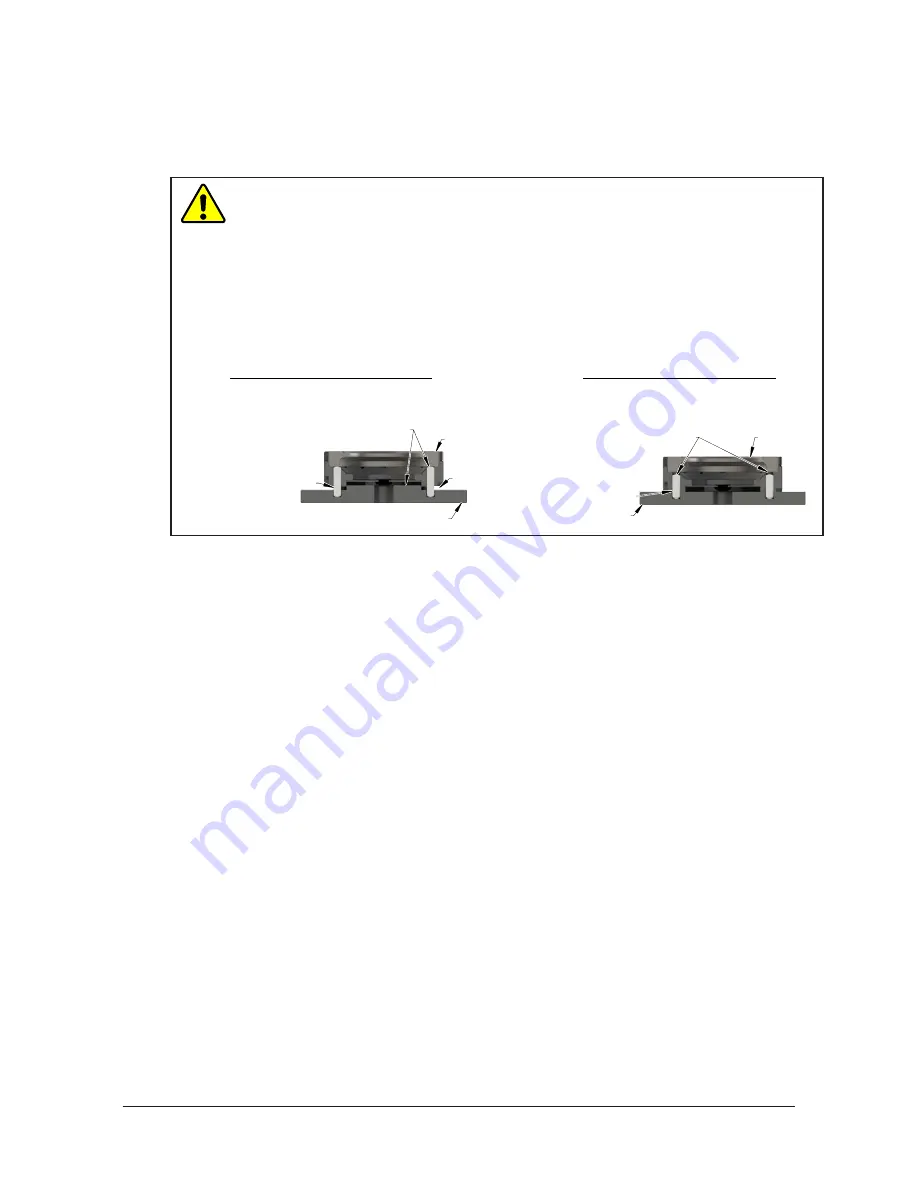
Manual, Tool Changer, QC‑313
Document #9620‑20‑B‑313 Series Base Tool Changer‑06
Pinnacle Park • 1031 Goodworth Drive • Apex, NC 27539 • Tel: 919.772.0115 • Fax: 919.772.8259 •
B-9
2.4 Tool Interface
The Tool plate is attached to the customer’s tooling. An interface plate can adapt the Tool plate to customer
tooling. Alignment features (dowel holes and a recess) accurately position and bolt holes to secure the Tool
plate to customer tooling. Custom interface plates can be supplied by ATI (refer to the application drawing).
CAUTION:
Do not use more than two alignment features when securing a Tool plate
to an interface plate. Using more than two alignment features can cause damage to
equipment. Use either two dowel pins or a single dowel pin, along with a boss/recess
feature to align the Tool plate with the interface plate.
CAUTION:
Do not use dowel pins that are too long or do not allow the interface plate
and Tool body to mate flush. Using dowel pins that are too long will cause a gap
between the interface plate and Tool body and damage the equipment. Use dowel pins
that will not extend further than allowed by the Tool body.
Tool Plate
Interface Plate
Dowel pins are
proper size allowing
interface plate and Tool
Plate to mount flush.
Two dowel pins (or a
boss/recess) used as
alignment features.
Correct Mounting of Tool Plate
Tool Plate
Interface Plate
Dowel pins
are too long and
cause a gap between
interface plate and Tool.
Boss and two dowel pins
as alignment features can be
difficult to align and can
damage equipment.
Gap
Incorrect Mounting of Tool Plate
single dowel pin along with a
If the customer chooses to design and build a tool interface plate, consider the following points:
•
The interface plate should include bolt holes for mounting and either two dowel pins or a dowel
pin and a boss for accurate positioning on the customer tooling and Tool plate. The dowel and boss
features prevent unwanted rotation.
•
Dowel pins must not extend out from the surface of the interface plate farther than the depth of the
dowel holes in the Tool plate.
•
The thickness of the interface plate must be sufficient to provide the necessary thread engagement for
the mounting bolts. Fasteners should meet minimum recommended engagement lengths while not
exceeding the maximum available thread depth. Use of bolts that are too long can cause damage to the
tool side changer.
•
The plate design must account for clearances required for Tool Changer module attachments and
accessories.
•
If a boss is to be used on the interface plate, a boss of proper height and diameter must be machined
into the interface plate to correspond with the recess in the Tool plate.
•
The interface plate must have a hole in its center for manually returning the locking mechanism to the
unlocked position under adverse conditions (i.e. unintended loss of power and/or air pressure). The
center access hole with a minimum diameter of 1” (25.4 mm) prevents debris from contaminating the
locking mechanism. Greater protection is provided by leaving the race cover and grommet in place.