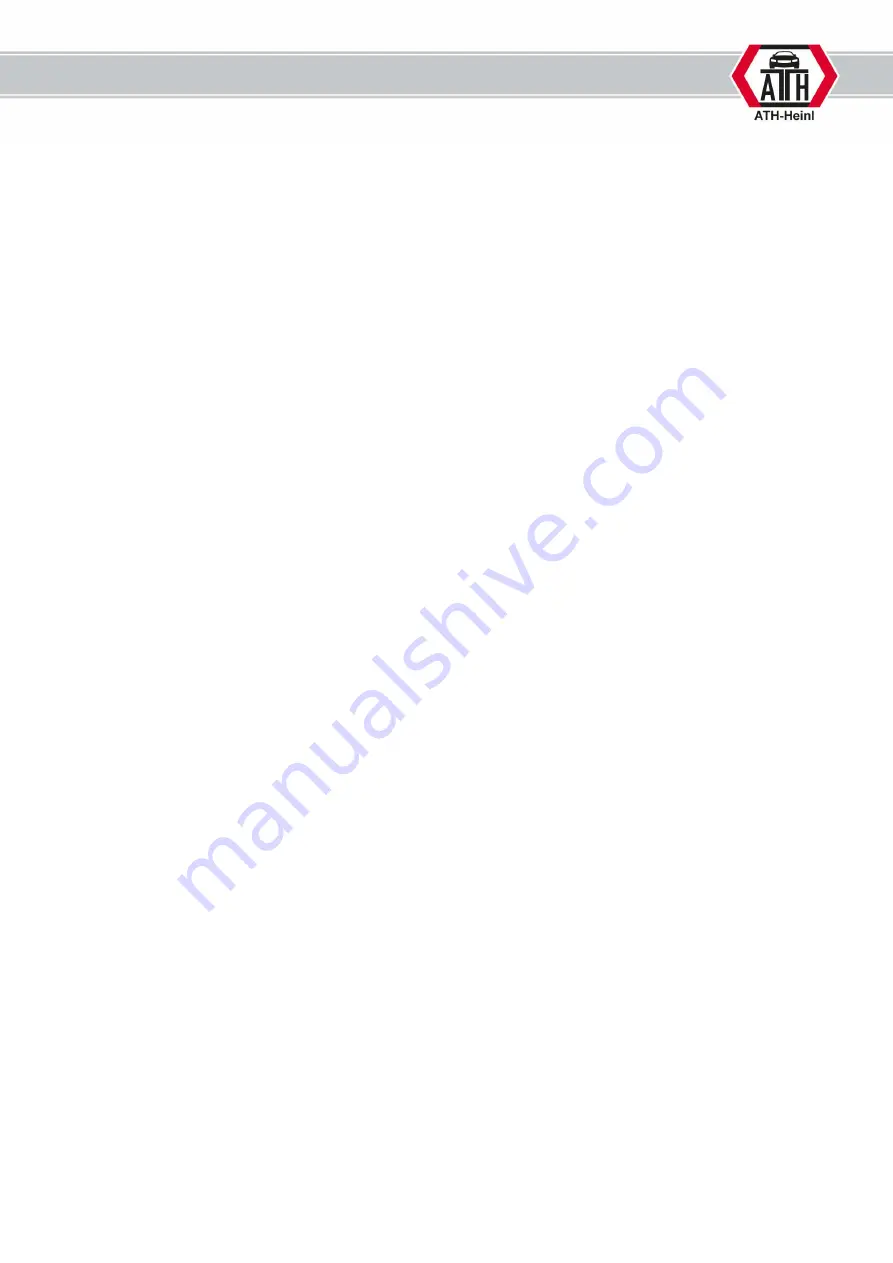
® Copyright ATH-Heinl GmbH & Co. KG, 2019, All rights reserved / Misprints and technical changes reserved / As of: 2019-01
Manufacturer ATH-Heinl GmbH & CO.KG
- 5 -
1.
Lifting columns
The two crossbeams are guided in the lifting columns during raising and lowering.
The lifting columns anchor the lift to the ground.
2.
Hydraulic unit
The hydraulic oil is fed from the tank to the lifting cylinder by a gear pump driven by an electric
motor. The lowering valve allows the oil to flow back into the tank.
P1 Main guide rail
The guide rails bridge the gap between the two crossbeams. They are the parts of the lift onto
which the vehicle is driven. The hydraulic cylinder and the mechanisms required to transmit the
lifting forces (cables, rollers etc.) are fitted under the main guide rail.
P2 Auxiliary guide rail
This has the same design as the main guide rail but does not have any of the hydraulic operating
parts. It is positioned loosely on one side of the crossbeams and can be adjusted according to the
vehicle track width.
3.
Design of the guide rails for the ATH-Four Lift 55
A
The guide rails are also equipped with swing plates at the back and recesses at the front (including
blank plates) for axle measurement rotary plates.
Jacking beam (optional)
This facilitates additional vehicle lifting on the axle or chassis.
The running rails required are provided on the guide rails.
4.
Crossbeams
The crossbeams are the lift supports that connect the opposite pairs of columns. Both access ramps
are attached to these crossbeams.
5.
Control box
The complete electrical control system is located here. All buttons are protected by a front ring in
order to prevent them being pressed accidentally. Furthermore, all movements are immediately
stopped when the buttons are released (dead man’s control).
6.
Roll protection
This device prevents the vehicle from rolling off when it is in the raised position.
7.
CE stop
This device stops the lift descending at a height of 400 mm.
8.
Safety catches
These prevent the raised platform from lowering by more than 100 mm in the event of any defects.
Pneumatic cylinders unlock the device each time it is lowered.
9.
Limit switch
Prevents an unnecessarily high build-up of pressure in the hydraulic circuit.