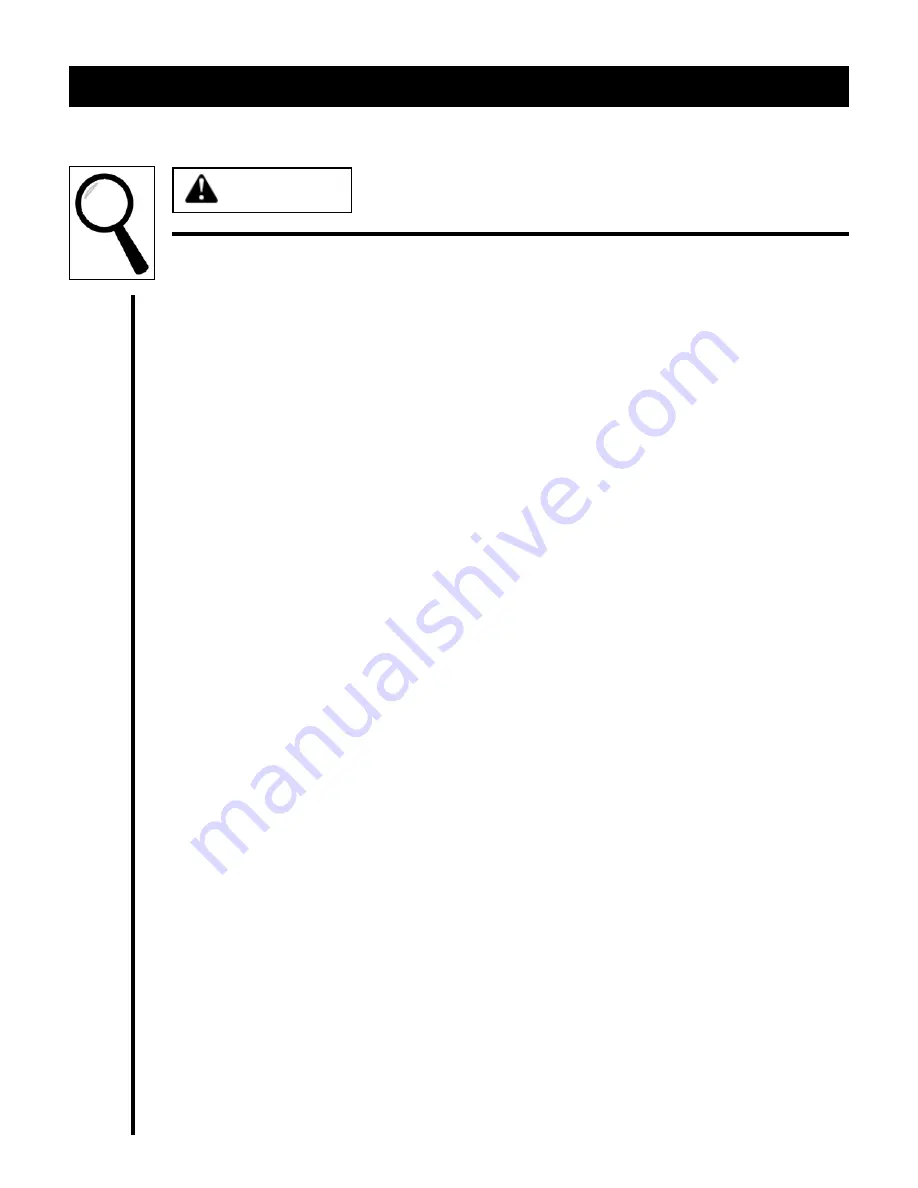
15
1. Fan Does Not Operate
A.)
Check voltage requirements on unit and electrical supply. Check for live receptacle, plug,
power line and toggle switch.
B.)
Look for any loose connections inside the main motor's junction box.
2. Unusual Noise
Squealing at start-up or during operation may be caused by the motor shaft's bearing seal.
Spray with lubricant at the front of the motor where the shaft exits the motor's frame.
3. No Fog
A.)
If the flowmeter is closed, turn the flow control knob counter-clockwise to increase
fogging output. Visually check for sediment clogs within the flowmeter's body and remove
inline strainer's cap to flush any debris from screen. Refer to the maintenance section for
flowmeter cleaning instructions.
B.)
If the fan is automated and the water is supplied through a water solenoid, check to see
if the solenoid is electrically activated by the control and check the solenoid for clogs.
C.)
If after checking both the flowmeter and solenoid, you still do not have any fog, begin a
process of elimination starting with the water source. Disconnect and reconnect your
plumbing before and after each device to check for any obstructions.
4. Poor Quality Fog
A.)
The liquid feed tube (Part #575) may not be properly positioned. The feed tube is located
behind the blade assembly and should be inserted approximately 1/4" into the slot
between the motor shaft and the stainless steel face plate. Centered in the slot area and
aimed slightly downward, free from any rotational contact.
B.)
Liquid not traveling through the fan blades. This can be diagnosed by viewing the back
of a blade assembly during operation (using a bright flashlight). If system is clogged,
liquid can be seen spinning out of the slot area between the motor shaft and stainless
steel face plate (Part #573). If confirmed, replace fan blade assembly (Part #571-assy).
Cleaning the internal passageways of a blade assembly is feasible with the aid of some
speciality tools.
5. Fog Slowly Decreases
If fog output gradually decreases over time, sediment is slowly clogging the flowmeter's
needle valve. Try operating at a higher output or cleaning the inline strainer (Part #71). If the
problem persists, a smaller size flowmeter may be required. Flowmeters perform best when
set half way up the scale or higher.
t
roublesHootinG
BEFORE INSPECTION AND /OR SERVICE,
DISCONNECT AND LOCK OUT POWER SOURCE.
WARNING