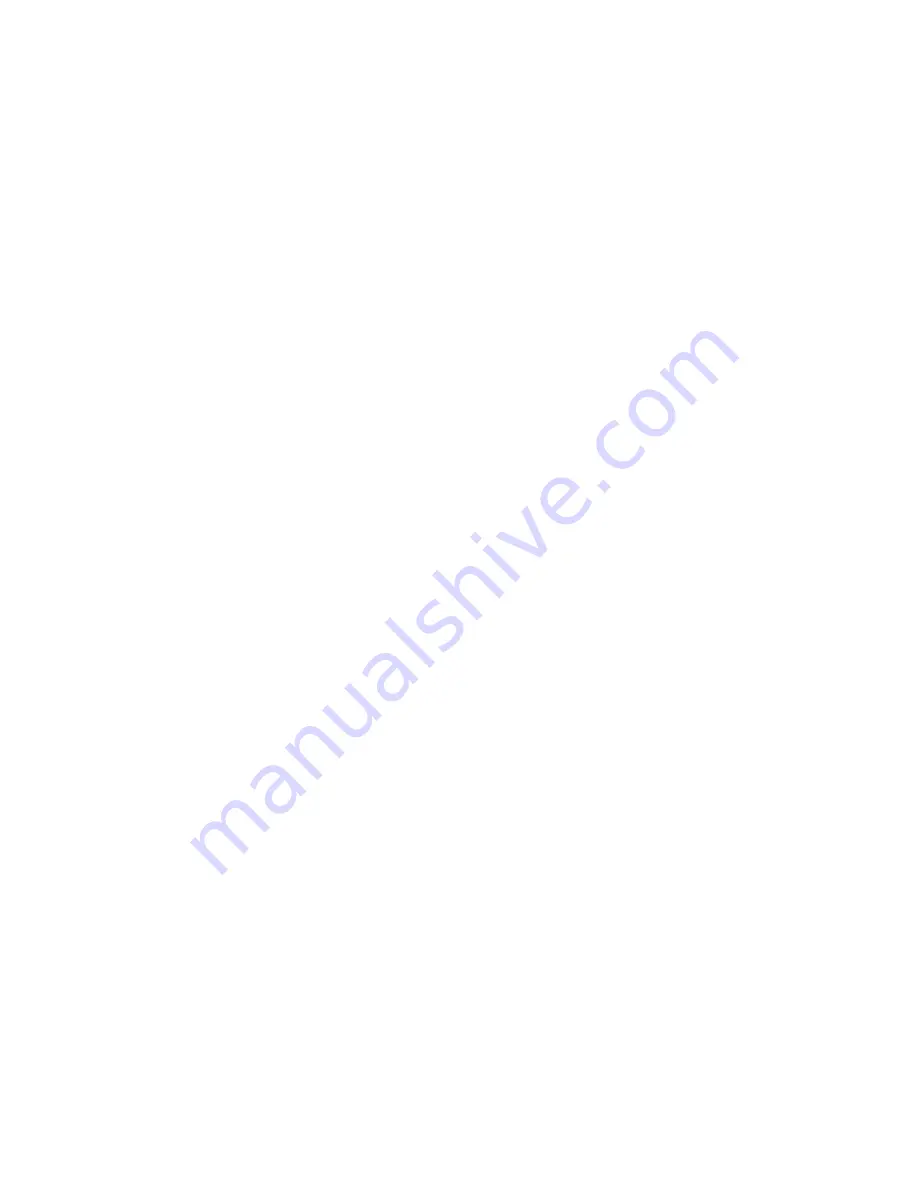
6
DISASSEMBLY/ASSEMBLY INSTRUCTIONS
THROTTLE DISASSEMBLY
–
Remove eductor assembly (31). To remove, unthread upper
section, press in on tabs of lower section and pull assembly
from housing.
–
Remove inlet adapter (9), releasing spring (8) and valve (7).
NOTE: Do not remove seat (6) unless damage is evident.
–
To remove valve stem (2), remove roll pin (4) and lever (3).
THROTTLE ASSEMBLY
–
Coat valve stem (2) with ARO 29665 spindle oil and assemble
into housing with hole in valve stem in line with housing to ac-
cept valve (7).
–
Assemble seat (6) into housing with rounded corners into
housing first.
–
Coat valve (7) with ARO 29665 spindle oil and assemble into
housing, securing valve stem (2).
–
Assemble spring (8) into housing.
–
Assemble inlet adapter (9) to housing, securing throttle com-
ponents.
–
Assemble lever (3) to housing, securing with roll pin (4).
–
Assemble eductor assembly (31) to housing. To assemble, in-
sert tapered section of eductor assembly into housing while
aligning threaded section with housing. Using a wrench on
flats, tighten threaded section securely. Tabs will snap into
slots in housing.
Содержание RS25A–VLK
Страница 7: ...7 NOTES ...
Страница 8: ...PN 49999 500 ...