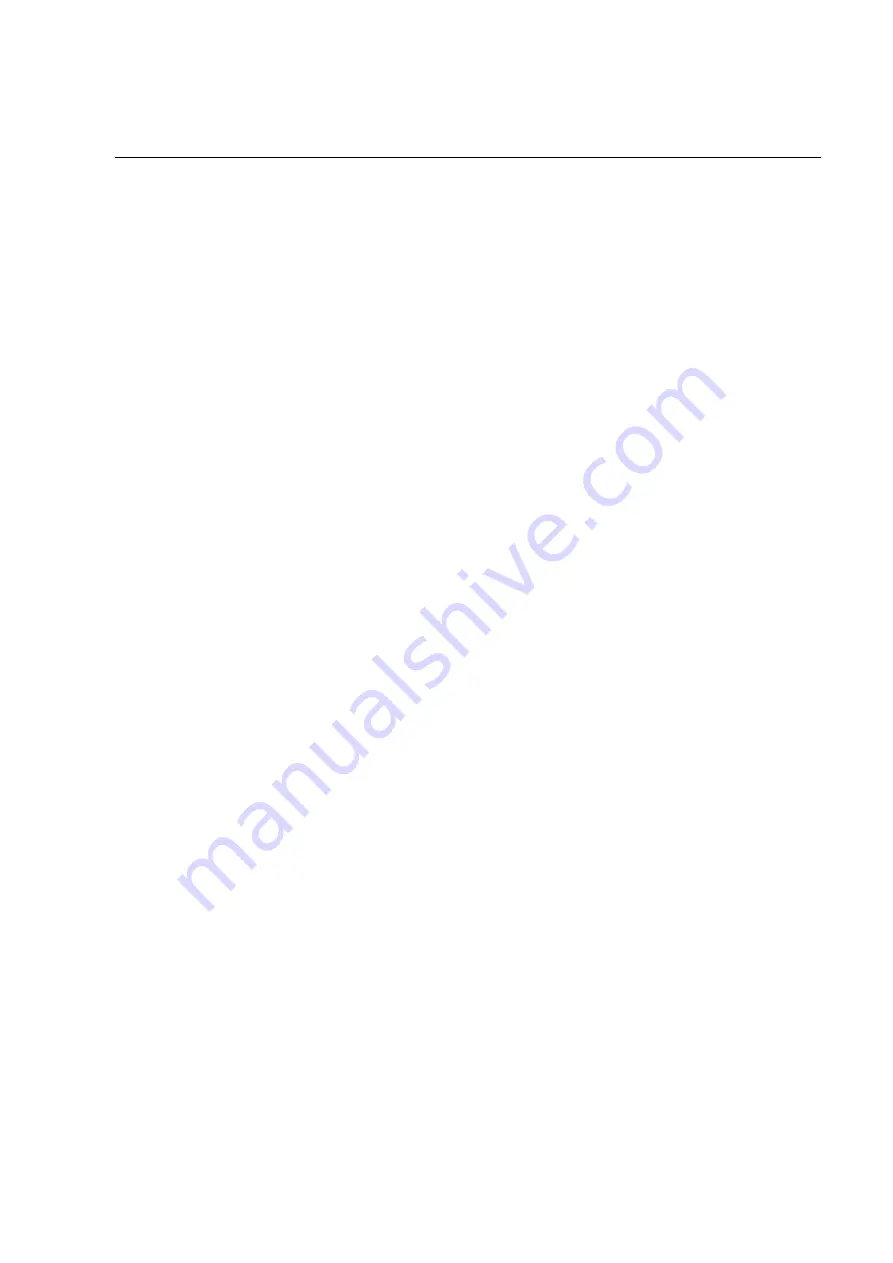
01.03.2020 v3
Table of Contents
Page
General
1
Features of the Driver
1
Applications of the Driver
1
Specifications and Operating Environment
2
Electrical Specifications
2
Operating Environment and Parameters
2
Driver Connectors, P1, P2 and P3
2
Control Signal Connector P1 Pins
2
Power Connector P2 Pins
2
Power Connector P3 Pins
2
Power Supply Selection
3
Maximum Voltage Input
3
Regulated or Unregulated Power Supply
3
Multiple Drivers
3
Driver Voltage and Current Selection
4
Selecting Supply Voltage
4
Setting Proper Output Current
4
Microstep Resolution and Driver Current Output
4
Microstep Resolution Selection
4
Current Setting
4
Driver connection to Motors
5
Driver Dimensions
5