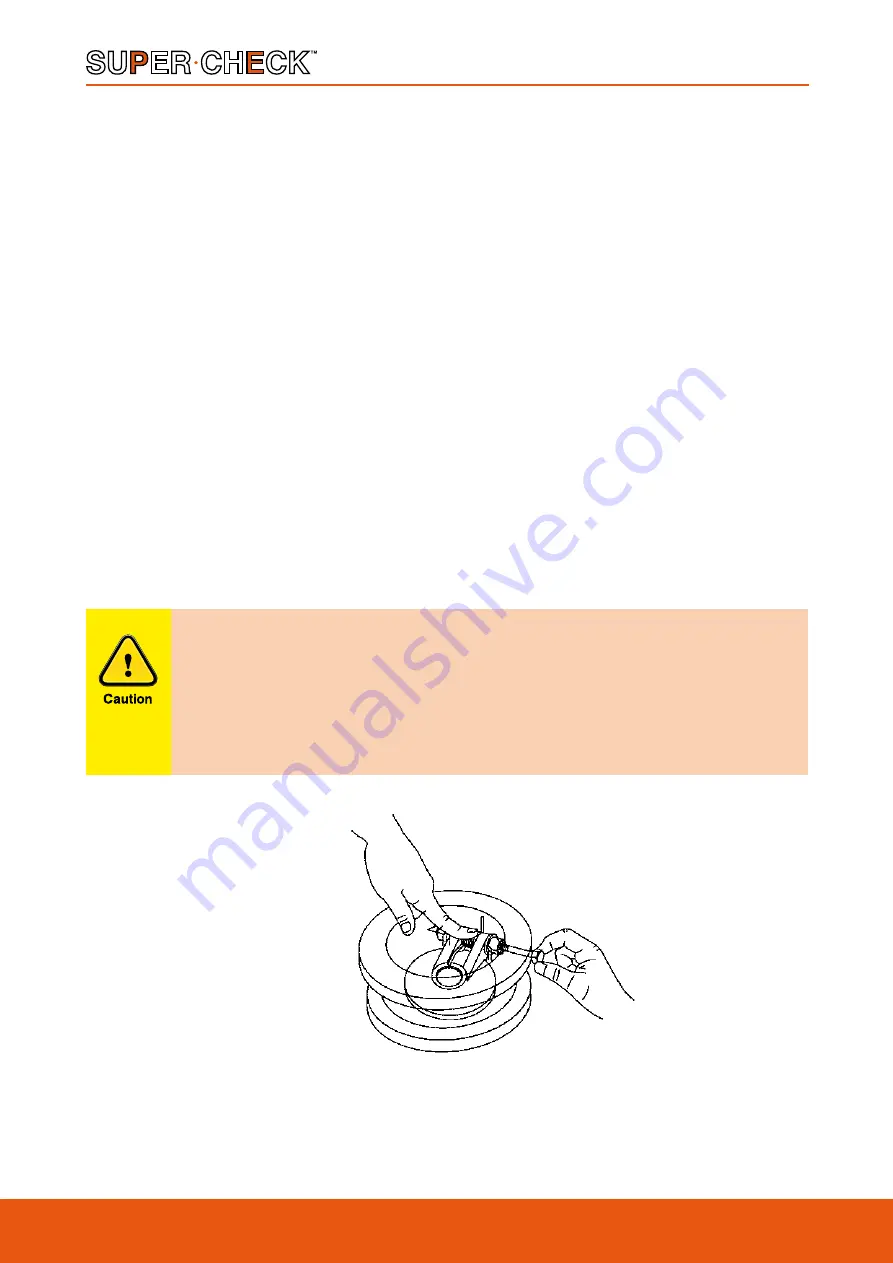
WAFER PATTERN CHECK VALVES - ‘SLP’ & ‘SW’ STYLE
Australian Pipeline Valve - Installation, Operation and Maintenance Manual
10
Important see Diagram 5 and caution note below about guarding the spring during disassembly to
prevent eye damage. Refer to exploded view in Appendix.
5.4 ASSEMBLY SLP SERIES
a) Lay the body (1) down, with ‘downstream’ side of the body facing upward. Lay disc (2) inside the body
(1). Slide hinge pin (3) into the body through the bushings (6) (where fitted) the spring (5) and disc (2).
Refer paragraph b) below on energising spring into the body. Reinsert disc into body cavity with shaft
holes inline with side shaft port. Slide shaft into the body through shaft bearing on one side. Continue
sliding shaft through disc, disc spring and remaining bushing. Check the disc (2) and bushings for end
play. If body plate is severely worn it should be replaced.
b) Wind the spring (5) 180° in a clockwise direction. Place the wound spring (5) in position between the
disc hinge lugs ensuring the long convex side of the spring’s leg is against the disc, the other end must
be energised against the wall of the valve as per the Diagram 4. Different sizes and classes may have
different spring configurations. While maintaining pressure on the spring (5), insert the hinge pin (3)
into the body (1) passing it through the bushings (6) (where required), disc (2) and spring (5) as detailed
above in paragraph a).
c) Teflon tape the threads of the hinge pin retainer, and screw the hinge pin retainers (8) into the body (1).
After repair, the valve should be retested as per API 598 or applicable standard.
DIAGRAM 5
For SLP and SW series: under no circumstances wind springs to gain a higher or
lower torsional load. Special high and low torque springs are available for this
purpose. Before attempting shaft extraction, be sure to press hand over the disc
spring (see Diagram 5). Failure to do this may result in personal injury due to the
spring “launching” itself unexpectedly once the shaft is pulled free of it. Always
wear protective eyewear.