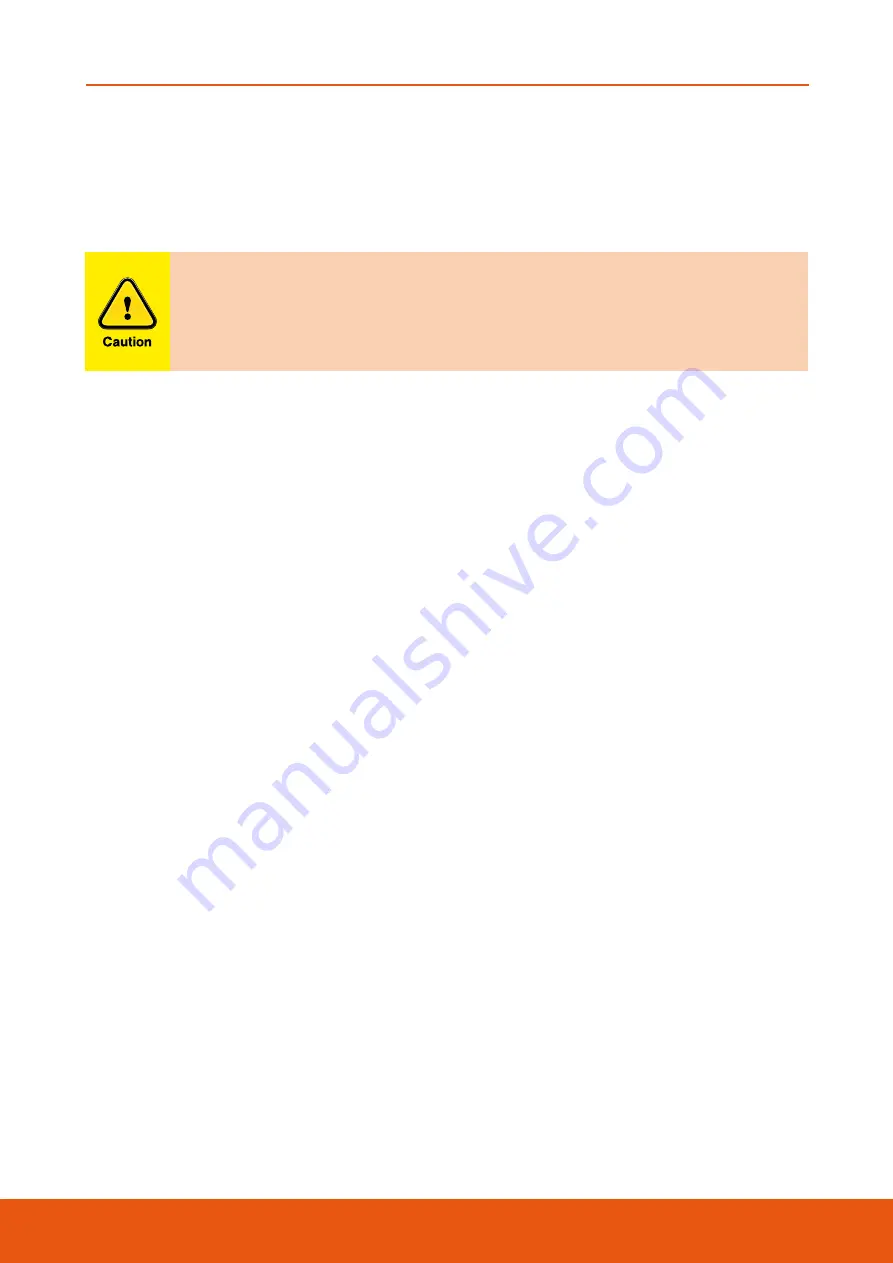
LUBRICATED PLUG VALVES - SAPM/SAPL
Australian Pipeline Valve - Installation, Operation and Maintenance Manual
12
3.2 INSTALLATION POSITIONS
Plug valves are usually bidirectional, and therefore may be installed in either direction. In some cases,
plug valves may be unidirectional, in which case the direction of flow will be indicated on the valve body.
Piping should be properly aligned and supported to reduce mechanical loading on
the end connections.
3.3 PREPARATION FOR INSTALLATION
Before installation ensure all protective packaging is removed.
To ensure tight shut off it is recommended that additional sealant be injected prior to operation and
re-test. Any excess sealant found around the plug port should be removed using a scraper. End
connections should be cleaned to remove any unwanted paint or rust inhibitor. Significant problems can
become apparent with any valve installed in an unclean pipeline. Ensure that the pipeline has been
flushed free of dirt and debris before installation. The working environment should also be clean and
clear of any debris which could contaminate the valve. During cleaning ensure the valve is in the fully
opened or fully closed position. Water and inert gas such as carbon dioxide and nitrogen are unlikely to
affect the sealant. It is recommended that valves be re injected with sealant after completion of cleaning
when the use of solvents or steam cleaning are involved.
• Remove protective end caps or plugs and inspect valve ends for damage to threads, socket weld bores
or flange faces.
• Thoroughly clean adjacent piping system to remove any foreign material that could cause damage to
seating surfaces during valve operation.
• Verify that the space available for installation is adequate to allow the valve to be installed and to be
operated.
3.4 END CONNECTIONS
3.4.1 Threaded Ends
Check condition of threads on mating pipe.
Apply joint compound to the male end of joint only. This will prevent compound from entering the valve
flow path.
3.4.2 Flanged Ends
Check to see that mating flanges are dimensionally compatible with the flanges on the valve body ensure
sealing surfaces are free of debris.