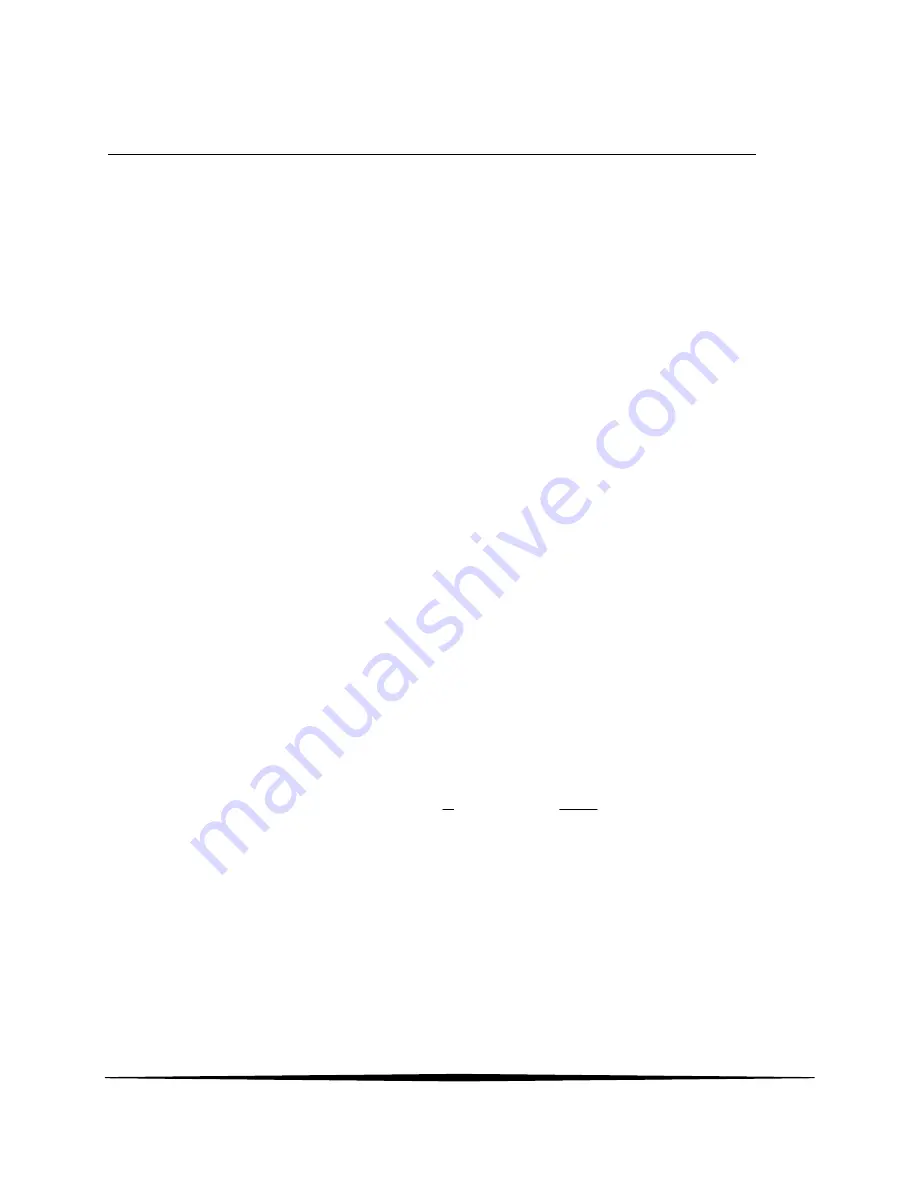
43
O&M Manual
Rev-H (6/17)
Part 8 – PID Controller Details
8.1
PID Description
PID control, like many other control schemes, are used in chemical control to improve the
efficiency of chemical addition or control. By properly tuning the control loop that controls
chemical addition, only the amount of chemical that is truly required is added to the system,
saving money. The savings can be substantial when compared to a system which may be simply
adding chemical at a constant rate to maintain some minimal addition under even the worst case
conditions. The PID output controller is highly advantageous over simple control schemes that
just utilize direct (proportional only) 4-20 mA output connections for control, since the PID
controller can automatically adjust the “rate” of recovery based on the error between the setpoint
and the measured value – which can be a substantial efficiency improvement..
The PID controller is basically designed to provide a “servo” action on the 4-20
mA output to control a process. If the user requires that a measured process stay as close as
possible to a specific setpoint value, the controller output will change from 0% to 100% in an
effort to keep the process at the setpoint. To effect this control, the controller must be used with
properly selected control elements (valves, proper chemicals, etc.) that enable the controller to
add or subtract chemical rapidly enough. This is not only specific to pumps and valves, but also
to line sizes, delays in the system, etc.
This section is included to give a brief description of tuning details for the PID
controller, and is not intended to be an exhaustive analysis of the complexities of PID loop tuning.
Numerous sources are available for specialized methods of tuning that are appropriate for a
specific application.
8.2
PID Algorithm
As most users of PID controllers realize, the terminology for the actual algorithm terms
and even the algorithms themselves can vary between different manufacturers. This is important
to recognize as early as possible, since just plugging in similar values from one controller into
another can result in dramatically different results. There are various basic forms of PID
algorithms that are commonly seen, and the implementation here is the most common version;
The ISA algorithm (commonly referred to as the “ideal” algorithm.)
+
+
=
∫
dt
t
de
D
t
d
t
e
I
t
e
P
output
)
(
)
(
)
(
1
)
(
Where:
output =
controller output
P =
proportional gain
I =
integral gain
D =
derivative gain
t =
time
e(t) =
controller error (e=measured variable – setpoint)
Figure 21 - ISA (Ideal) Equation
The most notable feature of the algorithm is the fact the proportional gain term affects all
components directly (unlike some other algorithms - like the “series” form.) If a pre-existing
controller utilizes the same form of the algorithm shown above, it is likely similar settings can for