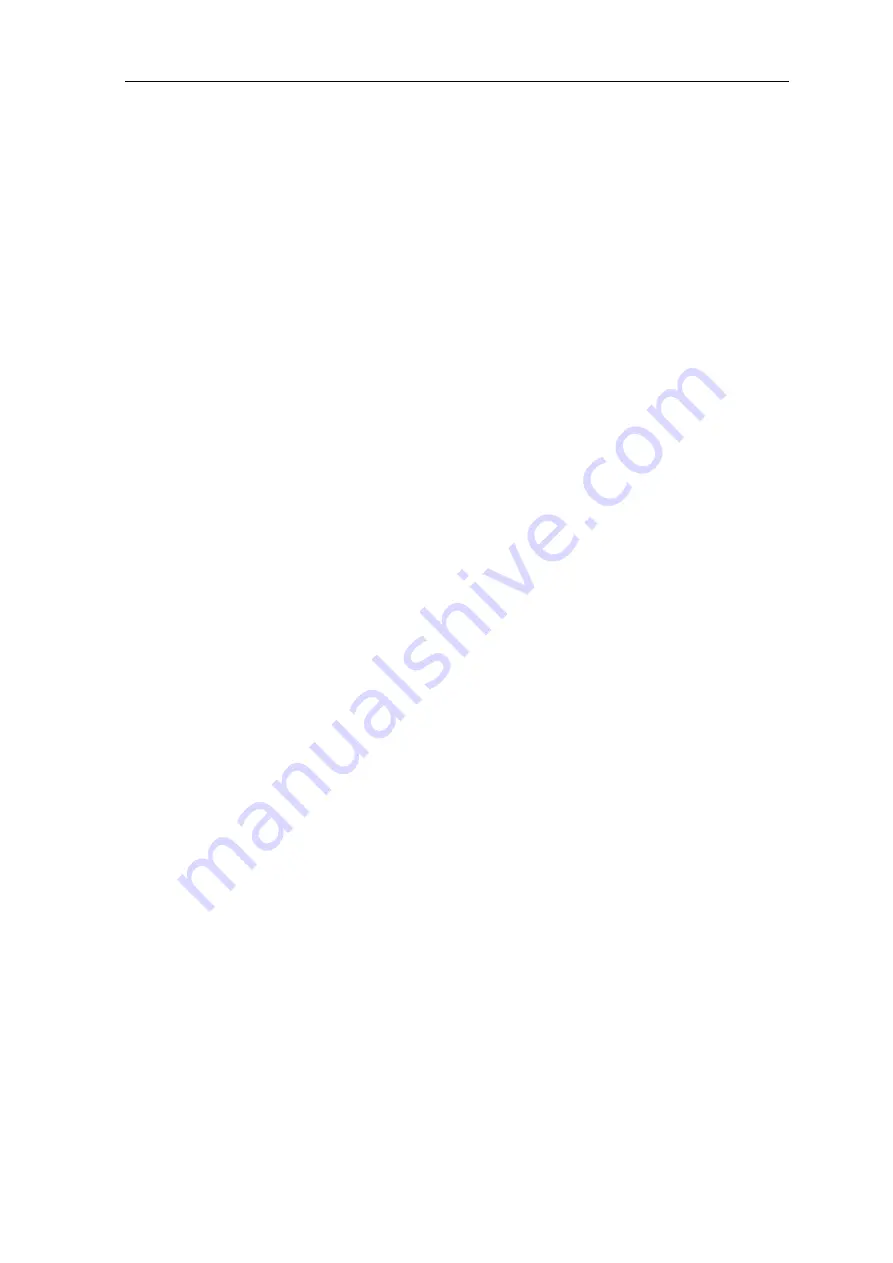
SUMMARY
10
2 SUMMARY
2.1 Brief Introduction
Arcomig 250C welding machine utilizes the latest pulse width modulation (PWM) technology and
insulated gate bipolar transistor (IGBT) power module, which can replace large transformer type welders.
Inverters are portable, small, lightweight, with low power low consumption. This machine performs four
welding processes, such as MIG, MMA, AC TIG and DC TIG.
Characteristics
:
★
The ZVS soft switch technology reduces the IGBT switching loss.
★
The machine uses Power Factor Correction, which increases the electrical
efficiency of the machine.
★
The machine comes complete with protection safeguards such as
overvoltage, over-current, over-heating and so on. Those functions
obviously improve the stability and security of the welding machine.
★
The panel combines two kinds of control modes, making it easy for user to
operate.
★
MCU control system responds immediately to any changes.
The ArcoMig 250C is suitable for all positions welding for various plates made of stainless steel,
carbon steel, alloyed steel, titanium, magnesium, cuprum, etc, which is also applied to pipe installment,
mould mend, petrochemical, architecture decoration, car repair, bicycle, handicraft and common
manufacture.
Содержание ArcoMiG LCD 250C
Страница 1: ...I ...
Страница 3: ...CONTENT III ...
Страница 34: ...MAINTENANCE TROUBLESHOOTING 34 5 3 Electrical principle drawing ...
Страница 38: ...MAINTENANCE TROUBLESHOOTING 38 ...