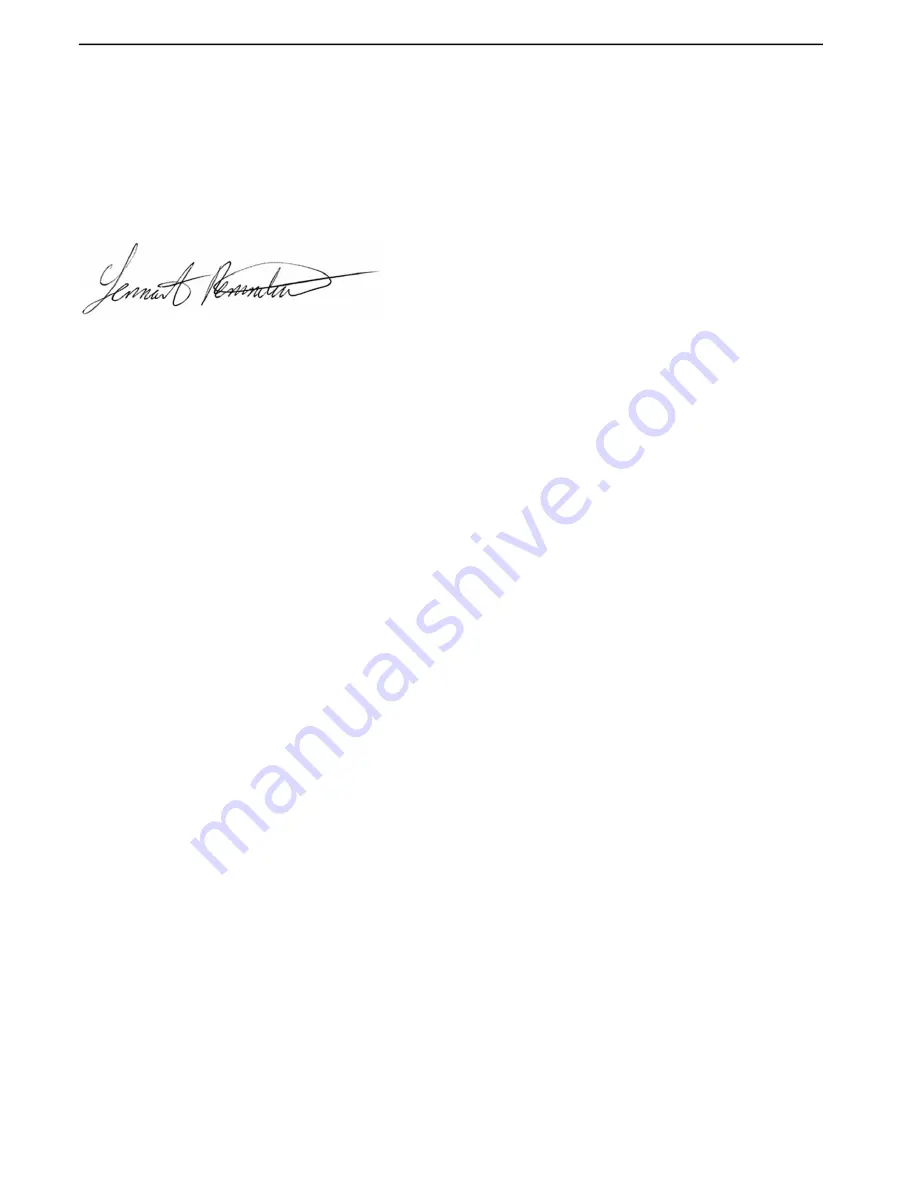
ies, to which this declaration relates is in conformity
with the appropriate standard(s):
EN 792-6, EN 13463-1:2002
and in accordance with the following directive(s):
98/37/EEC, 94/9/EC
Stockholm, October 2006
Lennart Remnebäck, General Manager
Signature of issuer
Installation
Air quality
• For optimum performance and maximum machine
life we recommend the use of compressed air with
a maximum dew point of +10°C. We also recom-
mend the installation of an Atlas Copco refrigera-
tion-type air dryer.
• Use a separate air filter of type Atlas Copco FIL.
This filter removes solid particles larger than 15
microns and also removes more than 90 % of li-
quid water. The filter must be installed as close
as possible to the machine/equipment and prior
to any other air preparation unit such as REG or
DIM (please see Air Line Accessories in our main
catalogue). Blow out the hose before connecting.
Models which need air lubrication:
• The compressed air must contain a small quantity
of oil.
We strongly recommend that you install an Atlas
Copco oil-fog lubricator (DIM). This should be
set according to air consumption by the air line
tool according to the following formula:
L
= Air consumption (litre/s).
(May be found in our sales literature).
D
= Number of drops per min (1 drop = 15 mm3)
L* 0.2 = D
this applies to the use of long work cycle air line
tools. A single point lubricator type Atlas Copco
Dosol can also be used for tools with short running
cycles.
Information about Dosol settings may be found
under Air Line Accessories in our main catalogue.
Lubrication-free models:
• In the case of lubrication-free tools it is up to the
customer to decide on the peripheral equipment
to be used. However, it is no disadvantage if the
compressed air contains a small quantity of oil
e.g. supplied from a fog lubricator (DIM) or Dosol
system.
This does not apply to turbine tools, which should
be kept oil free.
Compressed air connection
• The machine is designed for a working pressure
(e) of 6–7 bar = 600–700 kPa = 87–102 psi.
• Blow out the hose before connecting.
Handling
Tightening torque
The torque obtained depends on air pressure and
tightening time on the actual joint. Extensions and
worn sockets will reduce the delivered torque. The
impact wrench should be used within the specified
torque range. Never use the machine over recommen-
ded maximum torque. Might result in improper
function and faster wear.
Test methods
A static torque measurement is recommended for
impact wrenches.
For test on hydraulic tension tester and for test on
joints.
Maintenance
Service instructions
Overhaul and preventive maintenance is recommen-
ded at regular intervals once per year or after maxim-
um 100.000 tightenings depending on which occurs
sooner. More frequent overhaul may be needed if
the machine is used in heavy-duty operations. If the
machine not is working properly, it should immedi-
ately be taken away for inspection.
The strainer at the air inlet and the exhaust silencer
should be cleaned frequently or replaced in order to
prevent clogging, which decreases the capacity.
At the overhauls, all parts should be cleaned accur-
ately and defective or worn parts (i.e. O-rings, vanes)
should be replaced.
It is important that the machines threaded connec-
tions are tightened properly; i.e. in accordance with
the specifications on the exploded views. Before as-
sembly, lubricate the threads with grease.
A
All o-rings should be greased before assem-
bling.
© Atlas Copco Tools - 9836 3643 00
4
W2315XP-ATEX
Safety and operating instructions
Содержание W2315XP
Страница 11: ......