landing should take place into wind where practical/permissible. Maximum crosswind
limitation is 15kts.
Reduce engine rpm and speed to 60mph on short final.
Final approach speed should not be under 50mph. If in turbulence or rain, 60mph. As the
aircraft closes to the ground, reduce the speed by flaring and touch down with the main
wheels. Hold the stick back to use the rotor as a brake, and reduce speed for taxy.
Reduce engine power as required for taxy or idle if at rest.
When required, turn pneumatics selector switch to ‘BRAKE’ (system minimum pressure
2bar for switch to change over) to engage the rotor brake and automatically push the stick
forwards. The brake pressure may be increased by use of the “aft trim” control, up to
maximum system pressure (8bar nom).
Take care in windy conditions to prevent blade flap, and move stick into wind if needed!
Blades can be parked fore and aft the aircraft by either manually increasing the brake
pressure at the appropriate time by pulling the stick rearwards, or by depressing the brake
interlock release button, and momentarily engaging the prerotator. A little practice may be
required.
Caution: If the stick is moved in this way use only a small movement (no more than half
travel), because:
the leverage increases the pressure in the system, which could exceed allowable
pressure 10bar
the slow moving rotor blades will have reduced clearance to the tail
Do not taxy with the rotors parked across the aircraft. The advancing blade will try to lift,
and the retreating blade will be stalled, leading to a significant load pushing the stick to
the left.
Park into wind to ensure the canopy is not blown open or shut.
After engine has idled for at least 30secs (2mins for a 914UL due to the extra heat
generated – if stopped early the hot engine oil may carbonise in the turbocharger bearing
and result in expensive damage), turn the engine off using the ignition switches, and then
turn main switch off. Do not exit the gyroplane until the rotor stops turning.
If the engine and environment is particularly hot, press the ‘Fan’ button before turning off
the keyswitch to prolong electric engine cooling.
NB: If MC-194 and/or SB-044 embodied, pressing the “Fan” button before turning off the
master switch will initiate a ground-cooling sequence in which the cooling fan is reversed
(to aid natural convection cooling) and then runs for a period of 5-6mins (even when the
master switch is subsequently turned off). After this automatic sequence the system will
revert to the normal airflow direction for in-flight cooling.
An emergency landing is made exactly the same way, except that the above speeds
should be maintained in order to ensure sufficient rotor energy is left for the final flare.
NOTE! A 914UL engine can produce significant torque roll when the turbo is engaged in
flight. On a low level go-around this must be considered and countered with an
appropriate control response.