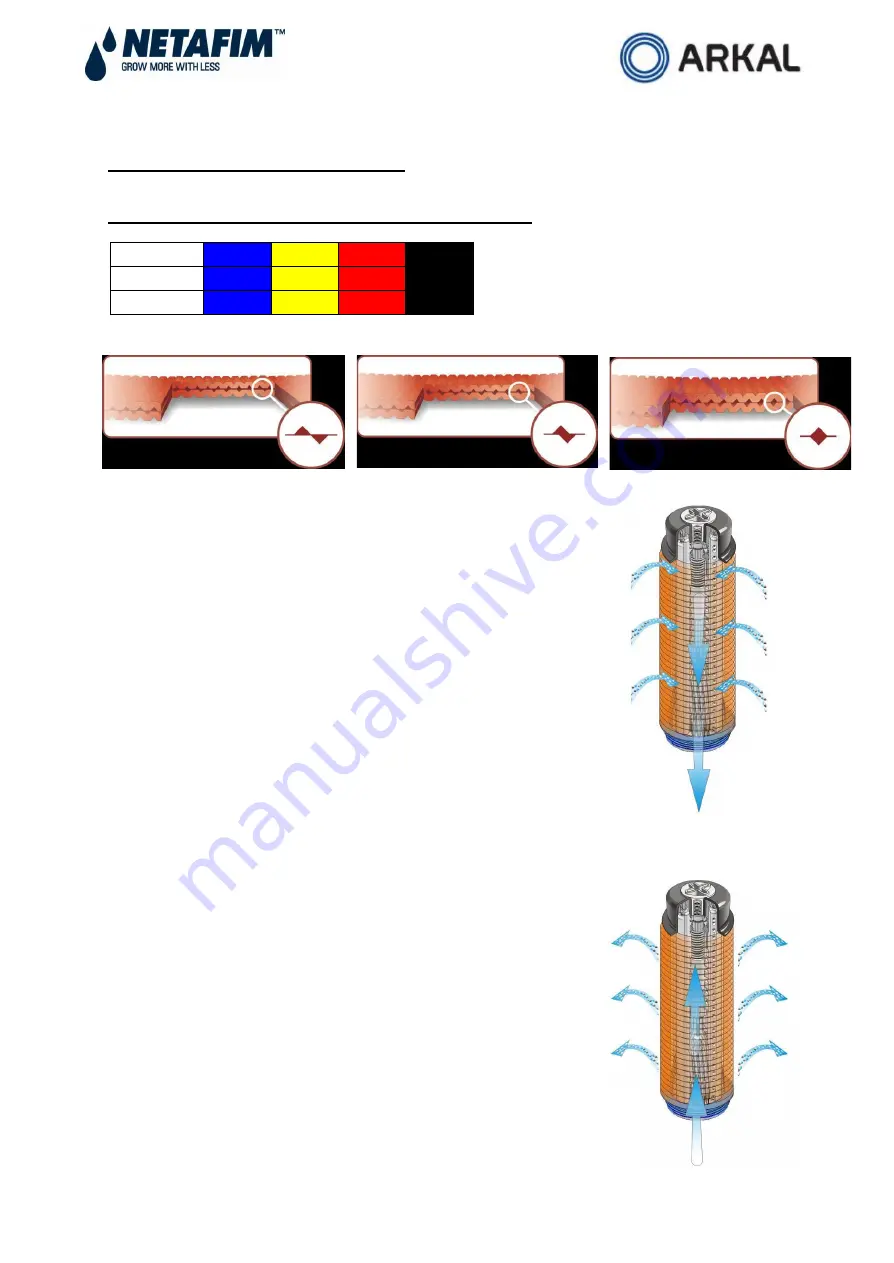
5
3. Description and Operation
Table of Filtration Grades of the Discs and Color Code
Color Code
Blue
Yellow
Red
Black
Mesh
40
80
120
140
Micron
400
200
130
100
Spin Klin Spine - The Core of the Spin Klin Filtration System
The Spin Klin
®
discs are stacked on the Spin Klin
®
spine. The
discs are color-coded according to micron size, and are
assembled to suit your water filtration requirements. The spine
assembly has a spring compression unit and an internal piston,
which operate during alternate filtration or backwash modes. The
spine assembly is specially designed to compress the micron
housing. Inside the housing a spring and the pressure difference
compress the discs tightly during the filtration process, forcing the
water to flow between the grooves and trap the solids.
Spin Klin Automatic Backwash Operation
Activated by a predefined command (differential pressure or
time) alternate units of the Spin Klin
®
system go into backwash
mode. The inlet valve is shut as the drain is automatically opened.
During the backwash process, the compression spring is
released and the pressure difference is eliminated. The spine
piston rises up, releasing the pressure on the discs. Tangential
jets of clean water are pumped at high pressure in the opposite
direction through nozzles at the center of the spine. The discs
spin free and clear, loosening the trapped solids. Solids are
quickly and efficiently flushed out through the drain.