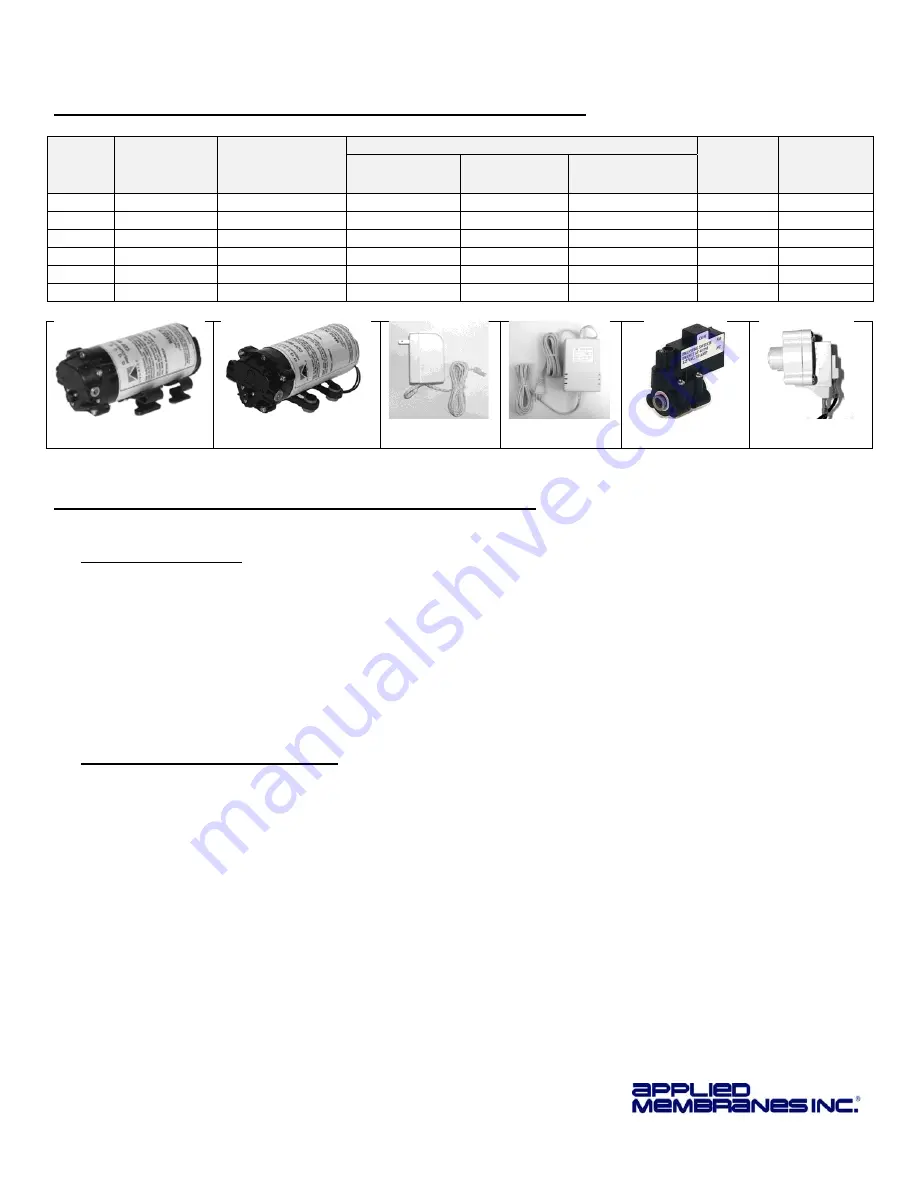
Installation and Service Manual – Under-the-Counter Point of Use 5 Stage Reverse Osmosis System with Booster Pump
Copyright © 2014 Applied Membranes, Inc.
All Rights Reserved.
Page 16
Replacement Pump & Pump Components
System
Flow
Rate
System
Model
Number
Replacement
Pump Model
Replacement Power Supply
Tank
Shut-Off
(TSO)
Low
Pressure
Switch
USA
(U)
Japan
(J)
European
(E)
12 GPD AAA-125P*
6840-2J03-B221 TAS114-19EP TAS104-19 TAS234-19EP PSW240 LPS340G
24 GPD AAA-245P*
6840-2J03-B221 TAS114-19EP TAS104-19 TAS234-19EP PSW240 LPS340G
36 GPD AAA-365P*
6840-2J03-B221 TAS114-19EP TAS104-19 TAS234-19EP PSW240 LPS340G
50 GPD AAA-505P*
8851-2J03-B423 TACS114-48 TACS104-48 TACS234-48RF PSW240 LPS340G
75 GPD AAA-755P*
8851-2J03-B423 TACS114-48 TACS104-48 TACS234-48RF PSW240 LPS340G
100
GPD
AAA-1005P* 8851-2J03-B423 TACS114-48 TACS104-48 TACS234-48RF PSW240 LPS340G
6840-2J03-B221
(6800 Series Low Flow Pump)
8851-2J03-B423
(8800 Series High Flow Pump)
TAS114-19EP
(6800 Power Supply)
TACS114-48
(8800 Power Supply)
PSW240
(Tank Shut Off Switch)
LPS340G
(Low Pressure Switch)
Pump Troubleshooting Information
1) The pump will not run:
a) Start at the source to determine where the electrical current flow has been interrupted. Use a multi-meter to check
the line voltage, and the transformer output. If the transformer is not functioning properly its current capacity may
have been exceeded. Replacement may be necessary.
b) If the transformer is properly sized, and is delivering the correct voltage to the system, remove the holding tank
pressure switch (PSW) from the system by disengaging both connectors, and connecting the pump directly to the
transformer.
i) If the pump now runs, the pressure switch is faulty, and needs adjusted or replaced.
ii) If the pump still fails to run, the electrical path has been interrupted within the motor, and should be replaced.
2)
The flow and/or pressure is too low:
Most Aquatec boost pumps are designed to limit the maximum output pressure to 110 psi, to protect the membrane
and other components from damage. The normal operating pressure as measured after the pump, and before the
membrane, will be approximately 80 psi. The flow rate of the 6800 series pump during operation is about 500 ml/min.
The 8800 is double that flow. If these parameters are not being met, please check the following:
a) Is the pump properly sized to handle the production rate of the membrane, plus the brine flow allowed by the
restrictor (usually 4 or 5 times the permeate production)?
b) Is the system receiving adequate feed water? The pump’s inlet chamber must be flooded to prevent performance
robbing air ingestion into the compression chambers.
c) Debris entering the pump may restrict the pumping operation. Consult the factory for valve cleaning instructions.