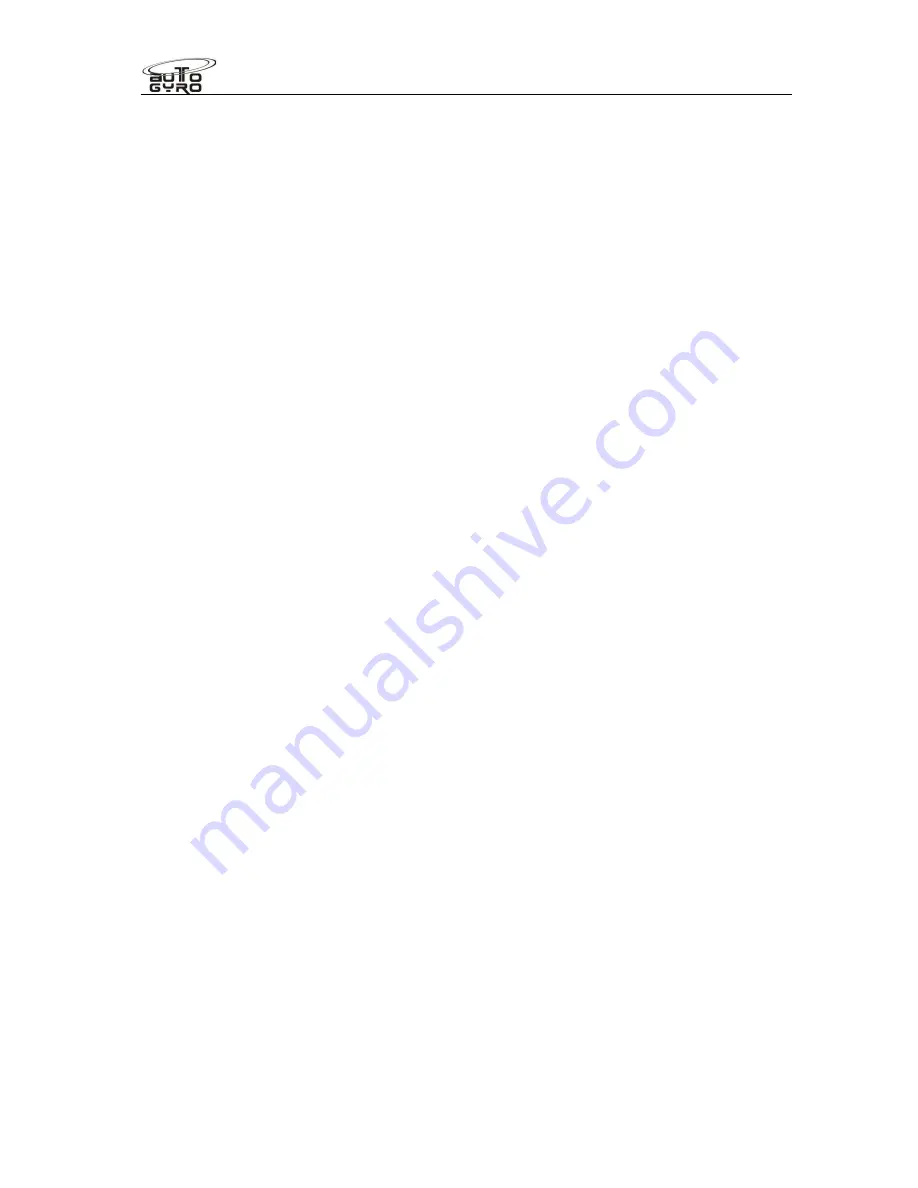
Pilot Operating Handbook
Cavalon Pro
SECTION 3
EMERGENCY PROCEDURES
RotorSport_POH_Cavalon Pro
Revision 1.0 – Issue 2 Date 16 03 2016
3-7
1. Engine and propeller. Vibration in this area will change with engine rpm, and can
therefore be affected and isolated by the pilot. The propeller is normally balanced to less
than 0.1ips, meaning low vibration. Vibration will increase as the propeller gets dirty, and will
also increase if damaged. A sudden change in flight will indicate a fault has developed,
either through an impact (loose luggage, bird strike etc. passing through the propeller) or by
some mechanical failure. In the event the pilot should make a precautionary landing for
evaluation. Propeller damage may also be evident from a change in noise level.
Upon landing, carefully check the propeller for damage, loose bolts or evidence of
mechanical failure within the prop or engine. Especially check the engine to engine bearer
connections, and the engine bearer to airframe connections.
2. Rotor.
Rotors will vibrate in flight due to tracking errors (side to side stick shake), rotor CG
misalignment with the axis of the bearing in the flat plane (oscillatory stick shake), and also
in the vertical plane (two per rev shake). The amount of shake will not suddenly change in
flight or between flights unless there has been mechanical failure, external influence or rotor
strike.
Vibration will increase (and performance decrease dramatically) with dirt build up on the
rotor blades, so before any analysis make sure they are clean.
If there is a change in vibration in flight make a precautionary landing and investigate. If on
rotor startup, stop and investigate.
Check items:
Rotor impact with tail of aircraft.
Hanger damage e.g. twist or distortion of trailing edge.
Blade bent from ground handling.
If after a recent re-assembly of the rotor, that the blades and hubs are serial-number
matched, and that the shim washers are correctly matched to the hub bar and rotor tower.
A reduction in vibration may be caused by increased flexibility between the rotor head and
the occupant. This may be control system looseness, so check all system joints for
tightness, and also for cracks at the base of the mast. Check security of all fastenings
between the rotor and the pilot. Check also for any cracks or other damage to the primary
structure; body, tail, keel tube, rotor head, rotor, mast.
3.8.7
OTHER EQUIPMENT FAILURE
Good judgement must be used in monitoring instruments, and timely action taken should a
reading be in doubt. If in doubt, make a precautionary landing and resolve the issue rather
than continuing a flight.
Actions recommended:
ASI failure: In level flight fly with an engine rpm of 4,200 lightly laden to 5,000 heavily laden
which will give approx 45-60KIAS, propeller in mid pitch range. When descending (nose
down) throttle back to approx 3,000 to 3,500rpm to prevent overspeed. Continue to your
designated landing site, maintaining speed for a flare on landing in the final descent. Leave
plenty of space to land in should the flare be prolonged. Experience will aid judgement of
the best engine rpm to maintain to match the desired flight speed and payload.
Altimeter failure: In a gyroplane it is reasonably easy to judge height. If in controlled
airspace ensure the controlling authority is informed to prevent traffic conflict. Otherwise
continue to a safe landing using navigational skills to avoid potential collisions.
Compass failure: Resort to map, aided by GPS if available, fly at a speed to suit
navigational requirements or make a precautionary landing if unable to identify position.