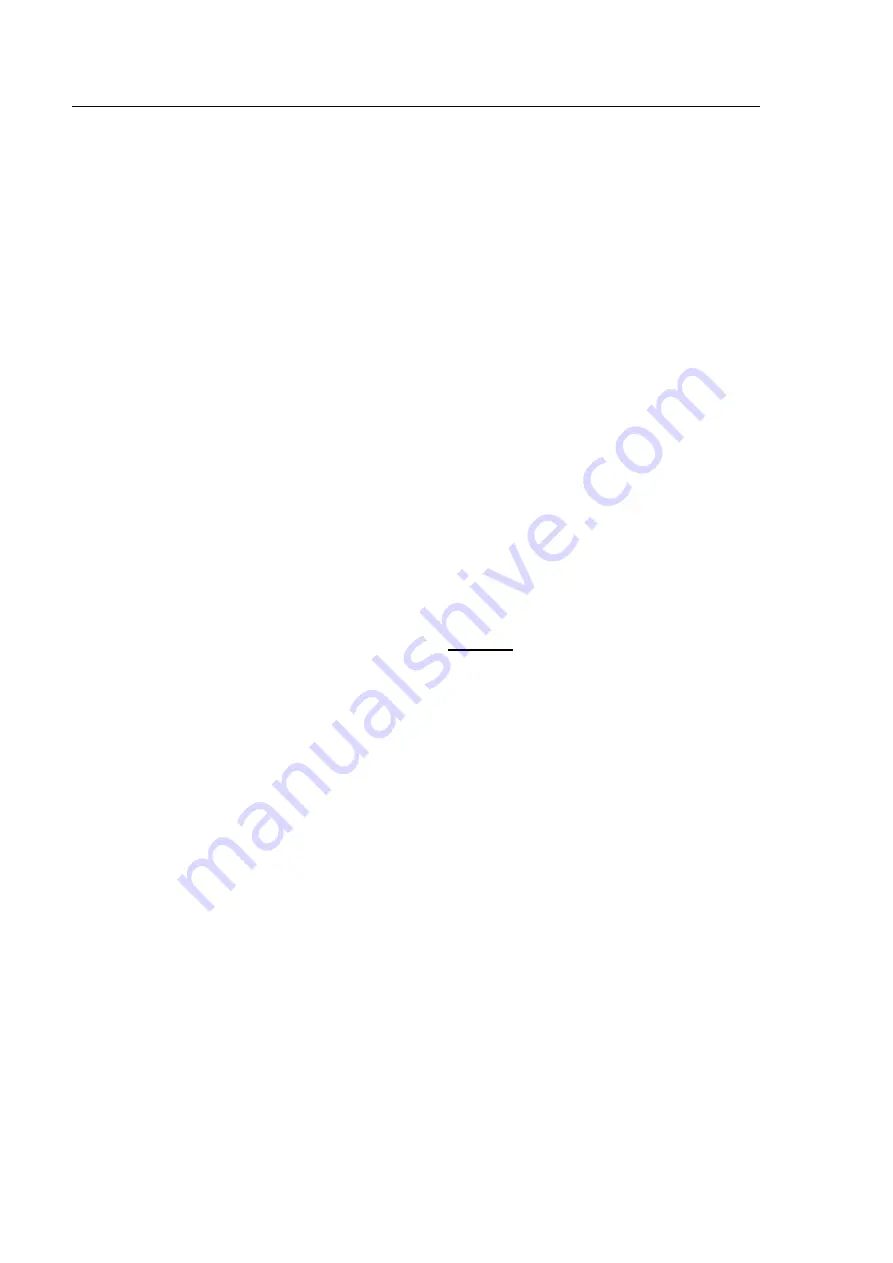
02.06.2022 V1
4. POWER SUPPLY SECTION
It is important to choose the appropriate power supply to make the driver operate
properly
.
Maximum Voltage Input:
The internal power supply can operate from 25Vdc to 110Vdc, including power input
fluctuation and back EMF voltage generated by motor coils during motor shaft
deceleration, or from 18Vac to 80Vac via a transformer.
Higher voltages will damage the driver.
Regulated or unregulated power supply:
Both regulated and unregulated power supplies can be used to supply DC power to the
drive. However, unregulated power supplies are preferred due to their ability to
withstand current surge. If regulated power supply (such as most switching supplies) is
used, it is important to have a large current output rating to avoid problems like current
clamp. For example, using a 4A supply for a 3A motor drive operation. You can use a
power supply of lower current rating than that of the motor (Typically 50%~70% of
motor current). The reason is that the drive draws current from the power supply
capacitor only during the ON duration of the PWM cycle, but not during OFF duration.
Therefore, the average current withdrawn from the power supply is considerably less
than the motor current. For example, two 3A motors can be supplied by one power
supply of 4A rating.
Multiple Drivers:
It is recommended that multiple drives share one power supply to reduce cost,
provided that the supply has enough capacity.
DO NOT
daisy-chain the power supply
input pin of the drivers (connect them to power supply separately) to avoid cross
interference.
Higher supply voltage will allow higher motor speed to be achieved. If the speed
requirement is low, it’s better to use lower supply voltage to improve noise, heating and
reliability.
NEVER
connect power and ground incorrectly, it will damage the driver.
Page 3