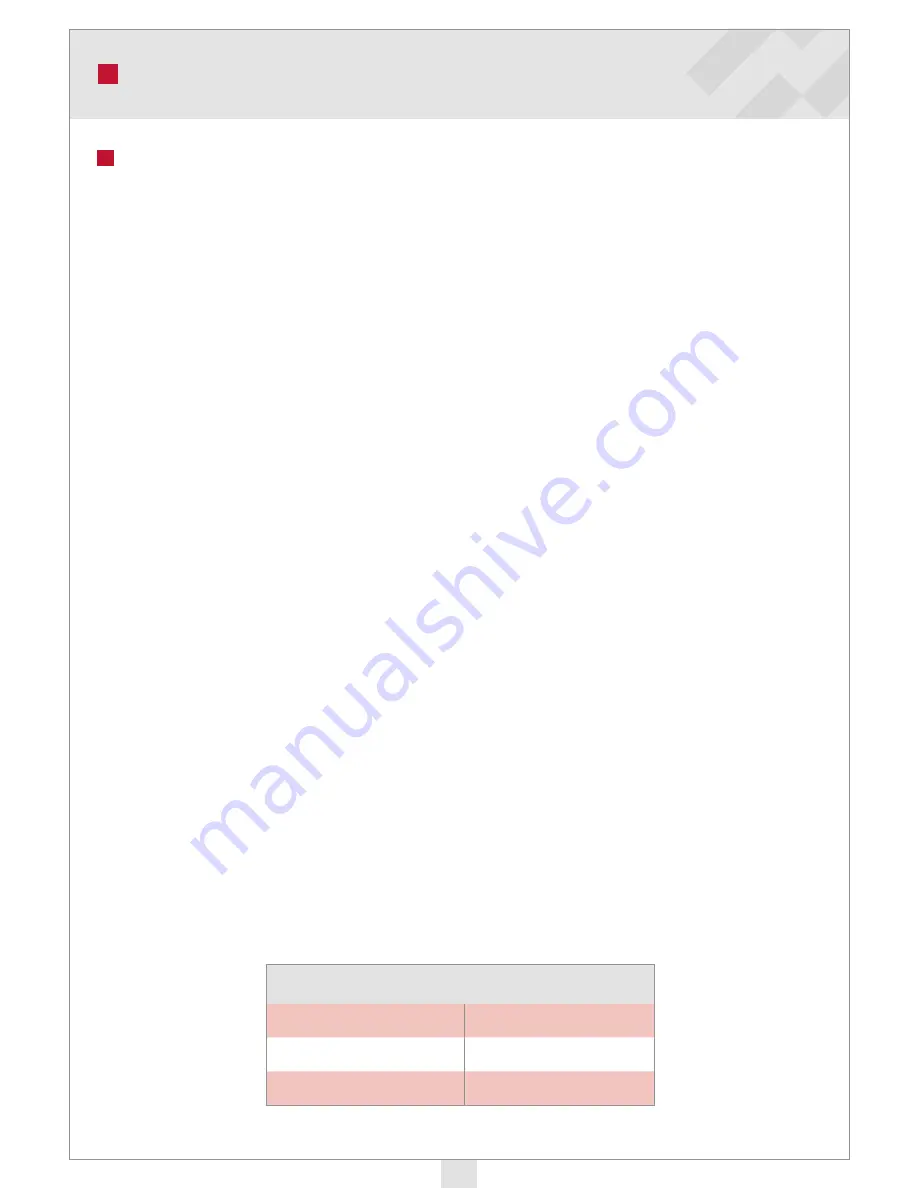
16
INTRODUCTION INTO USE
INTRODUCTION INTO USE
Operational testing
The operation of the equipment is tested before use as follows:
Start the motors (augers and fans) one at a time and check the following:
•
directions of rotation of the augers
•
operation and direction of rotation of the combustion air fans and flue gas extractor
•
countermanding of fuel augers
•
pump operation
•
check the direction of rotation of the pump of the power unit
•
operation of moving grate
Check the safety equipment
•
Adjust the tripping temperature of the burn back thermostat to a level low enough to set
off an alarm.
•
Turn the thermostat of the AVTA valve so that it trips and check that the nozzles are
open. Please note that this may create a large volume of water, and we recommend that you
direct it into a separate receptacle.
•
Adjust the tripping temperature of the pulse-controlled burn back thermostat to a level low
enough that it trips.
•
If necessary, carefully heat the sensors.
•
Check the over-heat protection, boil-dry protector and other connected safety equipment.
•
Check the alarm function and that a remote alarm is set off, if it has been connected
Read the operating instructions for the automatic control system before starting the system!
Adjustment
The burner and boiler should be run slowly up to operating temperature in order to minimise
the heat stress on the structures. Automatic control should be shut off and a suitably low power
level selected while the temperature is rising (about 1 hour).
Once the burner and boiler have been warmed up, the burner must be adjusted for clean and
economic operation. An experienced burner operator can adjust the burner visually. The flame
must be pale yellow and combustion must be even. Precise adjustment, however, requires the
use of a flue gas analyser and this is recommended.
The excessive movement of fuel in the grate can be reduced by restricting the movement of the
grate. If ash sticks to the grate, increase its movement.
Target values for combustion
Oxygen (O2)
7-9%
Carbon monoxide (CO)
100-400 ppm, chip
Carbon monoxide (CO)
50-200 ppm, pellet
Содержание Multijet 500
Страница 1: ...INSTALLATION OPERATION AND MAINTENANCE Multijet 500 1500 hydraulic ...
Страница 25: ...25 HYDRAULIC DIAGRAM HTR Hydraulics Oy Multijet 500 1000 kW ...
Страница 26: ...26 HTR Hydraulics Oy Multijet 1500 kW HYDRAULIC DIAGRAM ...
Страница 38: ...38 DECLARATION OF COMFORMITY ...
Страница 40: ...NOTES 40 ...
Страница 41: ...41 NOTES ...
Страница 42: ...42 NOTES ...
Страница 43: ...43 NOTES ...