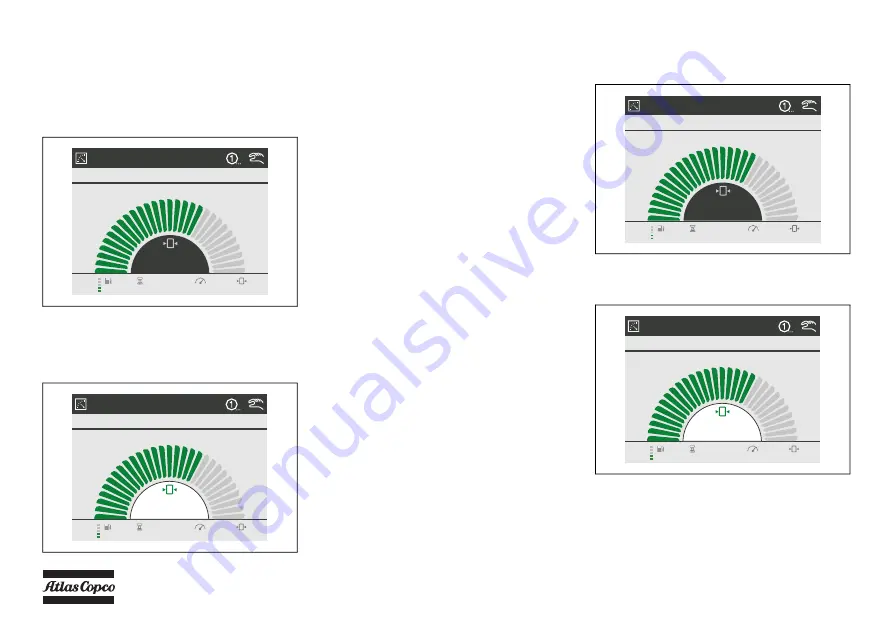
- 46 -
PRESSURE SETTING
To change the pressure setting there are two
possibilities.
1. Choosing between presets
The operator can choose between two preset
pressures.
The current active preset is indicated in the top
right corner of the display: 1 or 2. To switch to the
other preset, go to the Main view and press the
enter button for 2 seconds (the pressure set point
will light up in green).
By pressing the left or the right arrow button the
operator will be notified to:
“Press enter to go to other pressure setting X Y”
When enter is pressed the setting will become
active.
By pressing enter again the controller will go out
of edit mode.
The active preset pressure (1 or 2) will be visible
in the top right corner of the display.
2. Changing the pressure of a preset
The operator can adjust the active preset as
follows.
In the Main view when the operator presses the
enter button for 2 sec. The pressure setting will
light up in green when it is in edit mode.
By pressing the up and down buttons the pressure
setting can be increased or decreased in 0.1 bar
steps.
Pressing the enter button again confirms the
pressure setting and will leave the edit mode.
MAIN VIEW
LOADED
7.2
1424RPM
7.2bar
1286h
40%
MAIN VIEW
LOADED
1424RPM
7.2bar
1286h
40%
7.2
MAIN VIEW
LOADED
7.2
1424RPM
7.2bar
1286h
40%
MAIN VIEW
LOADED
1424RPM
7.2bar
1286h
40%
7.2
Содержание U190 PACE KD WUX
Страница 1: ...Instruction Manual for Portable Compressors English U190 PACE KD WUX Engine Kubota V1505T ...
Страница 2: ......
Страница 16: ... 16 Main Parts ...
Страница 18: ... 18 COMPRESSOR REGULATING SYSTEM ...
Страница 22: ... 22 CONTINUOUS PNEUMATIC REGULATING SYSTEM ...
Страница 26: ... 26 Option circuit diagram 9829380198 01 15kva ...
Страница 27: ... 27 9829380198 02 15kva ...
Страница 28: ... 28 9829380198 03 15kva ...
Страница 29: ... 29 Option circuit diagram 9822108160 01 6kva ...
Страница 30: ... 30 9822108160 01 6kva ...
Страница 31: ... 31 9822108160 01 6kva ...
Страница 32: ... 32 WIRE HARNESS 1094 4377 02 ...
Страница 89: ... 89 Maintenance Log Compressor Customer Serial number Service hours Maintenance action Date By initials ...
Страница 90: ... 90 ...
Страница 91: ......
Страница 92: ......