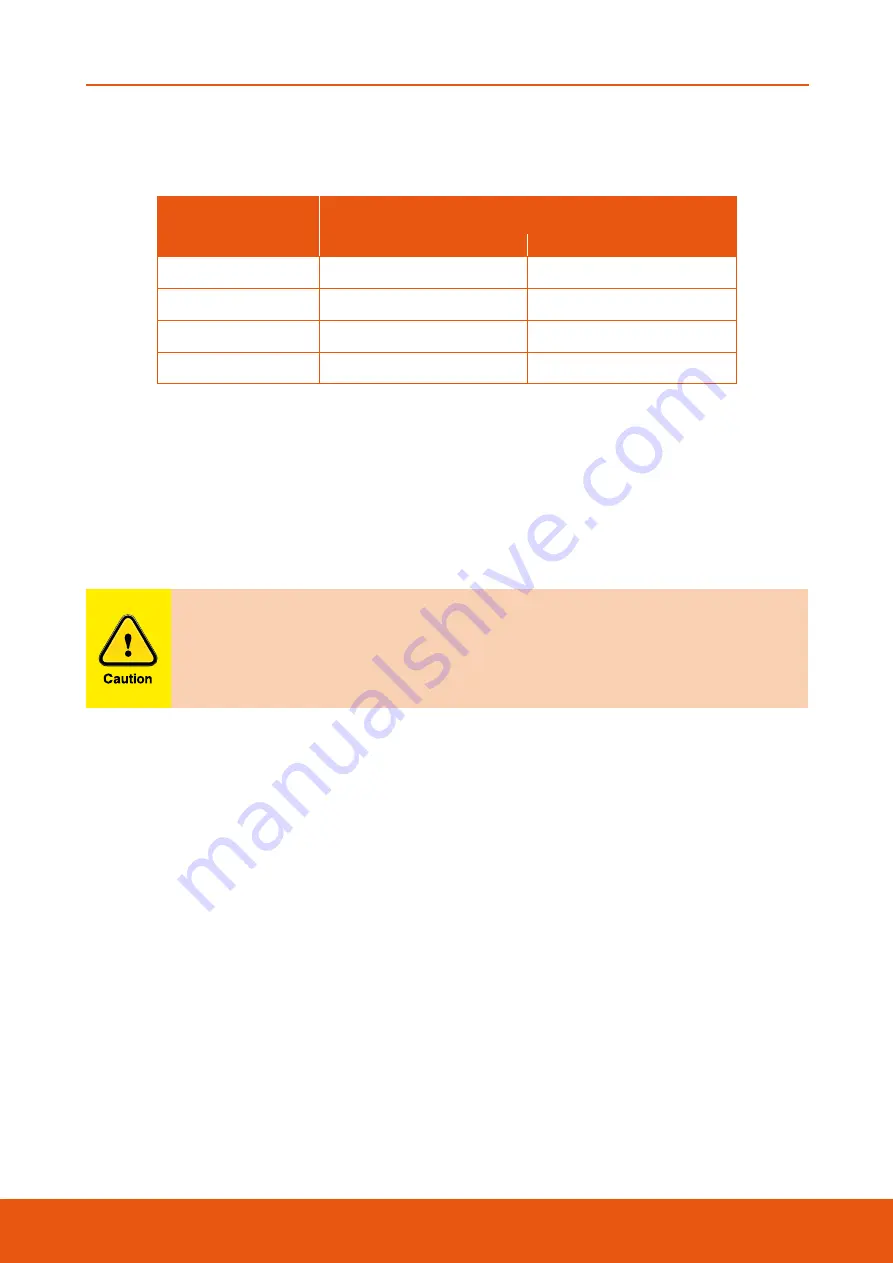
LUBRICATED PLUG VALVES - SAPM/SAPL
Australian Pipeline Valve - Installation, Operation and Maintenance Manual
18
TABLE 3
Frequency of lubrication using operation frequency as a guide
FREQUENCY OF VALVE
USE
FREQUENCY OF SEALANT INJECTION FOR A VALVE IN
STANDARD SERVICE
NO MORE THAN
NO LESS THAN
10-100 times a day
Daily
Weekly
1-10 times a day
Weekly
Monthly
1-30 times a month
Monthly
Quarterly
Several times a year
Quarterly
Biannually
The choice of lubricant should be in accordance with the process medium and the service temperature
range (see lubrication Table 2 & 3 above).
It is recommended that the valve be periodically stroked (at least partially) to ensure valve functions, and
will aid to prevent seizure/galvanisation on any mating surfaces (or in the case of resilient seats).
Duration depends on service, criticality, etc.
There are different types of lubricants available depending on temperature and service. Special lubricants
for worn or corroded valves are available as well as flushing agents to remove old grease.
Use extreme caution when injecting sealant into a valve in the closed position with
a non compacting fluid in the valve.
B) CONFIRM SUSPECTED STEM LEAKAGE
The following methods can indicate stem leakage.
a) Gas services - applying a detergent solution around the stem area will produce soap bubbles if
the stem is leaking. A bad leak may be heard as a hissing noise from the stem area.
b) Liquid services - stem leak on a liquid service will be visible as liquid flowing out from
where the stem protrudes from the body.
c) Gear operated valves - the area where the stem protrudes from the body is hidden by the gear
operator. Confirm stem leak by observing or applying a detergent solution around relief valve
(where fitted) in the gear operator indicator plate, and the gear operator to the valve body
mounting area.
d) Portable electronic hydrocarbon detectors - some are sensitive enough to detect stem leaks by
placing the probe adjacent to the stem.
If a hexagon socket/headed screw bottoms out inside the stem packing, and the stem is still leaking, then
more stem packing compound needs to be loaded into the stem packing. This is done by removing the hex
socket/headed screw and putting a new piece of stem packing compound into the injector unit and
energising it with the hexagon socket/headed screw.