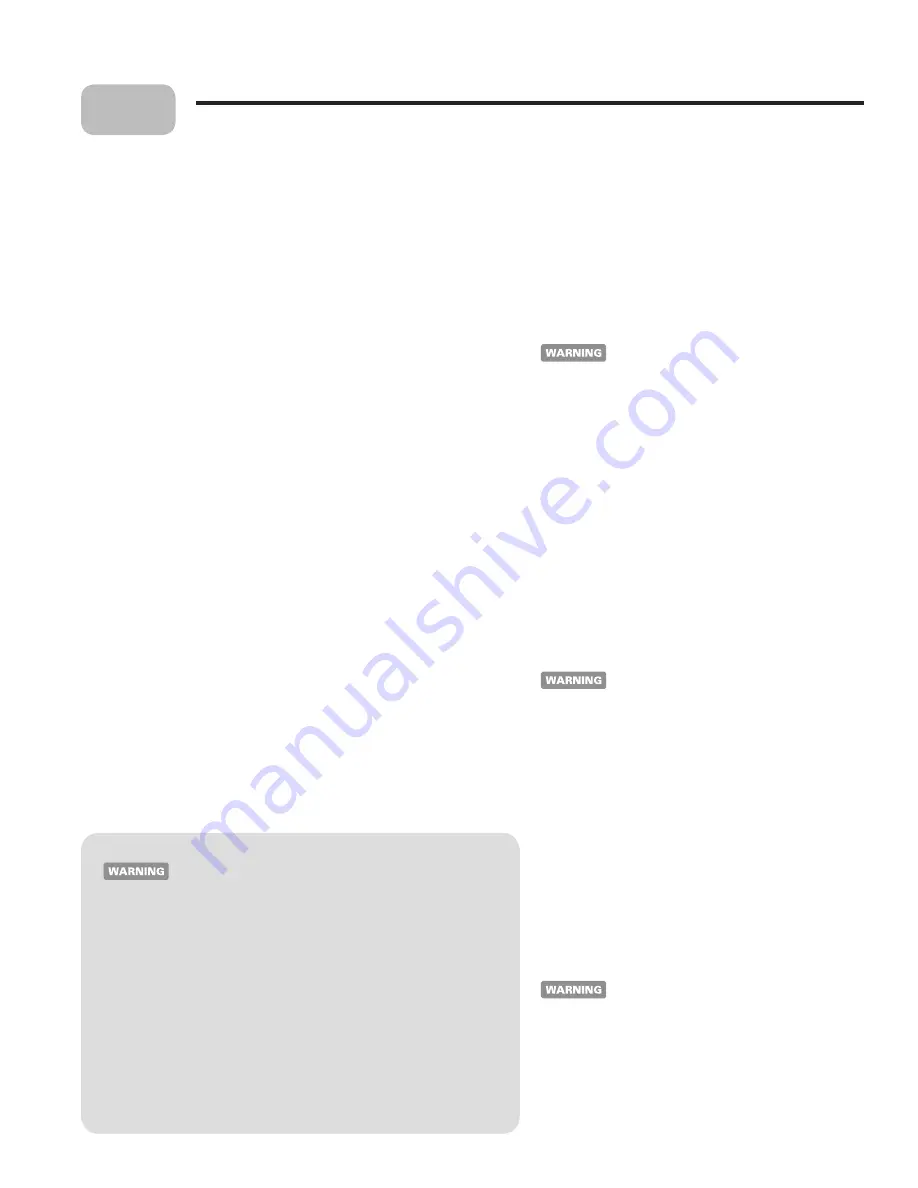
Page 31
KN INSTALLATION AND OPERATION INSTRUCTIONS
Fill and test the system
(continued)
❑
Antifreeze
• Antifreeze for hydronic systems contains propylene glycol and an inhibitor.
Without the inhibitor the glycol is actually corrosive. So the system water must be
checked at least annually to ensure that the inhibitor is at the correct level.
•
Never
use galvanized piping in a system that contains antifreeze. Never use
chromate water treatment. Either of these will react with the inhibitor in the
antifreeze mix.
•
Antifreeze concentration
— If not using a pre-mixed antifreeze solution,
determine the amount of antifreeze to add based on the total volume of the system
piping, the boiler and the expansion tank. Follow the antifreeze manufacturer’s
instructions for the ratio of glycol required for the lowest expected exposure
temperature. NEVER use a glycol mix greater than 50%.
•
Prevent leaks
— Glycol will escape more easily than water through any leak in
the system. So the glycol concentration will reduce if a leak is allowed to continue.
Eliminate all leaks in the system and have the owner frequently inspect the visible
portions of the system for leaks periodically. Do not use circulators or valves with
packing glands, the packing glands can weep.
•
Install a water meter
— Because the system must be installed with automatic
water make-up to ensure pressure will always be at least 12 psig, you should install
a water meter with one half-gallon resolution on the make-up water line. This will
allow monitoring to see if excessive make-up water is entering the system.
•
Circulator sizing
— Glycol/water mixtures do not move heat as well as water
only. The circulator size must be increased to account for this. As a rule of thumb,
increase the flow rate by 15%. Assume a 10% reduction in pressure drop compared
to water only at a give flow rate.
•
Constant circulation
— For areas of the system that will be exposed to low
temperatures, use continuous circulation to keep the water moving in the pipes.
•
Expansion tank sizing
— Increase the expansion tank size about 20% to account
for the effects of the antifreeze.
•
Indirect heat exchangers
— Output from indirect heat exchangers (including
indirect water heaters) can drop substantially when using antifreeze/water. Make
sure the exchanger is sized correctly for the application.
❑
System pressure
• Once the system is cleaned, filled, purged and treated as
required, set the make-up water pressure reducing valve
to the correct cold-fill pressure. This is usually 12 psig for
systems using 30 psig relief valves. For higher pressure
systems, set the cold-fill pressure such that the system
pressure will never exceed about 80% of the boiler relief
valve setting when system water temperature reaches the
maximum operating temperature that the system and boiler
temperature controls will allow.
The pressure in the boiler must never be below
12 psig. Lower pressure could allow localized
boiling in the boiler heat exchanger, causing
possible damage and section failure.
• At cold fill, the water level in closed-type expansion tanks
should not be above center. Use the tank fitting to verify
tank water level is correct.
• As the system heats up, the water will expand, causing the
system pressure to increase. If the expansion tank is properly
sized and installed, the system pressure will never exceed
about 80% of the relief valve set pressure (24 psig for typical
residential systems).
• If the system operating pressure becomes too high, check
the expansion tank to ensure it is large enough. For closed-
type expansion tanks, make sure there are no leaks in the
piping or the tank and the tank fitting is correctly installed.
For diaphragm or bladder-type tanks, you may have to
remove the tank from the system and verify that it can hold
pressure. If it cannot hold pressure, the membrane may be
damaged.
If the system pressure is allowed to rise too high,
the boiler relief valve will open, allowing water to
escape from the system. The resultant addition of
make-up water will cause mineral deposits and
oxygen corrosion in the boiler.
❑
Final checks
• After the system is cleaned, filled and purged, and the system
pressure is correctly set, make sure the water chemistry
is correct. The pH and chemistry must be as required
(and specified by the chemical treatment specialist when
required).
• Make sure all valves are correctly set. Isolation and fill
valves should be open before start-up. Purge valves must be
closed.
• Open the valve on each automatic vent in the system about
one quarter turn to allow venting.
• Thoroughly inspect the system for leaks or weeping valves.
Eliminate all system leaks to prevent excessive
make-up water, which introduces oxygen as well
as lime-forming minerals. This can lead to heat
exchanger damage, resulting in possible severe
personal injury, death or substantial property
damage.
• Watch the boiler pressure/temperature gauge throughout
the start-up process. Make sure the pressure never drops
below 12 psig and never goes higher than 80% of the boiler
relief valve setting pressure.
Use only antifreeze sold for use in hydronic systems
— Never use automotive antifreeze. Automotive antifreeze
and ethylene glycol are toxic to humans and animals and will
damage rubber components in the system.
Make sure the owner is aware that the antifreeze must be
checked periodically by a qualified technician to ensure
the concentration is correct and that the inhibitor level is
adequate.
Obtain the MSDS for the antifreeze and leave a copy with
the owner. Follow antifreeze manufacturer’s guidelines for
application and maintenance.
Failure to follow these guidelines could result in system or
boiler failure, causing possible severe personal injury, death or
substantial property damage.
11