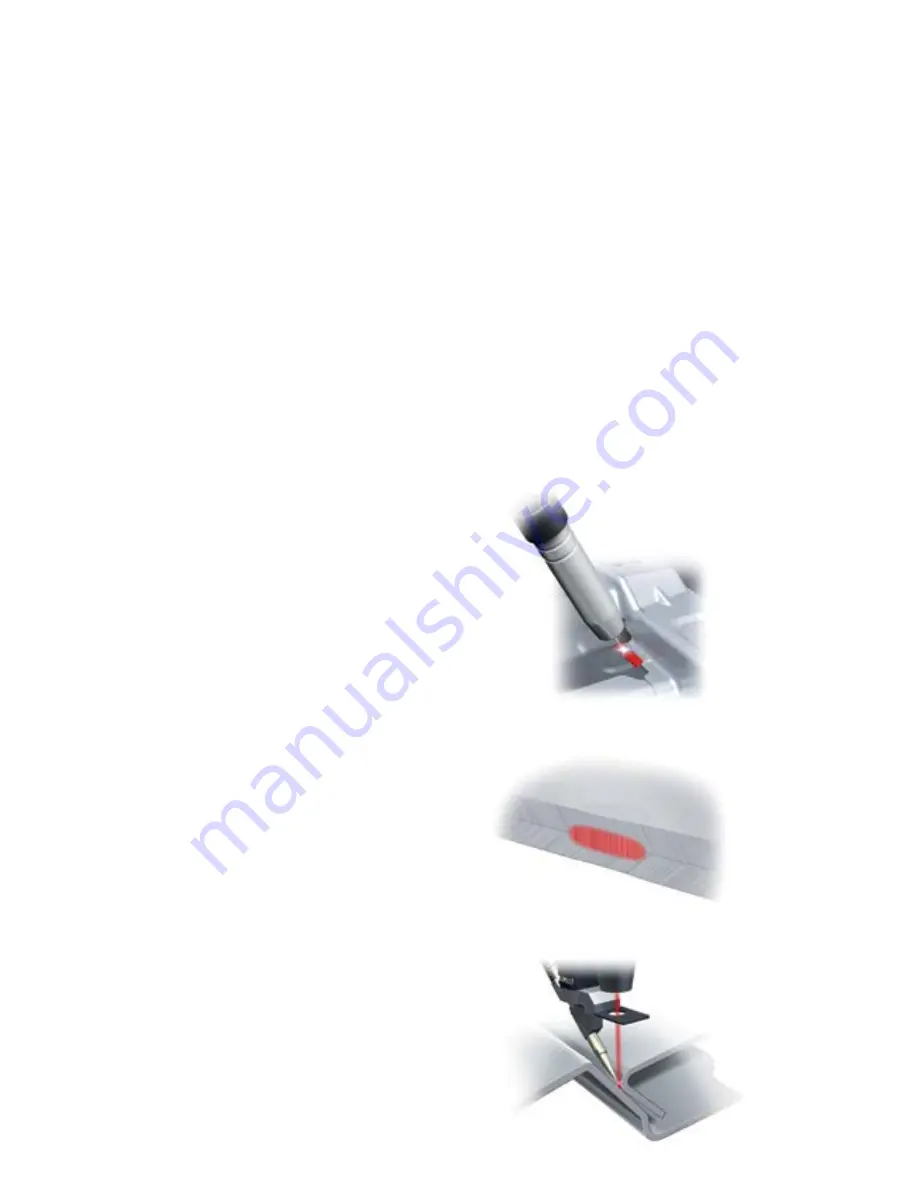
12
Thermal "hot" and mechanical "cold" joining techniques
The choice of the right joining technique in modern body
construction is material-dependent. Welding similar mate-
rials is still the most frequently used joining technique.
These welding and soldering techniques are called "hot"
joining techniques and have a large variety of applications.
However, the heat input causes high internal stresses in the
component, which often can only be compensated through
time-consuming re-work.
The mechanical "cold" joining technique has the decisive
advantage over the thermal joining technique in that hybrid
joints can be reliably produced between different types of
materials. The positive properties of the material are not
adversely affected by thermal influences.
The following "cold" joining techniques are used:
•
Punch riveting.
•
Clinching.
It makes good sense to combine the mechanical spot
joining techniques with bonding methods. First, it increases
the strength of the joint and, second, the adhesive also acts
as insulation in the case of hybrid aluminum/steel joints.
This, in combination with seam sealing, prevents direct
contact between the metals and ensures that corrosion
cannot occur. In addition, a carefully selected adhesive
concept also helps to absorb the differing degrees of
thermal expansion of the individual materials. Cataphoresis
is a fully automated process of painting by immersion,
which is based on the movement of charged particles in an
electric field (paint) towards an oppositely charged pole
(metallic surface to be painted). The main objective of the
coating process is to protect the surfaces from corrosion,
and its properties make it the ideal treatment for this
purpose. This technique also allows areas which are hard to
reach, such as recessed areas, piping etc to be painted.
"Hot" joining technique in the Audi TT
MIG/MAG welding
With the MIG/MAG (MIG = metal insert gas, MAG = metal
active gas) welding technique, an electric arc forms
between the automatically fed welding wire (electrode) and
the workpiece. A shielding gas protects the electric arc and
the welded surface against the ingress of ambient air. The
inert gas and welding wire have to be adapted to the basic
material.
Advantages:
•
Versatility in use.
•
High weld seam strength.
•
Outstanding thin panel properties.
630_076
Resistance spot welding
In the case of resistance spot welding, panels are welded
together using opposed electrodes under the application of
force, pressure and electrical current.
Advantages:
•
No additional connecting element.
•
No heat influence zone.
•
Short welding time.
Laser welding
With laser welding, the focused laser beam serves as an
energy source. In the welding head, the laser beam is
focused by a lens and reflected back onto the workpiece by
mirrors. At the point of contact, the laser beam melts the
workpiece. Welding can be performed both with and
without welding filler material.
Advantages:
•
Less influence of heat.
•
Less thermal distortion.
•
Less time spent on re-work.
630_077
630_065
•
Flow-drill screwing.
•
Seaming.
•
Bonding.
Содержание TT 2016
Страница 1: ...i The 2016 Audi TT Introduction eSelf Study Program 990153...
Страница 4: ...iv...
Страница 63: ...59 Notes...