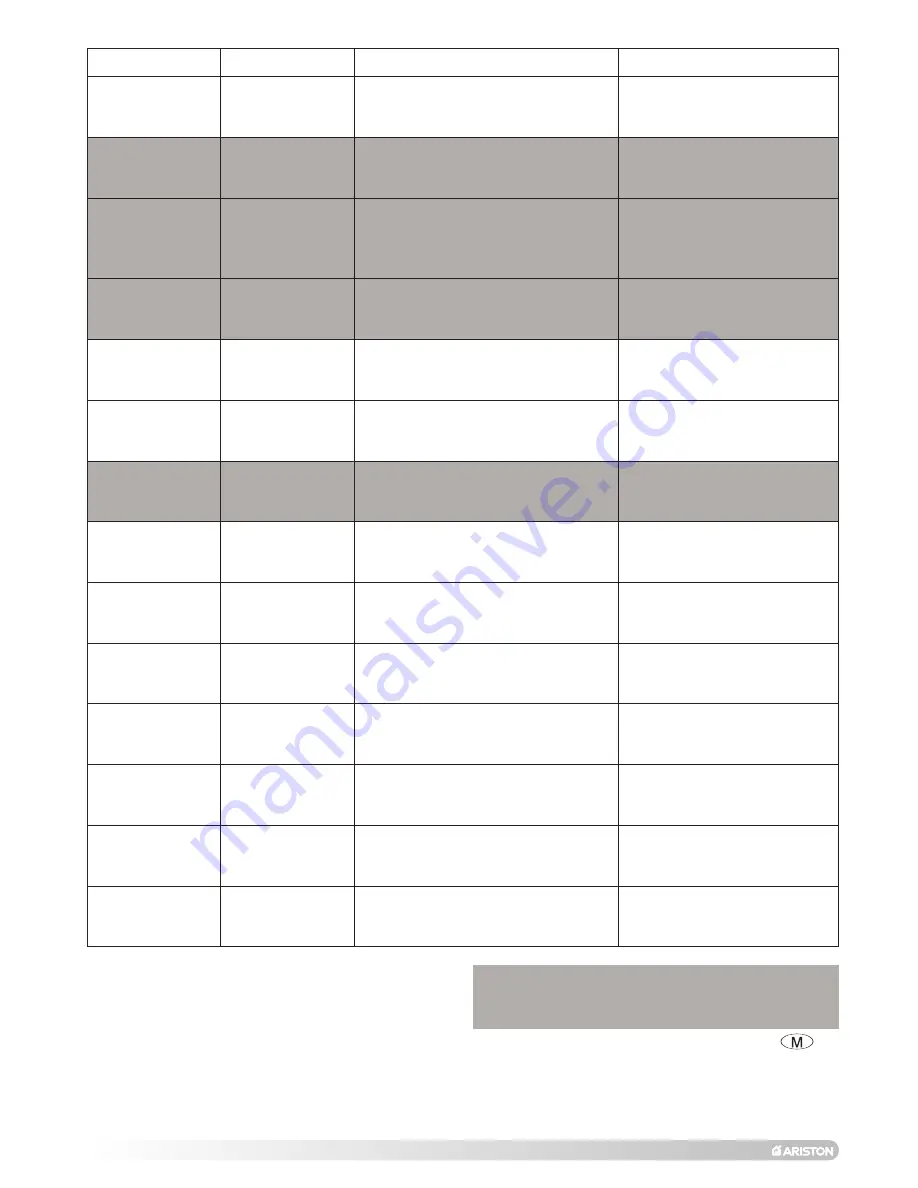
28
Important!!
The parameters P5, P6 and P9 are only enabled when
the outdoor sensor is connected.
To return to the normal display, press the menu button .
left-hand display
right-hand display
Function
factory setting
rr
from
0
00
0
to
0
01
1
selects low temperature systems
or std systems
0
01
1
p
p
from
9
90
0
to
9
91
1
Temperature regulation controlled by
external sensor
9
90
0
p
p6
6
from
-
-2
20
0
to
+
+2
20
0
Correction of heat curve translation
P
P5
5
from
0
0_
_3
3
to
3
3_
_0
0
Curve incline
tt
Test Function
A
A
8
81
1
Bus Address (Do not modify)
bb00
Set-point second heating zone
bb11
GSM value
bb
2
20
0
NOT USED
bb
30
NOT USED
bb
4
40
0
NOT USED
bb
5
50
0
NOT USED
bb
6
60
0
NOT USED
bb
7
70
0
NOT USED
Содержание 47-116-09
Страница 48: ...63 ...