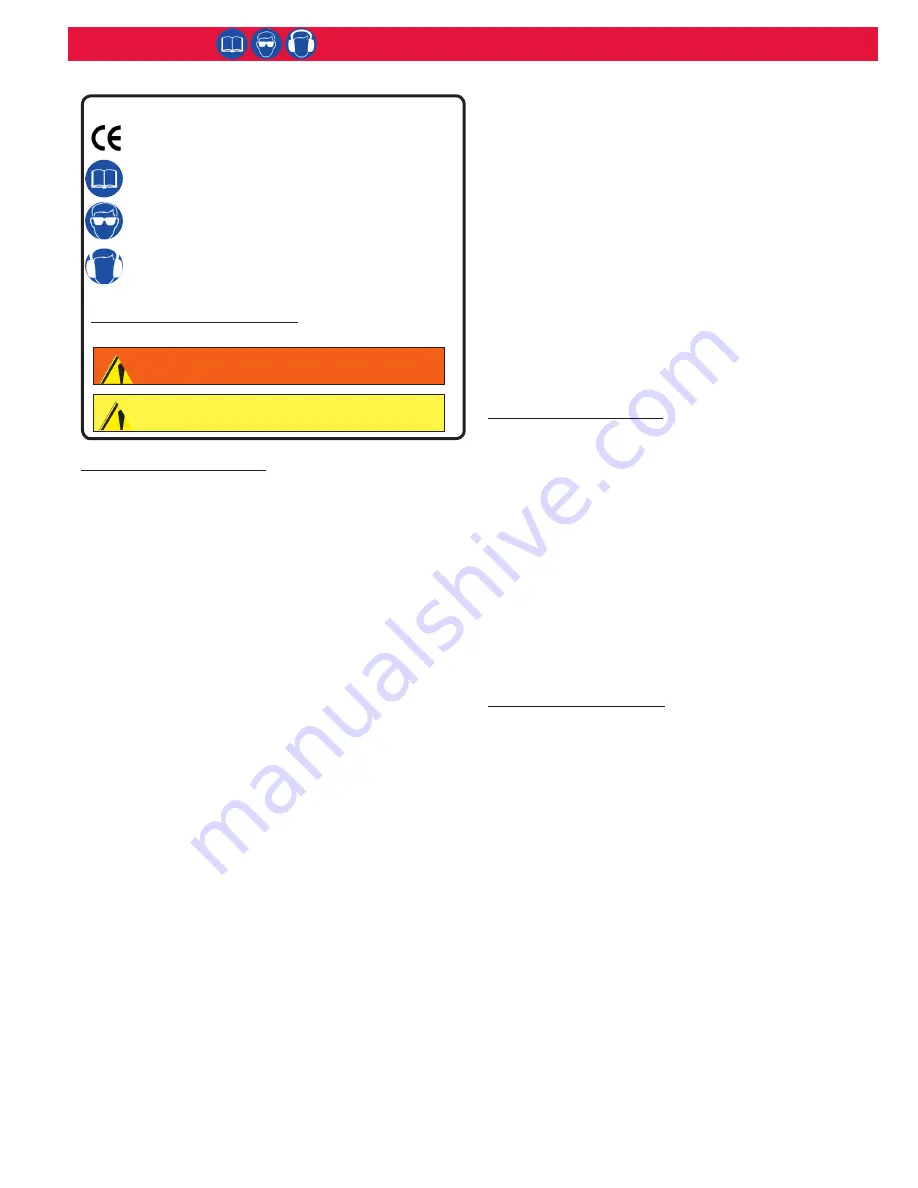
3
ERT_S series Ebbert Rivet Tools (HK1038
)
I. GENERAL SAFETY RULES:
1. A half-hour long hands-on training session with qualified
personnel is recommended before using Huck equipment.
2. Huck equipment must be maintained in a safe working
condition at all times. Tools and hoses should be inspected
at the beginning of each shift/day for damage or wear. Any
repair should be done by a qualified repairman trained on
Huck procedures.
3. For multiple hazards, read and understand the safety
instructions before installing, operating, repairing, maintaining,
changing accessories on, or working near the assembly power
tool. Failure to do so can result in serious bodily injury.
4. Only qualified and trained operators should install, adjust or
use the assembly power tool.
5. Do not modify this assembly power tool. This can reduce
effectiveness of safety measures and increase operator risk.
6. Do not discard safety instructions; give them to the operator.
7. Do not use assembly power tool if it has been damaged.
8. Tools shall be inspected periodically to verify all ratings
and markings required, and listed in the manual, are legibly
marked on the tool. The employer/operator shall contact
the manufacturer to obtain replacement marking labels
when necessary. Refer to assembly drawing and parts list for
replacement.
9. Tool is only to be used as stated in this manual. Any other use
is prohibited.
10. Read MSDS Specifications before servicing the tool. MSDS
specifications are available from the product manufacturer
or your Huck representative.
11. Only genuine Huck parts shall be used for replacements or
spares. Use of any other parts can result in tooling damage
or personal injury.
12. Never remove any safety guards or pintail deflectors.
13. Never install a fastener in free air. Personal injury from
fastener ejecting may occur.
14. Where applicable, always clear spent pintail out of nose
assembly before installing the next fastener.
15. Check clearance between trigger and work piece to ensure
there is no pinch point when tool is activated. Remote
triggers are available for hydraulic tooling if pinch point is
unavoidable.
16. Do not abuse tool by dropping or using it as a hammer. Never
use hydraulic or air lines as a handle or to bend or pry the
tool. Reasonable care of installation tools by operators is an
important factor in maintaining tool efficiency, eliminating
downtime, and preventing an accident which may cause
severe personal injury.
17. Never place hands between nose assembly and work piece.
Keep hands clear from front of tool.
18. Tools with ejector rods should never be cycled without nose
assembly installed.
19. When two piece lock bolts are being used always make sure
the collar orientation is correct. See fastener data sheet for
correct positioning.
II. PROJECTILE HAZARDS:
1. Risk of whipping compressed air hose if tool is pneudraulic
or pneumatic.
2. Disconnect the assembly power tool from energy source
when changing inserted tools or accessories.
3. Be aware that failure of the workpiece, accessories, or the
inserted tool itself can generate high velocity projectiles.
4. Always wear impact resistant eye protection during tool
operation. The grade of protection required should be
assessed for each use.
5. The risk of others should also be assessed at this time.
6. Ensure that the workpiece is securely fixed.
7. Check that the means of protection from ejection of fastener
or pintail is in place and operative.
8. There is possibility of forcible ejection of pintails or spent
mandrels from front of tool.
III. OPERATING HAZARDS:
1. Use of tool can expose the operator’s hands to hazards
including: crushing, impacts, cuts, abrasions and heat. Wear
suitable gloves to protect hands.
2. Operators and maintenance personnel shall be physically able
to handle the bulk, weight and power of the tool.
3. Hold the tool correctly and be ready to counteract normal or
sudden movements with both hands available.
4. Maintain a balanced body position and secure footing.
5. Release trigger or stop start device in case of interruption of
energy supply.
6. Use only fluids and lubricants recommended by the
manufacturer.
7. Avoid unsuitable postures, as it is likely for these not to allow
counteracting of normal or unexpected tool movement.
8. If the assembly power tool is fixed to a suspension device,
make sure that fixation is secure.
9. Beware of the risk of crushing or pinching if nose equipment
is not fitted.
Continued on next page...
GLOSSARY OF TERMS AND SYMBOLS:
- Product complies with requirements set forth by
the relevant European directives.
- Read manual prior to using this equipment.
- Eye protection is required while using this
equipment.
- Hearing protection is required while using this
equipment.
Notes: are reminders of required procedures.
Bold, Italic type, and underline:
emphasize a specific
instruction.
WARNINGS: Must be understood to avoid
severe personal injury.
CAUTIONS: Show conditions that will damage
equipment or structure.
Safety Instructions
Содержание ERT1S
Страница 2: ...2 ERT_S series Ebbert Rivet Tools HK1038 ...