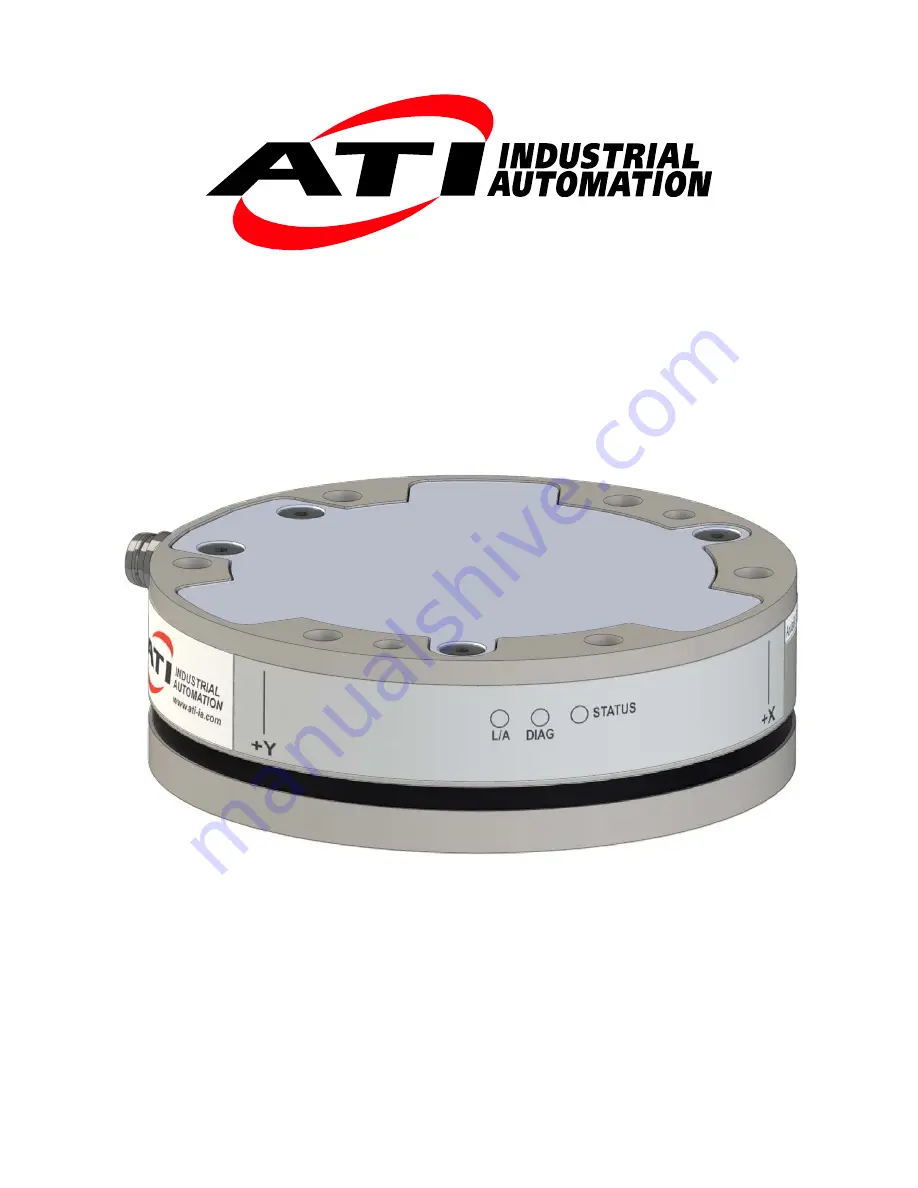
Engineered Products for Robotic Productivity
Pinnacle Park • 1031 Goodworth Drive • Apex, NC 27539 • Tel: +1.919.772.0115 • Fax: +1.919.772.8259 • www.ati-ia.com
Ethernet Axia F/T Sensor
Manual
Document #: 9610-05-Ethernet Axia
Engineered Products for Robotic Productivity
Pinnacle Park • 1031 Goodworth Drive • Apex, NC 27539 • Tel: +1.919.772.0115 • Fax: +1.919.772.8259 • www.ati-ia.com
Ethernet Axia F/T Sensor
Manual
Document #: 9610-05-Ethernet Axia