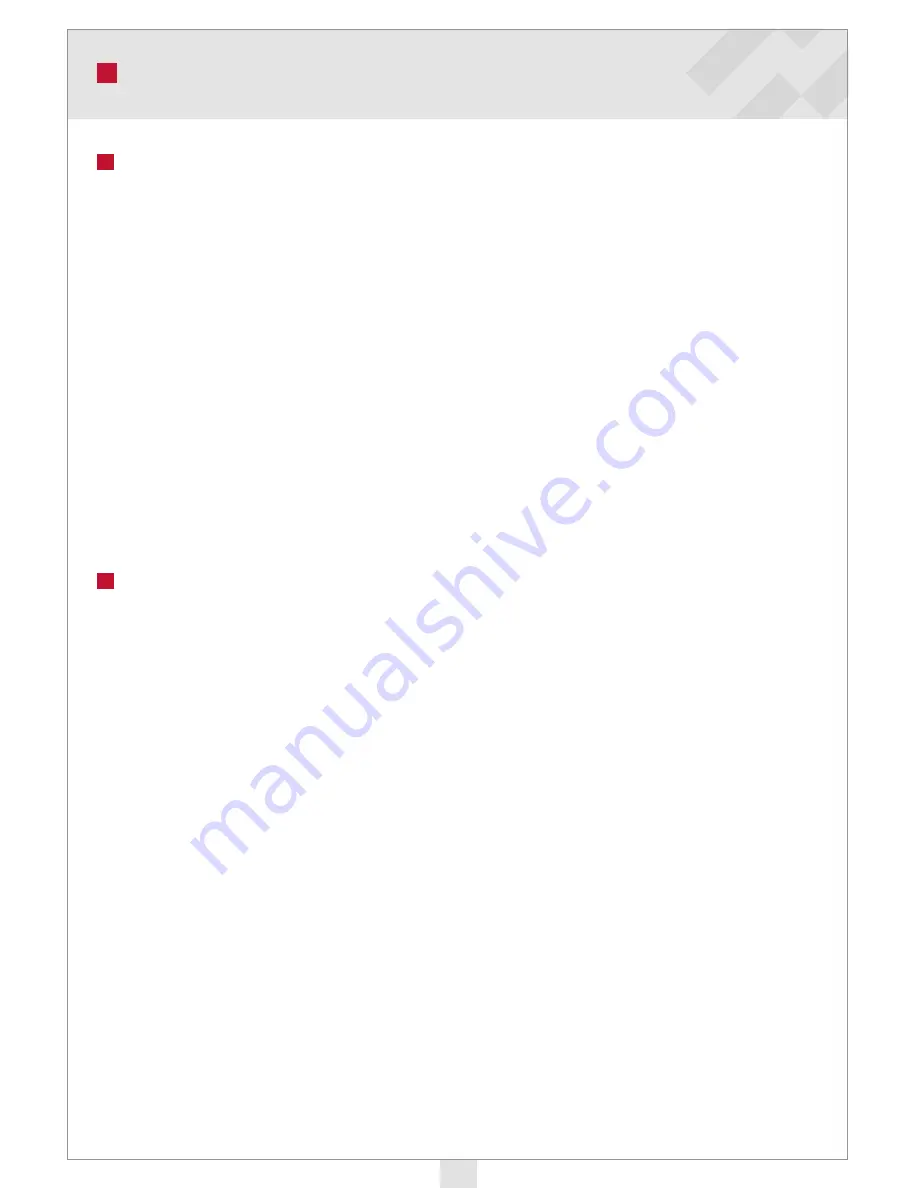
13
INSTALLATION
Powder extinguishing system
•
The powder extinguishing system consists of a bottle (+ spare bottle), a valve, extinguishing
hoses and a red plastic sensor pipe.
•
Install the 3 hoses of the system between the powder extinguisher, auger pipe and
intermediate tank units.
•
Install the red sensor pipe in the powder extinguisher unit and tighten it. Install the other
end of the pipe under the visor located on the auger pipe surface (see figure).
•
PLEASE NOTE! Open the extinguishing bottle slowly and in several stages to ensure the
even distribution of the sensor pipe gas pressure and prevent the content of the bottle from
being discharged by accident.
•
When heated, the pipe melts and breaks. This releases the pressure that keeps the
extinguishing bottle valve closed. The sensor pipe can be used again after cutting off the
melted part. Install the sealing plug again.
•
PLEASE NOTE! The powder extinguishing system is an accessory. When using pellets
as fuel, it is recommended to replace the water extinguishing system with a powder
extinguishing system.
•
Install the red hose filled with gas so that, when overheated, it melts and discharges the
powder extinguishing device. The powder penetrates into the burner auger and puts out
the fire.
•
The bottles must be replaced and refilled during factory maintenance.
Installation of safety systems guarding against burn back
The Ariterm bio-burner must be equipped with an extinguishing system to prevent burn back.
To ensure safe use of the equipment, it is important to install all extinguishing systems before
the equipment is started.
If the burner has two feed augers (MJ700-1500), separate safety equipment must be installed in
both feed augers.
The extinguishing systems are as follows (a-d):
a. Connecting the AVTA safety valve to the water supply system
(wood chip-burning
systems)
•
The Danfoss AVTA15 (50–+90 °C) thermostat valve (1) is connected to the burner auger
pipe and intermediate tank. The valve sensor is manually pushed above the sensor pocket
(2) (see picture), and the valve is connected to the water supply system. In order to avoid
possible network pressure loss, you can fit an expansion tank (4) equipped with a non-
return valve and a pressure warning gauge (PIA).
•
Through manual override, the water can be sprayed into the fuel system manually.
•
The AVTA valve must be adjusted to about 80 °C (on scale no. 4).
Please pay attention to the installation instructions for the valve sensor!
•
The burn back thermostat sensor and AVTA valve sensor are each installed in their own
sensor pocket on the surface of the auger pipe. Please note that the sensors must be tight
against the auger pipe housing. If necessary, use heat-conducting material or screws. The
screws must not, however, damage the sensor! The burn back thermostat is connected to
the burner’s automation system. The AVTA operates on water pressure.
Содержание Multijet 500
Страница 1: ...INSTALLATION OPERATION AND MAINTENANCE Multijet 500 1500 hydraulic ...
Страница 25: ...25 HYDRAULIC DIAGRAM HTR Hydraulics Oy Multijet 500 1000 kW ...
Страница 26: ...26 HTR Hydraulics Oy Multijet 1500 kW HYDRAULIC DIAGRAM ...
Страница 38: ...38 DECLARATION OF COMFORMITY ...
Страница 40: ...NOTES 40 ...
Страница 41: ...41 NOTES ...
Страница 42: ...42 NOTES ...
Страница 43: ...43 NOTES ...